АкушерствоАнатомияАнестезиологияВакцинопрофилактикаВалеологияВетеринарияГигиенаЗаболеванияИммунологияКардиологияНеврологияНефрологияОнкологияОториноларингологияОфтальмологияПаразитологияПедиатрияПервая помощьПсихиатрияПульмонологияРеанимацияРевматологияСтоматологияТерапияТоксикологияТравматологияУрологияФармакологияФармацевтикаФизиотерапияФтизиатрияХирургияЭндокринологияЭпидемиология
|
Исследование процесса подготовки к помолу зерна твердой пшеницы белорусской селекции
4.2.1 Исследование возможности удаления мелкой фракции зерна
Анализ литературных источников показал, что в существующих технологических схемах подготовки к макаронному помолу твердой пшеницы отбор мелкой фракции зерна проводят после очистки и кондиционорования. В данном случае номер сита для отбора такой фракции устанавливают в зависимости от фактического качества перерабатываемого зерна. Отобранная партия мелкой фракции зерна не подлежит хранению вследствие высокой влажности (порядка 16%). Данная партия направляется в размольное отделение и измельчается на спецсистеме, промежуточные продукты которой поступают по технологической схеме помола на системы второго качества.
Для наиболее эффективного использования мелкой фракции зерна твердой пшеницы было принято решение об исследовании возможности удаления его перед этапом ГТО с последующим использованием такого зерна в крупяном производстве.
Для решения данной задачи определяли содержание мелких фракций (проход сита 2,2х20 и 2,5х20) в исследуемом зерне, оценивали качество полученных фракций зерна и исследовали влияние удаления мелких фракций, полученных проходами указанных сит, на выход и зольность круподунстовых продуктов.
Содержание мелких фракций в исследуемом зерне твердой пшеницы белорусской селекции, согласно ситовому анализу, приведено в таблице 14.
Таблица 14 – Процентное содержание мелкой фракции в зерне твердой пшеницы различных сортов (проход сита 2,2х20 и 2,5х20/ сход сита 1,7х20)
Наименование сорта
| Содержание мелкой фракции 2,2х20
1,7х20
| Содержание мелкой фракции 2,5х20
1,7х20
| Вероника
| 4,36
| 24,20
| Славица
| 3,19
| 18,39
| Розалия
| 0,87
| 8,52
|
Анализ полученных данных показал, что в исследуемом зерне содержание мелкой фракции 2,2х20/1,7х20 не превышает 5 %. Наименьшее содержание данной фракции у сорта Розалия. При установлении проходового сита 2,5х20 содержание мелкой фракции для сортов Вероника и Славица значительно увеличивается и составляет соответственно 24,2% и 18,4%. Для сорта Розалия увеличение данного показателя незначительно и составляет 8,5%.
Таким образом, на основании полученных данных для исследуемого зерна целесообразно устанавливать сито для удаления мелкой фракции зерна размером 2,2х20.
Удаление мелкой фракции зерна потенциально увеличивает выход и качество макаронной крупка, поэтому далее в работе поочередно удаляли мелкие фракции 2,2х20 и 2,5х20, проводили ГТО полученных образцов зерна и размалывали данные образцы на трех драных системах. Определяли выход и зольность полученных круподунстовых продуктов.
Результаты исследований представлены в таблицах 15, 16 и на рисунках 25 - 38.
Таблица 15 – Выход круподунстовых продуктов и муки при помоле зерна твердой пшеницы без отбора и с отбором мелкой фракции
