Распределенными параметрами
Спектр силы резания и внешних возмущений, вызванных неуравновешенностью заготовки, по данным исследований достигает 100 МГц. Если собственные частоты подвижного люнета и подсистемы инструмента в каждом конкретном случае могут быть приняты стабильными, то жесткость и спектр подсистемы маложесткой детали в связи с изменением положения зоны резания непрерывно меняется, что, в конечном счете, увеличивает вероятность резонанса на высших гармониках. Для реальных нелинейных систем оценить распределение энергии при резонансе по формам колебаний чрезвычайно трудно, поэтому трудно предсказать, какая из собственных форм колебаний окажет наибольшее влияние на поведение систем. Из практики известно, что виброустойчивость такой системы низка, и поэтому мехобработку ведут на очень низких скоростях, т.е. в квазистационарном режиме, что резко снижает производительность и не гарантирует точности мехобработки.
С целью повышения производительности и точности мехобработки маложестких деталей необходима разработка эффективных систем управления процессом, синтез которых основывается на современных методах управления технологическими процессами.
Расчеты частотных и точностных характеристик процесса мехобработки маложестких деталей базируются на общих закономерностях колебаний сложных механических систем. При этом широко применяется математический аппарат теории автоматического управления и, в частности, рассмотрение задач в комплексной области. Переход в комплексную область позволяет свести динамическую задачу для линейной системы при гармоническом возбуждении к квазистатической с комплексными коэффициентами, зависящими от частоты. Введение комплексных модулей упругости позволяет применить единый подход при рассмотрении вынужденных и собственных колебаний демпфированных и недемпфированных систем.
При расчетах сложных механических систем приходится упрощать расчетные модели отдельных деталей и узлов. Эти упрочнения идут по пути линеаризации подсистем и внешних нагрузок, замены гистерезисных потерь колебательной энергии в сочленениях деталей упруго вязкими, рассмотрение части подсистем, как абсолютно жестких и пренебрежения колебаниями по некоторым степеням свободы. Вместе с тем расчет динамических характеристик сложный систем имеет свои специфические задачи:
1. Оптимальное распределение системы на подсистемы.
2. Разработка расчетных моделей подсистем и накопление необходимой для них экспериментальной информации.
3. Создание моделей и алгоритмов расчета, обеспечивающих необходимую точность вычисления и соответствие результатов основным характеристикам реального процесса.
4. Оценка зависимости результатов расчета от точности задания исходной информации.
5. Создание алгоритмов расчета, обеспечивающих минимальное время вычислений на - ЭЦВМ и т.п.
С целью разработки системы автоматического управления точностью механической обработки маложестких деталей выделим в качестве объекта управления технологическую систему станка с учетом процесса резания. Из экспериментальных исследований обоснуем следующее разбиение технологической системы на подсистемы: 1. Деталь-опоры. 2. Суппортная группа. 3. Процесс резания. Исследует каждую из подсистем и на базе проведенного анализа объекта управления проведем исследование функциональных и структурных схем автоматического управления точностью мехобработки маложестких деталей.
Рассмотрим деталь как однородный стержень, закрепленный в произвольных опорах. Свободные изгибные колебания стержня без действия диссипативных сил описываются уравнением
. (2.26)
Когда стержень колеблется по собственным формам колебаний , его прогибы будут изменяться во времени по геометрическому закону
. (2.27)
Подставляя (2.27) в (2.26), получим для собственной формы уравнение
, (2.28)
где . (2.29)
Общее решение (2.28) можно записать в виде
, (2.30)
Формы кривых, описывающих прогибы, задаются нормальной функцией
. (2.31)
Таким образом, формы колебаний имеют вид синусоид.
Применим теперь метод нормальных форм колебаний к исследованию поперечных динамических перемещений стержней. Положим, что на вал действует распределенная поперечная сила N(x, t). В этом случае уравнение движения имеет вид:
. (2.32)
Будем искать решение в виде . Используя условия ортогональности и нормируемости собственных функций, получим
(2.33)
где . (2.34)
Будем изучать устойчивый процесс мехобработки (например, устойчивый процесс резания на токарном станке). Вынужденные колебания детали в плоскости YОХ под действием произвольной гармонической силы описывается уравнением.