Наиме-
нование
продуктов
размола
| Наименование сорта
| Розалия
| Вероника
| Славица
| без отбора
| с отбором 2,2*20
| с отбором 2,5*20
| без отбора
| с отбором 2,2*20
| с отбором 2,5*20
| без отбора
| с отбором 2,2*20
| с отбором 2,5*20
| Крупная крупка
| 8,7
| 9,0
| 10,5
| 8,3
| 9,5
| 11,4
| 8,1
| 8,7
| 9,5
| Средняя крупка
| 14,7
| 15,3
| 16,1
| 14,0
| 14,6
| 16,1
| 14,8
| 15,2
| 16,0
| Мелкая крупка
| 12,9
| 13,5
| 15,3
| 13,2
| 13,8
| 15,3
| 13,1
| 13,6
| 15,5
| Жесткий дунст
| 16,4
| 16,6
| 17,0
| 15,0
| 15,2
| 16,4
| 15,5
| 15,8
| 16,3
| Мягкий дунст
| 11,8
| 11,7
| 12,0
| 11,7
| 11,7
| 12,1
| 11,3
| 11,5
| 11,7
| Мука
| 8,5
| 8,0
| 7,0
| 8,0
| 7,8
| 8,0
| 9,1
| 9,0
| 9,2
| Общий выход
| 73,0
| 74,1
| 77,9
| 70,2
| 72,6
| 79,3
| 71,9
| 73,8
| 78,2
| Макаронная крупка
| 52,7
| 54,4
| 58,9
| 50,5
| 53,1
| 59,2
| 51,5
| 53,3
| 57,3
|
Таблица 16 – Зольность круподунстовых продуктов, муки при помоле зерна твердой пшеницы без отбора и с отбором мелкой фракции
Наиме-
нование
продуктов
размола
| Наименование сорта
| Розалия
| Вероника
| Славица
| без отбора
| с отбором 2,2*20
| с отбором 2,5*20
| без отбора
| с отбором 2,2*20
| с отбором 2,5*20
| без отбора
| с отбором 2,2*20
| с отбором 2,5*20
| Крупная крупка
| 1,83
| 1,8
| 1,79
| 1,8
| 1,75
| 1,69
| 1,87
| 1,83
| 1,79
| Средняя крупка
| 1,38
| 1,35
| 1,3
| 1,47
| 1,4
| 1,35
| 1,49
| 1,42
| 1,4
| Мелкая крупка
| 1,25
| 1,21
| 1,17
| 1,31
| 1,28
| 1,2
| 1,38
| 1,35
| 1,29
| Жесткий дунст
| 1,2
| 1,18
| 1,16
| 1,24
| 1,23
| 1,13
| 1,19
| 1,16
| 1,11
| Мягкий дунст
| 1,08
| 1,07
| 1,05
| 1,05
| 1,02
| 0,97
| 1,0
| 0,98
| 0,96
| Мука
| 0,85
| 0,83
| 0,8
| 0,89
| 0,81
| 0,75
| 0,87
| 0,83
| 0,75
| Средневзве-
шенная зо-
льность
| 1,26
| 1,24
| 1,23
| 1,29
| 1,26
| 1,21
| 1,29
| 1,26
| 1,22
| 1,37
| 1,34
| 1,31
| 1,41
| 1,38
| 1,32
| 1,43
| 1,39
| 1,35
|
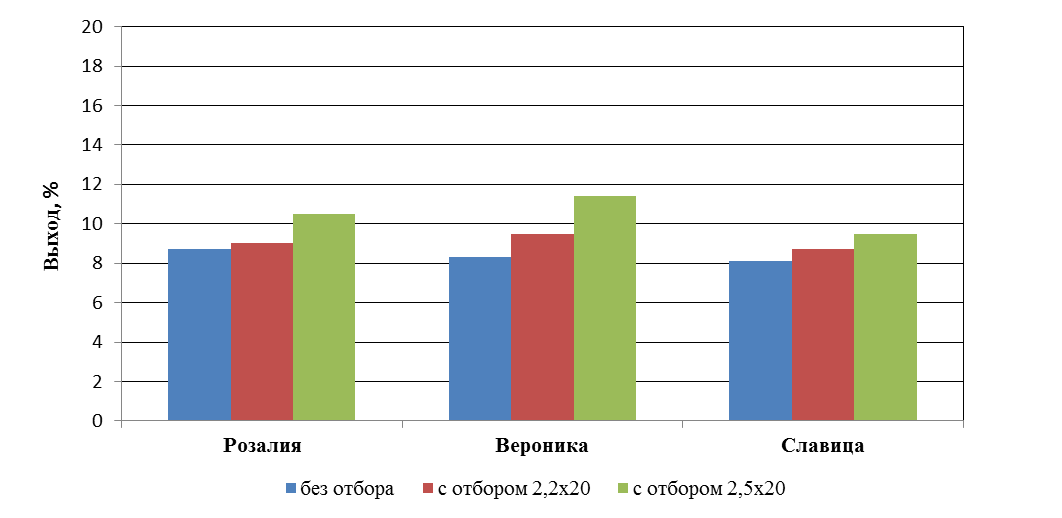
Рисунок 25 - Выход крупной крупки зерна твердой пшеницы белорусской селекции
В результате исследования было установлено, что с отбором мелкой фракции зерна для всех исследуемых сортов выход крупной крупки увеличивается. Удаление мелкой фракции 2,2х20 ведет к увеличению выхода крупной крупки на 0,3-0,8%, удаление фракции 2,5х20 приводит к увеличению выхода крупной крупки на 1,8-3,1%. В среднем выход крупной крупки ниже ориентировочных выходов, указанных в Правилах организации и ведения технологических процессов на мукомольных заводах, что может быть связано с особенностью кинематических параметров лабораторной мельницы, не предназначенной для макаронного помола.
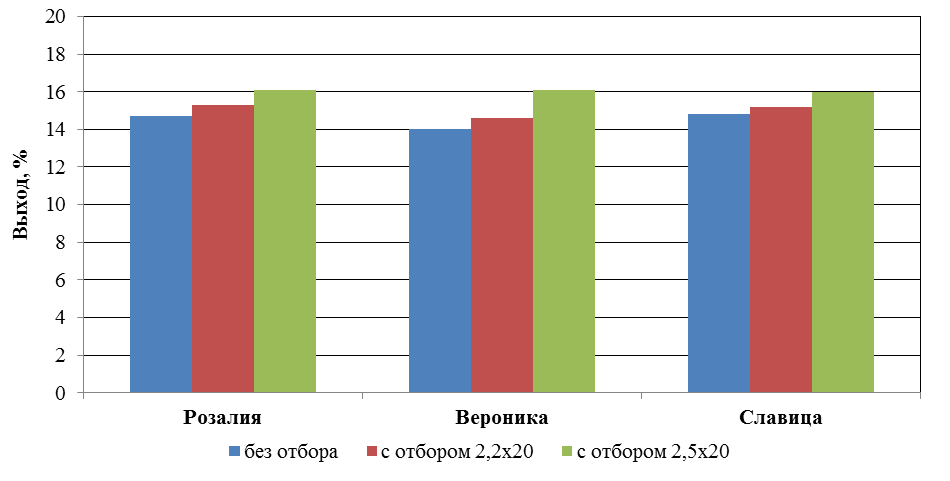
Рисунок 26 - Выход средней крупки зерна твердой пшеницы белорусской селекции

Рисунок 27 - Выход мелкой крупки зерна твердой пшеницы белорусской селекции
Анализируя данные по выходу средней и мелкой крупки следует отметить, что, как и для крупной крупки, удалением мелких фракций зерна приводит к увеличения выхода как средней, так и мелкой крупок. Увеличение выхода для средней и мелкой крупки при удалении фракции 2,2х20 менее значительно и составляет 0,4-0,6%. Увеличение выхода при удалении фракции 2,5х20 составляет для средней крупки 1,2-2,1%, для мелкой крупки 2,1-2,4%.
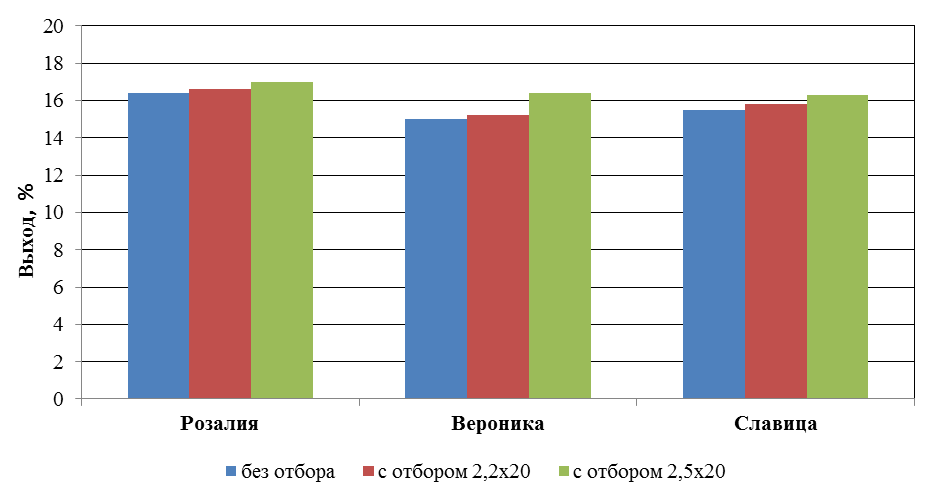
Рисунок 28 - Выход жесткого дунста зерна твердой пшеницы белорусской селекции
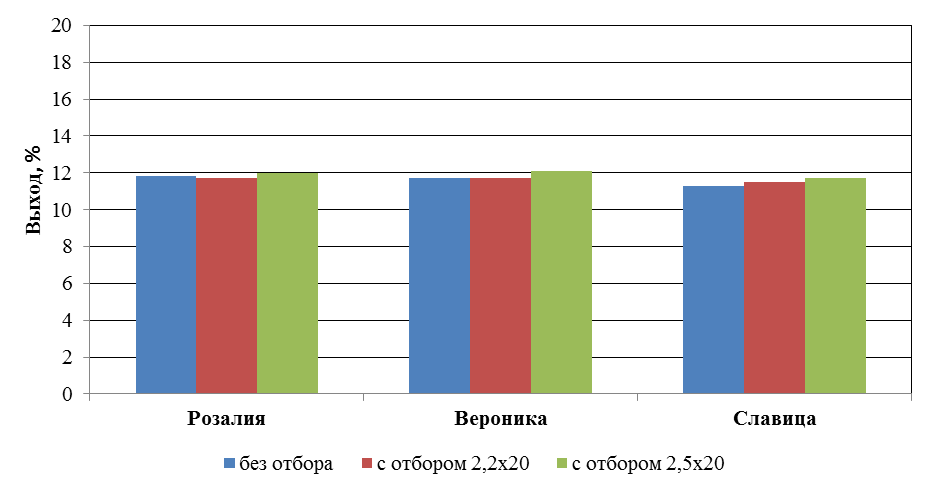
Рисунок 29 - Выход мягкого дунста зерна твердой пшеницы белорусской селекции
Из рисунков 27, 28 видно, что при удалении мелких фракций 2,2х20 и 2,5х20 при помоле зерна твердой пшеницы, выход жесткого дунста увеличивается на 0,2-0,3% и 0,6-1,4% соответственно. Увеличение выхода мягкого дунста при удалении тех же фракций не происходит либо незначительно (0,2-0,4%).
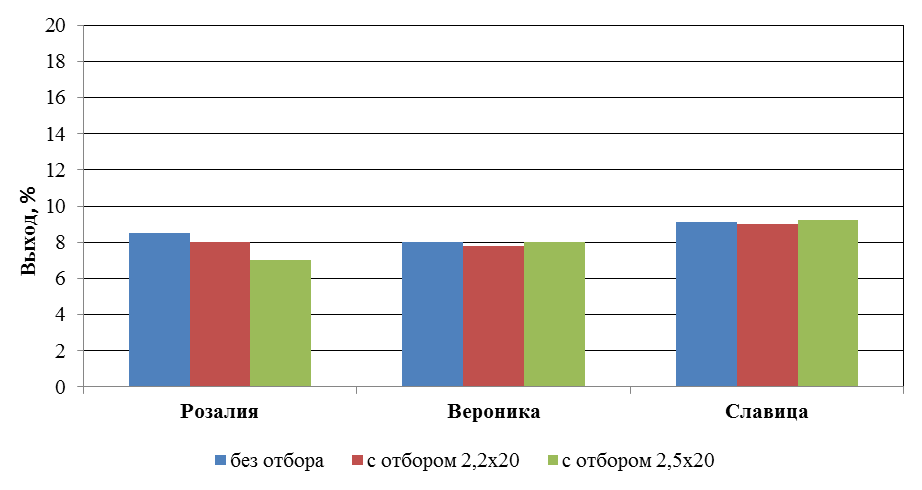
Рисунок 30 - Выход муки при помоле зерна твердой пшеницы белорусской селекции
Ориентировочный выход муки при макаронных помолах, согласно Правил организации и ведения технологических процессов на мукомольных заводах, должен составлять 3-4%. В результате исследований было установлено, что фактический выход муки для всех исследуемых сортов превышает рекомендуемый на 4-5%. После удаления мелких фракций выход муки незначительно снижается для сорта Розалия (на 0,5-1,5%), для сортов Вероника и Славица - практически не изменяется.
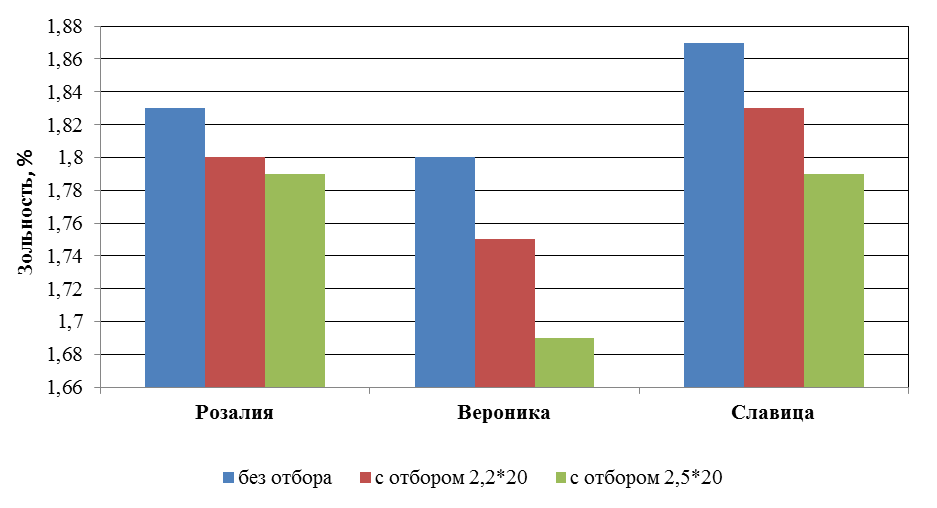
Рисунок 31 – Зольность крупной крупки, полученной при помоле зерна твердой пшеницы
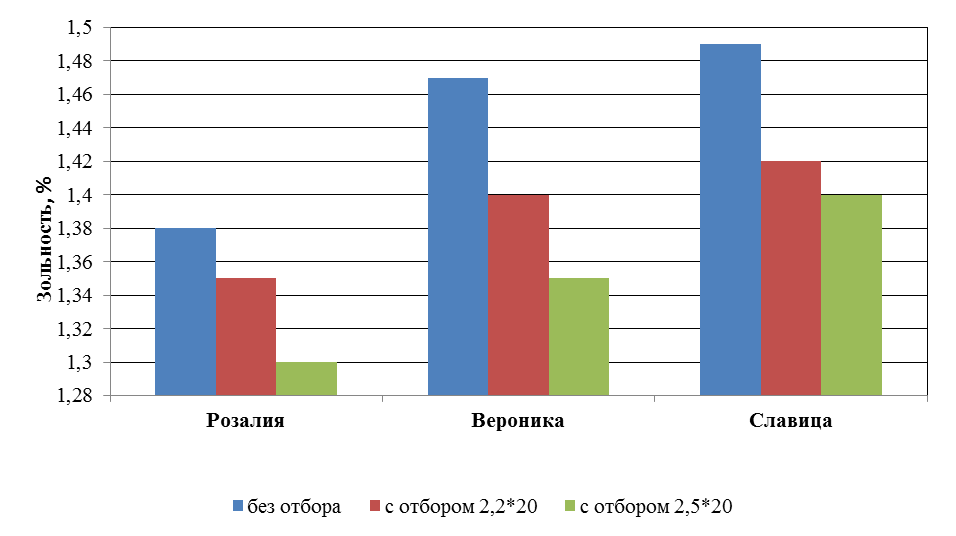