. (3.35)
Здесь - жесткость при изгибе; - масса единицы длины детали; - поперечное смещение; и - коэффициенты внешнего и внутреннего трения.
Пусть к детали, закрепленной в шарнирных опорах, приложена сосредоточенная гармоническая сила на расстоянии от правой опоры, тогда решение примет вид
. (2.36)
Определим входную передаточную функцию
, (2.37)
где и - изображения по Лапласу соответственного перемещения и силы Р.
Используя (2.36), преобразуем (2.37) к стандартному виду
, (2.38)
где - постоянные времени; - коэффициенты усиления; - коэффициенты колебательности (демпфирования); - коэффициент поглощения.
Передаточная функция (2.38) реализуется параллельно соединенным звеньям направленного действия.
Количество звеньев схемы (число членов ряда 2.38), достаточное для достижения требуемой точности мехобработки, зависит от физических свойств ( ) и размеров ( ) детали, а также от близости зон частот вынужденных колебаний и собственных ( ), то достаточно оставить 2…3 члена.
Таким образом, передаточная функция подсистемы "деталь-опоры" с распределенными параметрами приводил к сумме нескольких стандартных звеньев с сосредоточенными параметрами, соединенных параллельно.
На рис.2.16 приведены АФЧХ подсистемы "деталь-опоры", определенные по формуле при следующих значениях исходных параметров: , м, Н/м, кг/м3.
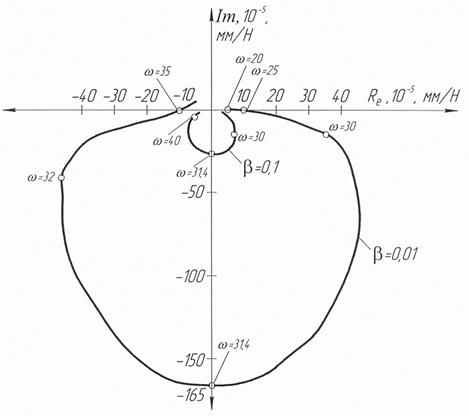
Рис.2.16. АФЧХ подсистемы «деталь-опоры»
Из построенных АФЧХ следует, что рассматриваемая подсистема является острорезонансной и практически описывается первым слагаемым сумм (2.38).
Динамическая характеристика резания как элемента динамической системы станка представляет собой зависимость изменения силы резания от вызвавшего это изменение относительного смещения заготовки и инструмента. Будем использовать динамическую характеристику резания, основанную на анализе полного выражения силы резания.
Это выражение силы, резания следует из эмпирических зависимостей и поэтому имеет определенные границы применения: в частности, оно не отражает особенностей замкнутой деформационной системы и ее сложных связей, присущих процессу резания. Однако, выражение силы резания позволяет обнаружить важные закономерности, составляющие основу динамической характеристики, которую можно рассматривать как первое приближение.
Динамическая характеристика процесса резания может быть построена только для условий, когда процесс является собственно устойчивым.
Для практических расчетов может быть использовано выражение динамической характеристики в форме:
, (2.39)
где - постоянная времени заднего угла; ; - постоянная времени переднего угла; - постоянная времени стружкообразования; - коэффициент резания, определяемый из выражения ; где удельная сила резания; - условное напряжение; - ширина срезаемого слоя; - усадка стружки.
Постоянные времени , , - можно оценить по известным приближенным зависимостям или по экспериментальным данным.
При анализе среднечастотной области характеристики в случае обработки с усадкой можно пользоваться упрощенным выражением .
В случае отсутствия автоколебаний процесс резания целесообразно описать квазистатической характеристикой .
Этому же соответствует и малость постоянных времени процесса резания по сравнению с постоянной времени упругой системы .
Теоретический анализ способов обработки нежестких деталей типа "вал-ротор" и анализ динамики системы СПИЗ как объекта управления показали, что одним из эффективных путей повышения точности обработки является разработка систем автоматического управления (САУ) точностью.