Рисунок 32– Зольность средней крупки, полученной при помоле зерна твердой пшеницы
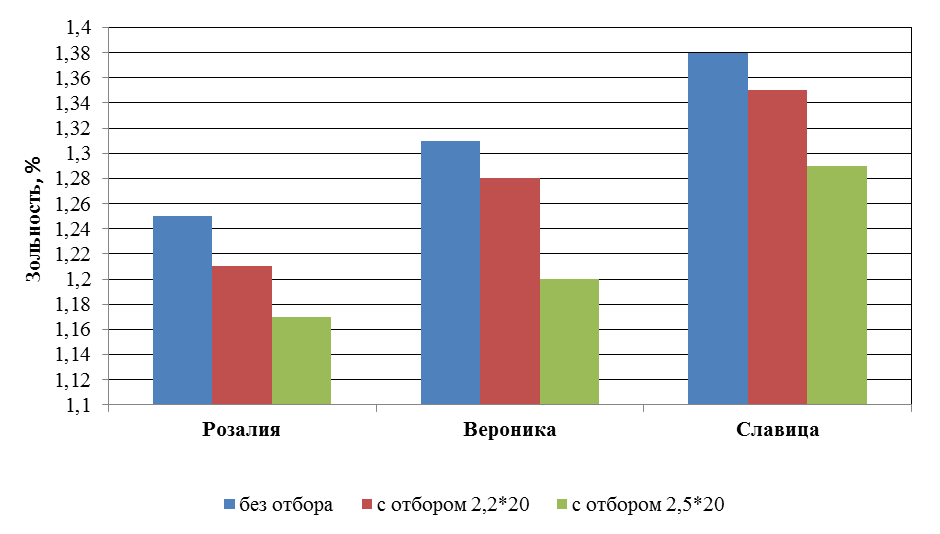
Рисунок 33 – Зольность мелкой крупки, полученной при помоле зерна твердой пшеницы
В результате исследования изменения зольности крупок, полученных при помоле зерна твердой пшеницы, было установлено, что динамика снижения зольности для крупной, средней и мелкой крупок после удаления мелких фракций зерна для всех сортов практически одинакова. Следует также отметить, что, чем выше процентное содержание мелкой фракции в зерне, тем интенсивнее снижается зольность крупок, полученных при помоле зерна после удаления данных фракций.
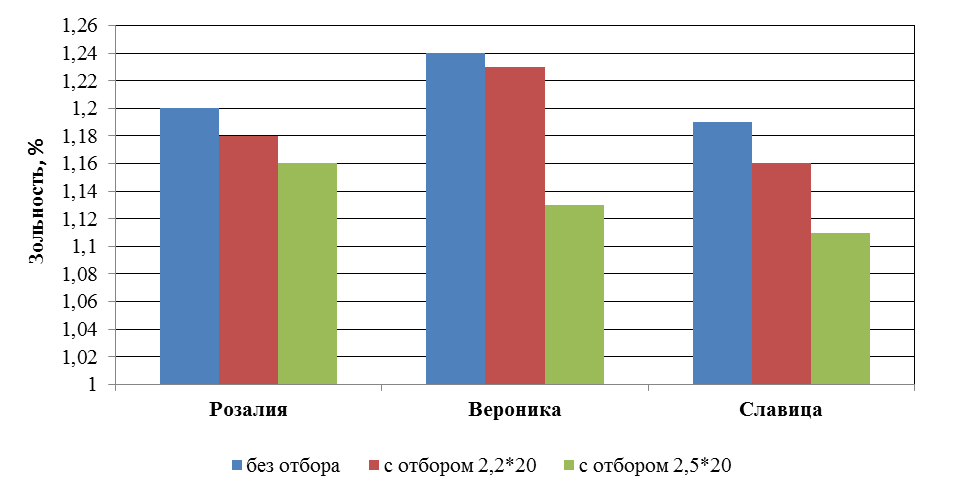
Рисунок 34 – Зольность жесткого дунста, полученного при помоле зерна твердой пшеницы
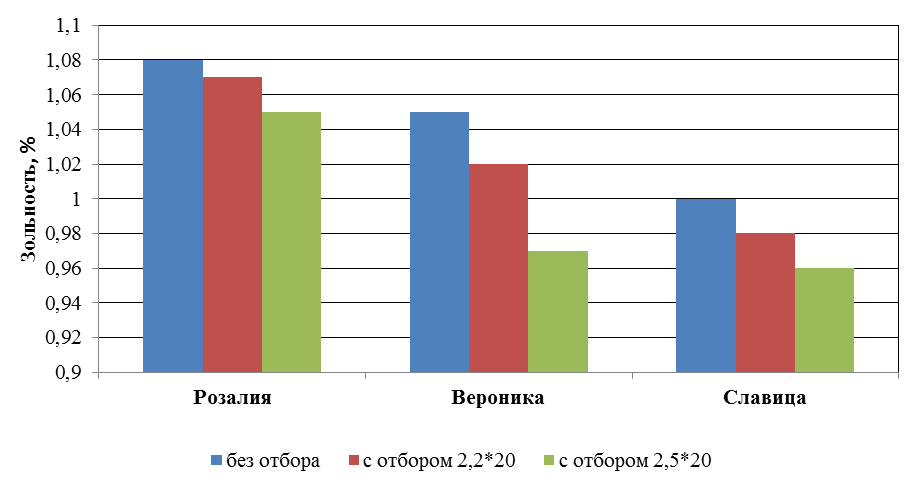
Рисунок 35 – Зольность мягкого дунста, полученного при помоле зерна твердой пшеницы
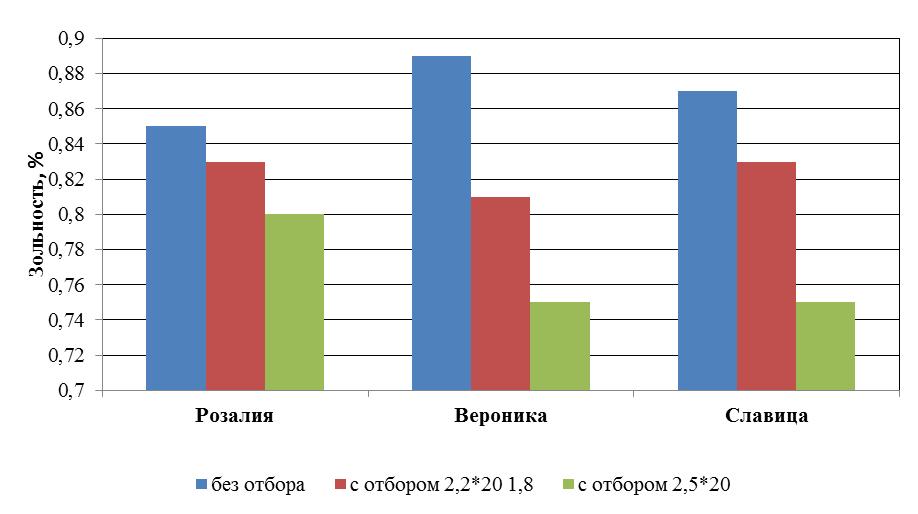
Рисунок 36 – Зольность муки, полученной при помоле зерна твердой пшеницы
При анализе изменения зольности дунстов и муки при помоле зерна твердой пшеницы было установлено, что для всех исследуемых сортов после удаления мелкой фракции зерна зольность дунстов и муки снижается. Для сорта Розалия степень снижения незначительна и составляет 0,01-0,05%. Для сортов Вероника степень снижения составляет от 0,01-0,09% (для жесткого дунста) до 0,8-0,14% (для муки), для сорта Славица от 0,02-0,04% (для мягкого дунста) до 0,05-0,13% (для муки).
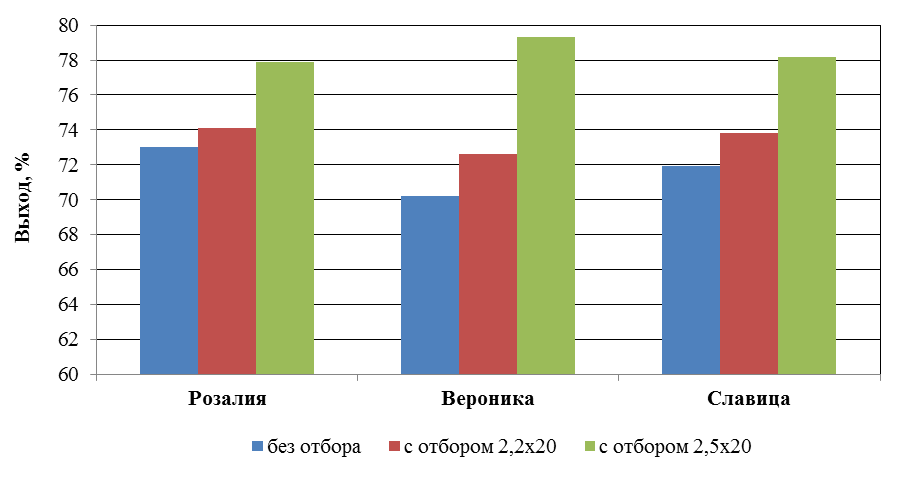
Рисунок 37 - Общий выход продуктов размола зерна, полученных при помоле зерна твердой пшеницы
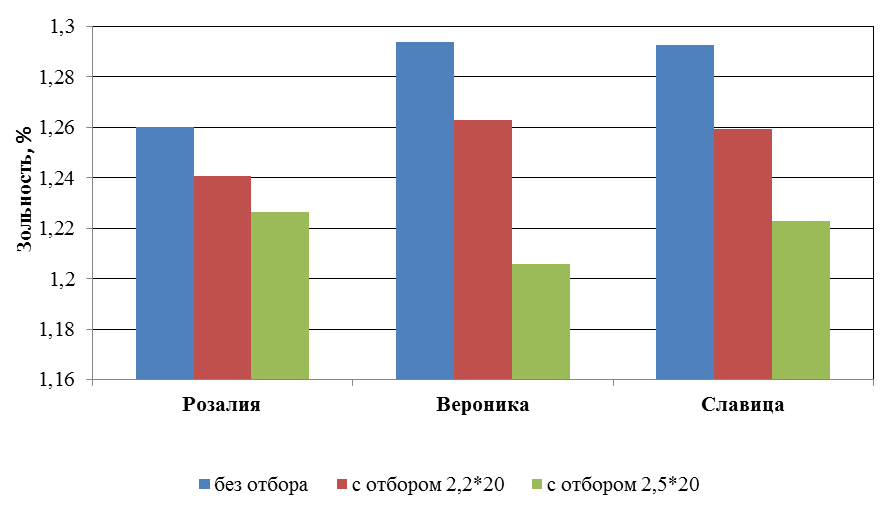
Рисунок 38 - Средневзвешенная зольность продуктов размола зерна, полученных при помоле зерна твердой пшеницы
Таким образом, в результате исследований было установлено, что удаление мелкой фракции зерна влияет как на выход, так и на зольность полученных продуктов. Анализ полученных данных показал, что при удалении мелкой фракции зерна проходом сита 2,2х20 выход круподунстовых продуктов и муки увеличивается на 1,1-1,8%, зольность снижается на 0,02-0,04%. При удалении мелкой фракции зерна проходом сита 2,5х20 общий выход круподунствоых продуктов и муки увеличился на 5-9%, степень снижения зольности составила 0,04-0,12%. Было также установлено, что чем больше массовая доля мелкой фракции в зерне, тем значительнее увеличивается выход продуктов помола и тем интенсивнее снижается средневзвешенная зольность продуктов, полученных при помоле зерна после удаления данных фракций.