Потеря точности обработки маложестких деталей вызвана в первую очередь податливостью детали и низкой виброустойчивостью системы СПИЗ в рассматриваемых процессах. Поэтому, естественно, первым вариантом САУ точностью обработки рассматривается САУ положением обрабатываемой детали (и жесткости подсистемы "деталь-опоры") в зоне резания. САУ исследована и реализована как часть комплексной САУ точностью обработки жестких деталей в работах, где доказана работоспособность такой САУ для жестких деталей. Вместе с тем, рассмотренные САУ, компенсируя статистические упругие перемещения, не могут полностью скомпенсировать динамические упругие перемещения нежестких деталей в зоне резания и поэтому не обеспечивают требуемой точности обработки.
Можно показать, что высокий уровень динамических усилий (и как следствие, перемещений) в зоне резания вызывается имеющейся всегда неуравновешенностью нежесткой детали.
Неуравновешенность детали, состоящая в несовпадении оси вращения с осью инерции, связано с припуском на обработку и его колебаниями, погрешностями предыдущих операций и, особенно, центровочных операций, влиянием веса деталей и др.
Важным обстоятельством, обеспечивающим изучение влияния неуравновешенности маложестких деталей на точность обработки является следующее. Любая распределенная по длине вала неуравновешенность может быть разложена на составляющие, каждая из которых соответствует определенной форме упругой линии и вызывает вынужденные колебания только этой формы. Поэтому учет неуравновешенности маложестких деталей можно проводить по собственным формам. Так как частота вынужденных колебаний при обработке нежестких валов, как правило, значительно меньше частоты собственных колебаний подсистемы "деталь-опоры", то для оценки неуравновешенности достаточно учитывать не более трех первых собственных форм, а при определенных условиях достаточно учесть первую собственную форму.
Под действием сил инерции и неуравновешенности нежесткий "вал-ротор" в процессе обработки изгибается по пространственной кривой, представляющей наложение гармоник последовательных порядков. Плоскости гармоник, вообще говоря различны. Совокупность плоскостей с лежащими в них гармониками, образует как бы "жесткую" конфигурацию, вращающуюся с валом. При изменении угловой скорости нарушаются соотношения модулей и фаз гармоник.
Динамические реакции в опорах и в зоне резания (как было показано выше, воздействие процесса резания на обрабатываемый нежесткий вал может быть заменено при определенных условиях, эквивалентной упругой опорой) можно разбить на слагаемые, соответствующие отдельным гармоникам, лежащие в плоскостях этих гармоник и вращающиеся с угловой скоростью.
Модуль амплитуды динамической составляющей можно найти по формуле
, (2.40)
где использованы обозначения:
; ; ; .
Здесь - собственная функция соответствующей недемпфированной системы; - результирующая неуравновешенность; - коэффициент пропорциональности в линейной силе трения.
Анализ формулы показывает, что величина опорных реакций сильно зависит от угловой скорости, ширина диапазонов резонансных колебаний растет с номером . Поэтому на высших критических скоростях вибрации, как правило, имеют более интенсивный характер, чем на низших, даже несмотря на уменьшение коэффициентов с ростом . Из сказанного следует, что для стабилизации процесса резания и, следовательно, повышения точности обработки маложестких деталей надо стабилизировать оси или управлять положением оси вала с целью повышения точности обработки. Таким образом, мы обращаемся ко второму варианту САУ точностью обработки, представляющую многократную систему управления, связанную через объект, которая управляет положением оси и колебаниями детали в точке управления. Количество точек управления и соответственно контуров системы управления, выбирается в зависимости от податливости детали и требуемой точности обработки в статическом режиме.
Следует заметить, что повышение точности обработки немыслимо без снижения уровня вибраций при резании. Следовательно, ставится вопрос о создании особого класса систем управления, обеспечивающих оптимизацию динамических характеристик системы СПИЗ в процессе резания.
При разработке контура управления возникает вопрос о выборе его входного и выходного сигналов. Очевидно, что в задачах, связанных с точностью управления, выходом объекта управления подсистемы "деталь-опоры" должно быть перемещение оси детали и амплитуды колебаний детали относительно принятой базы. Входом же в объект управления могут быть управляющие усилия или управляющие перемещения.