4.2.2 Исследование возможности применение шелушильно-шлифовальных машин для сухой обработки поверхности зерна твердой пшеницы
Сухая обработка поверхности зерна твердой пшеницы имеет огромное значение в технологии подготовки зерна к помолу. В процессе шелушения с поверхности зерна удаляется значительная часть оболочек, частицы пыли, микроорганизмы, а сама зерновая масса дополнительно очищается от большинства содержащихся в ней примесей. Шелушение помогает понизить зольность и улучшить качество. При отделении оболочек от зерен содержание клетчатки как соответственно и зольность готового продукта уменьшаются. Поэтому зерно пшеницы должно приобретать более высокие мукомольные характеристики, что положительным образом сказывается на результатах помолов, особенно сортовых.
Обработку поверхности зерна мягкой пшеницы при сортовых помолах осуществляют сухим способом, который предусматривает обработку поверхности зерна в обоечных, щеточных, шелушильных машинах.
Эффективность обработки поверхности зерна характеризуется снижением его зольности при ограничении увеличения количества битых зерен. В таблице 17 приведены ориентировочные значения показателей эффективности обработки зерна в различных машинах.
Таблица 17 – Эффективность обработки поверхности зерна в машинах разного типа
Типы машин
| Снижение зольности, %
| Увеличение количества битых зерен, не более, %
| Обоечные машины с абразивным цилиндром, шелушильные машины
| 0,03 – 0,06
|
| Обоечные машины с металлическим сетчатым цилиндром, щеточные машины
| 0,01 – 0,03
|
|
При переработке твердой пшеницы Правилами организации и ведения технологического процесса на мукомольных заводах рекомендовано обрабатывать поверхность только один раз преимущественно после ГТО. Сухая обработка поверхности зерна в обоечных машинах перед ГТО для зерна твердой пшеницы исключается из-за высокого выхода битых зерен, обусловленного высокой хрупкостью высокостекловидного эндосперма зерна.
В данной работе была исследована возможность проведения первичной сухой обработки поверхности зерна в шелушильно-шлифовальных машинах.
4.2.2.1 Исследование влияния длительности шелушения на выход продуктов шелушения и снижение зольности шелушенного зерна
Исследуемое зерно шелушили на лабораторном шелушителе УШЗ-1, имитирующем шелушение зерна в производственных условиях на машинах типа ЗШН. Длительность шелушения зерна была выбрана от 5 до 90 секунд. На первом этапе работы исследовали влияние длительности шелушения на выход продуктов шелушения: битых зерен, мучки и шелушенного зерна.
Результаты исследования представлены в таблице 18.
Таблица 18 - Изменение количества битых зерен и выхода мучки в зависимости от длительности обработки
Выход продуктов, %
| Длительность шелушения, сек
|
|
|
|
|
|
|
| Сорт Розалия
| мучка
| 1,50
| 3,02
| 5,30
| 7,20
| 7,82
| 9,02
| 13,70
| битые зерна
| 0,60
| 1,15
| 1,52
| 1,98
| 2,60
| 2,75
| 3,10
| Сорт Славица
| мучка
| 1,35
| 2,95
| 5,20
| 7,30
| 7,65
| 8,63
| 14,05
| битые зерна
| 0,52
| 0,95
| 1,41
| 2,01
| 2,24
| 2,60
| 3,25
| Сорт Вероника
| мучка
| 1,69
| 3,88
| 5,90
| 7,05
| 8,12
| 9,65
| 14,21
| битые зерна
| 0,65
| 1,20
| 1,45
| 1,85
| 2,54
| 2,80
| 3,30
|
Из таблицы видно, что выход битого зерна и мучки при обработке поверхности с увеличением длительности шелушения возрастает, за счет чего выход шелушенного зерна уменьшается. Результаты исследования показали, что при увеличении времени обработки увеличивается выход как мучки, так и битого зерна. Следует отметить, что с увеличением времени обработки интенсивность прироста мучки значительно превышает прирост битого зерна. Правилами организации и ведения технологических процессов на мукомольных заводах ограничивается количество битых зерен при обработке поверхности зерна до 2%. Данное ограничение соблюдается при длительности шелушения до 20-30 секунд.
Далее в работе исследовали влияние длительности шелушения на изменение зольности шелушенного зерна и мучки.
Результаты представлены на рисунках 39, 40.
| Рисунок 39 – Изменение зольности шелушенного зерна в зависимости от длительности шелушения
| 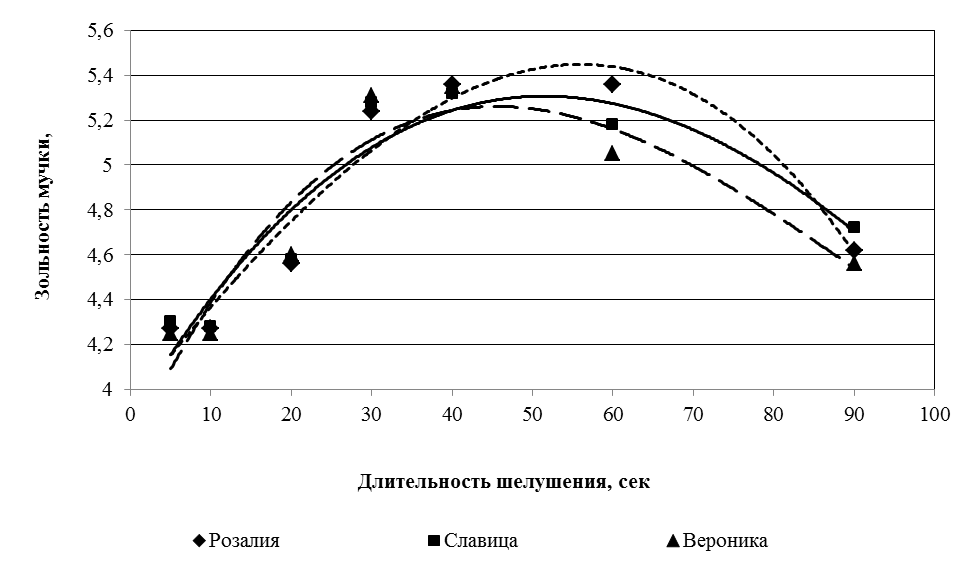
Рисунок 40 - Изменение зольности мучки в зависимости от длительности шелушения
Начальная зольность зерна составляла 2-2,1%. Из рисунка видно, что с увеличением длительности шелушения зольность зерна значительно снижается и после 90 сек шелушения составляет уже 1,45-1,58 %. Повышение зольности мучки наблюдается при продолжительности шелушения до 40 секунд. При дальнейшем увеличении длительности шелушения зольность мучки несколько снижается, что свидетельствует об интенсификации процесса шелушения и перехода в мучку внутренних слоев зерновки – алейронового слоя и эндосперма. Следует также отметить, что при ранее установленной длительности шелушения до 30 секунд, при которой соблюдается ограничение по приросту битых зерен, снижение зольности составляет 0,15-0,2%, что значительно превышает данный показатель при обработке в обоечной машине (0,03-0,04%).
На основании проведенных исследований можно сделать вывод, что оптимальной длительностью шелушения, при которой соблюдается ограничение по количеству битых зерен, является время до 20 секунд. При этом наблюдается снижение зольности на 0,15%.
4.2.3 Исследование влияния длительности шелушения на степень удаления зародыша
При обработке поверхности зерна пшеницы сухим способом происходит не только удаление оболочек, но и частичное удаление зародыша. Удаление зародыша приводит к уменьшению ферментативной активности и увеличению сроков хранения готовой продукции. Зародыш характеризуется высоким содержанием жира, богатого ненасыщенными жирными кислотами, которые быстро окисляются, что вызывает прогоркание готовой продукции и приобретение ей неприятного вкуса и запаха.
О степени удаления зародыша можно судить косвенно по показателю энергии прорастания.
Энергия прорастания – это способность семян быстро и дружно прорастать, её выражают в процентах (%).
При определении энергии прорастания были исследованы шесть образцов твердой пшеницы белоруской селекции с временем шелушения в машине типа ЗШН от 0 до 60 сек. Определение данного показателя проводили способом проращивания зерна в рулонах. Данные полученные в результате опыта представлены в таблице 19 и на рисунке 41.
Таблица 19 - Влияния длительности шелушения на энергию прорастания
Время шелушения, сек
| Количество проросших зерен, шт
| Количество загнив-ших зерен, шт
| Энергия прорастания, %
|
|
|
|
|
|
|
|
|
|
|
|
|
|
|
|
|
|
|
|
|
|
|
|
|
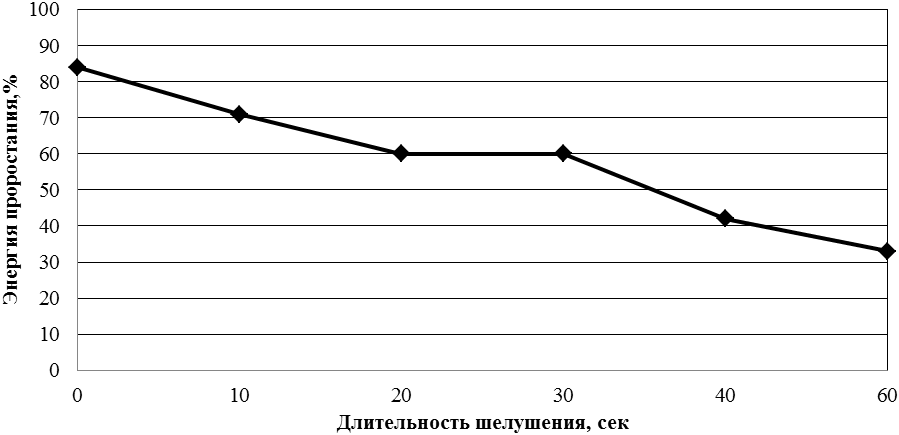
Рисунок 41 - Зависимость энергии прорастания от времени шелушения зерна пшеницы
Из рисунка видно, что с увеличение длительности шелушения до 60 сек показатель энергии прорастания снижается с 84 до 33%, что свидетельствует о степени удаления зародыша на 60%. При ранее установленной длительности шелушения 20-30 секунд, при которой соблюдается ограничение по приросту битых зерен, степень снижения энергии прорастания составляет 28%.
4.2.4 Исследование влияния длительности шелушения на выход и качество круподунстового продукта
Следующим этапом является определение выхода и зольности круподунстовых продуктов и муки, полученных в результате помола зерна твердой пшеницы белорусской селекции сорта Розалия. Размол зерна осуществляли на лабораторном вальцовом станке QC-104 на трех драных системах. Определяли выход и зольность круподунстовых продуктов. Результаты исследования представлены в таблицах 20, 21 и на рисунках 42 - 45.
Таблица 20 – Выход круподунстовых продуктов и муки, полученных в результате помола зерна твердой пшеницы белорусской селекции
Наименование продукта
| Длительность процесса шелушения, сек
| без предварительного шелушения
|
|
|
| Крупная крупка, %
| 9,5
| 13,5
| 14,9
| 15,9
| Средняя крупка, %
| 14,8
| 16,7
| 18,2
| 18,9
| Мелкая крупка, %
| 14,0
| 13,7
| 13,5
| 13,3
| Дунсты, %
| 28,3
| 27,6
| 25,8
| 25,1
| Мука, %
| 7,1
| 3,9
| 3,1
| 2,5
| Общий выход, %
| 73,7
| 75,4
| 75,5
| 75,7
| 66,6
| 71,5
| 72,4
| 73,2
|
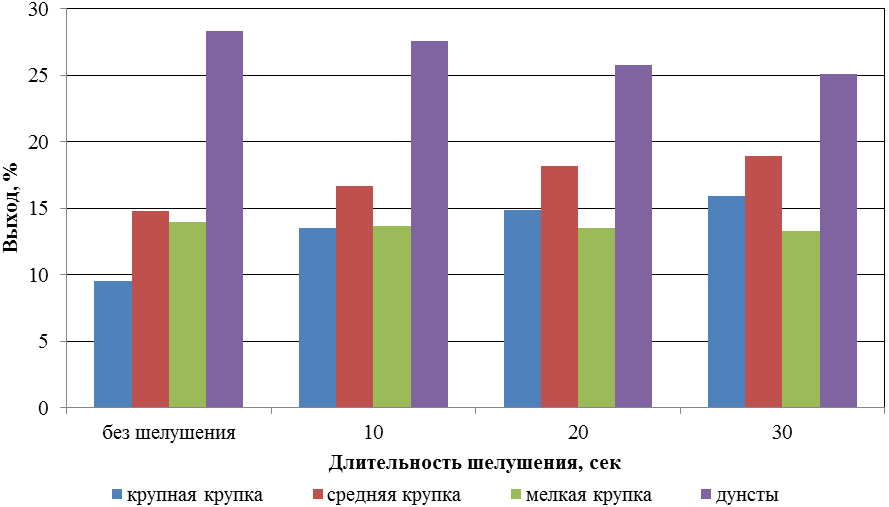
Рисунок 42 – Выход круподунстовых продуктов в зависимости от длительности процесса сухой обработки поверхности зерна
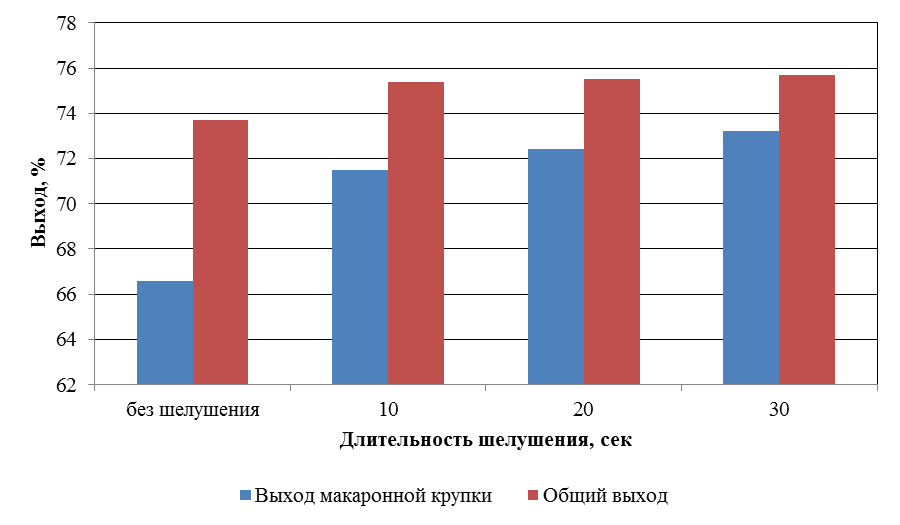
Рисунок 43 – Выход макаронной крупки и общий выход в зависимости от длительности процесса сухой обработки поверхности зерна
Таблица 21 – Зольность круподунстовых продуктов и муки, полученных в результате помола зерна твердой пшеницы б.с.