На рис.2.17 представлена многоконтурная, многосвязная система управления с тремя точками входа и выхода в объект управления, выходом которого является перемещение оси детали, а входом - управляющее усилие. Связи контуров осуществляются через объект и введенные в рассмотрение передаточные функции объекта управления . В сечении 1 на объект действует сила резания , сила, связанная с неуравновешенностью вала и управляющее усилие , которые суммируются со своими знаками, образуя силу . Сила воздействуя на объект через передаточную функцию , вызывает смещение оси детали в сечении 1 . Результирующие усилия и , действующие соответственно в сечениях 2 и 3, вызывают в сечении 1 через передаточные функции и смещение оси и . Полное смещение (или амплитуду колебаний оси детали в сечении 1 получаем сложением слагаемых , , .
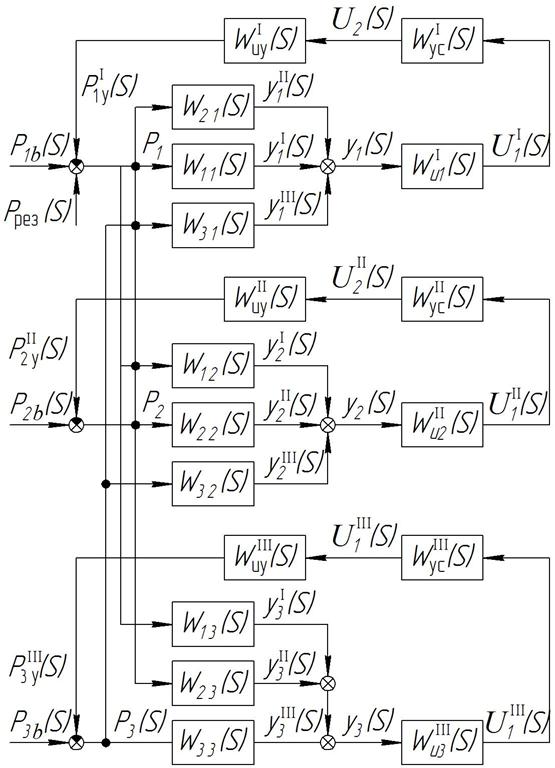
Рис.2.17. Структурная схема многоконтурной САУ обработкой длинномерных маложестких заготовок
В теоретическом варианте рассматриваемая САУ точностью обработки нежестких деталей в сечении 1 может быть представлена следующими звеньями: датчиком малых перемещений с передаточной функцией входом которого является перемещение (амплитуда) оси детали в сечении 1 , а выходом напряжение ; усилителя ; который усиливает сигнал датчика до уровня ; исполнительного устройства , включенного на выход усилителя и преобразующего его сигнал в управляющее усилие . Аналогично устроены каналы управления в сечениях 2 и 3.
Теоретический анализ структурной схемы управления, представленной на рис.2.17, обнаружил следующие недостатки: 1) управляющие усилия и управляемые смещения оказались в разных точках управления, что вызывает дополнительное запаздывание управления; 2) известно, что для достижения эффективности управления целесообразно управлять перемещениями детали (управление отклоненной оси); 3) влияние управляющих воздействий в сечениях 2... на сечения резания 1, зависит от состояния управления в сечении 2; 4) отличительной особенностью рассматриваемой САУ является то обстоятельство, что стабилизация положения оси детали в сечениях 2... п, увеличивает жесткость подсистемы "деталь-опоры" и снижает уровень колебаний в сечении резания 1, т.е. контуры управления 2, 3... образуют отрицательную обратную связь для контура 1, что не следует из рассматриваемой структурной схемы; 5) в САУ точностью обработки перемещение детали является информативным фактором, обеспечивающим цели управления.
Указанных недостатков не имеет схема управления, где входом и выходом в объекте управления являются перемещения оси детали (и амплитуда колебаний детали). Перейдем к анализу такой схемы, представленной на рис.2.18, причем, как следует из сказанного выше, достаточно рассмотреть два канала управления в сечениях 1 и 2. Рассматриваемая система представляет собой двухканальную систему с идентичными каналами. Здесь и известные передаточные функции объекта управления, - передаточная функция управляющего устройства в идентичных каналах.
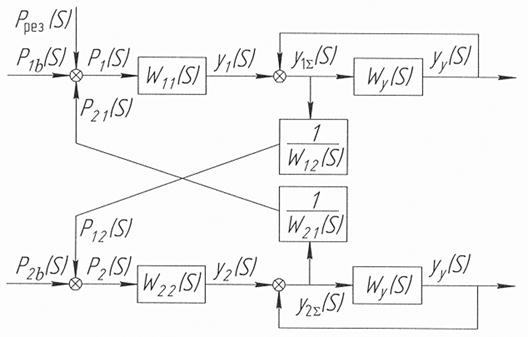
Рис.2.18. Структурная схема многоконтурной САУ перемещениями заготовки – двухканальной системы с идентичными каналами
Будем предполагать выполненными необходимые и достаточные условия того, чтобы в системе со связанными между собой через объект управляемыми величинами можно было в каждом контуре управления неограниченно увеличивать коэффициент усиления без нарушения устойчивости в каждом контуре и во всей системе в целом:
а) каждая отдельная система без учета взаимовлияния других контуров управления имела структуру, устойчивую при сколь угодно большом коэффициенте усиления;
б) вырожденное и вспомогательное уравнения для всей многосвязной системы, каждое в отдельности, удовлетворяли условиям устойчивости.
Для повышения устойчивости и качества управления в двухканальных системах получили широкое распространение обратные перекрестные связи между каналами, т.е. связи, имеющие равные, но обратные по знаку, передаточные функции. Обратная связь передает воздействие с выхода одного звена в одном канале на вход идентичного звена в другом канале (связи и , ) рис.2.18.
Прямые перекрестные связи, когда воздействие передается с входа одного звена в одном канале на выход идентичного звена в другом канале, осуществляются самим объектом управления. Комбинация же прямых и обратных связей дает весьма сильный положительный эффект.
Далее, исходя из общих усилий устойчивости системы связями через объект управления и того обстоятельства, что контуры управления в рассматриваемой системе образуют друг по отношению к другу отрицательную обратную связь, мы переходим к теоретическому анализу одного канала системы управления приложенного в сечении резания и представленного на рис.2.19.
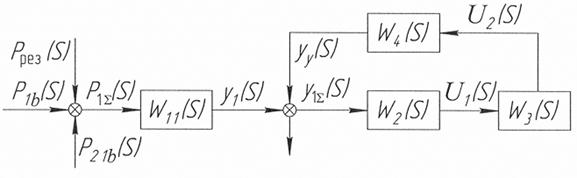
Рис.2.19. Канал САУ в сечении резания
Здесь на вход объекта управления прикладывается усилие , слагаемыми которого являются эквивалентная сила резания , возмущение в сечении 1 и возмущение, передаваемое с выхода второго канала Система управления представлена тремя звеньями: 1) датчиком малых перемещений с передаточной функцией , выходом которого является напряжение ; 2) усилителем , который усиливает сигнал до уровня ; 3) исполнительного механизма , который преобразует сигнал в перемещении оси детали.
Для анализа такой системы управления составим общую передаточную функцию цепи обратной связи
. (2.41)
Передаточная функция объекта с встроенным контуром управления
. (2.42)
АФЧХ системы в целом и объекта, рассчитанные при следующих исходных данных: ; м; м; Н/м; кг/м3 - показаны на рис.2.20. Из сопоставления АФЧХ объекта без регулятора (годограф I) и системы в целом (годограф II) видно, что введение контура управления уменьшает радиус-вектор годографа в 2...2,5 раза на частотах 0...30 Гц. Следует отметить, что задача ставится об управлении положением оси и амплитуды колебаний детали, когда внешняя сила изменяется с частотами 0...30 Гц, если процесс резания носит квазистатический характер. Введение контура управления подобного типа, как показали эксперименты, проведенные на лабораторной установке, позволяет компенсировать перемещение оси маложесткой детали и уменьшить амплитуду ее колебаний в 2... 3 раза. Фиксируя статическое положение оси детали и поддерживая ее в процессе механической обработки, можно повысить точность формы в продольном и поперечном направлениях в 2,5...3 раза. В то же время описанная система позволяет повысить запас устойчивости по глубине резания в 5...6 раз.
Дата добавления: 2015-01-18 | Просмотры: 809 | Нарушение авторских прав
1 | 2 | 3 | 4 | 5 | 6 | 7 | 8 | 9 | 10 | 11 | 12 |
|