Наименование продукта
| Длительность процесса шелушения, сек
| без предварительного шелушения
|
|
|
| Крупная крупка, %
| 1,65
| 1,60
| 1,56
| 1,53
| Средняя крупка, %
| 1,35
| 1,29
| 1,24
| 1,21
| Мелкая крупка, %
| 1,21
| 1,15
| 1,03
| 1,08
| Дунсты, %
| 1,10
| 0,95
| 0,89
| 0,87
| Мука, %
| 0,83
| 0,80
| 0,78
| 0,75
| Средневзвешенная зольность, %
| 1,21
| 1,17
| 1,13
| 1,11
| 1,25
| 1,19
| 1,15
| 1,13
|
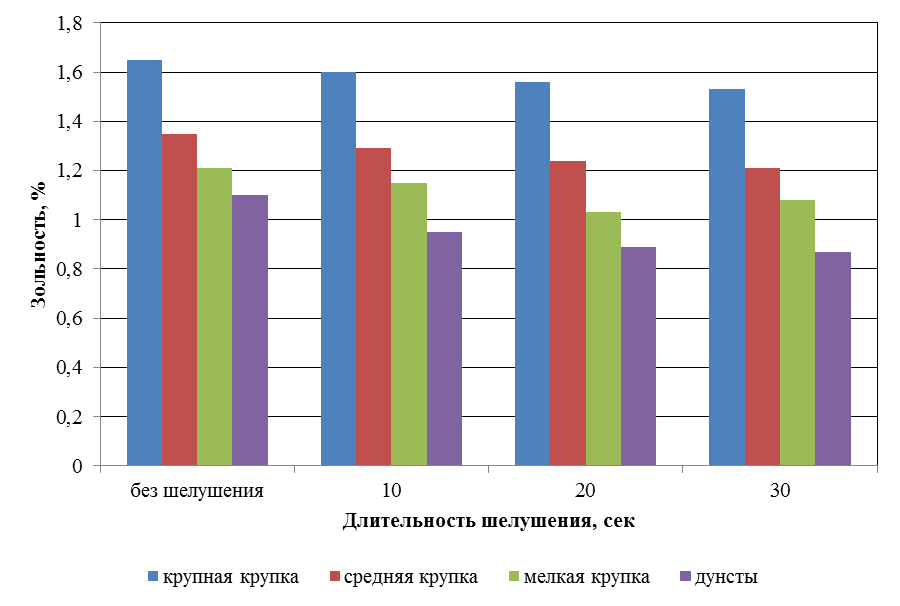
Рисунок 44 – Зольность круподунстовых продуктов в зависимости от длительности процесса сухой обработки поверхности зерна
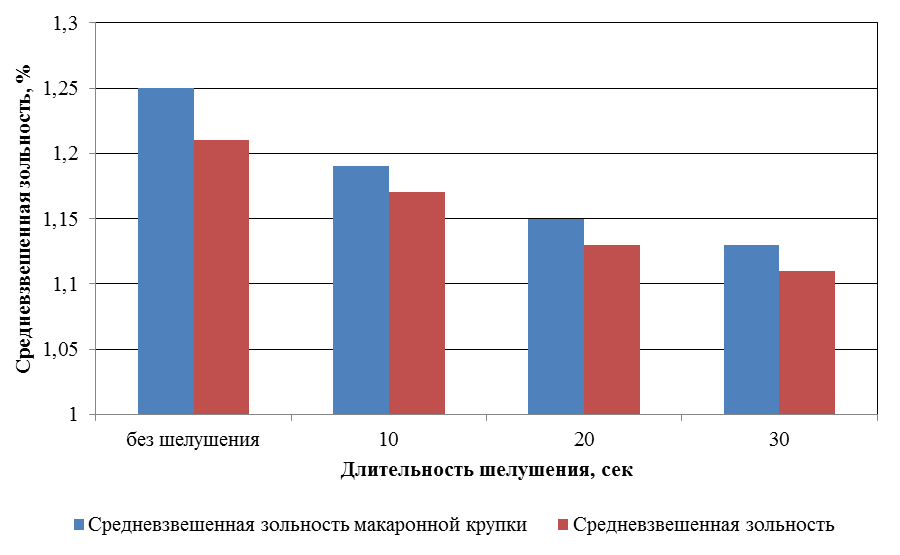
Рисунок 45 – Средневзвешенная зольность макаронной крупки и средневзвешенная зольность в зависимости от длительности процесса сухой обработки поверхности зерна
В результате исследований было установлено, что с увеличением длительности шелушения зерна выход круподунстовых продуктов увеличивается, а зольность снижается. Так, применение сухой обработки поверхности зерна в течение 30 секунд приводит к увеличению общего выхода круподунстовых продуктов на 6,6% и одновременному снижению зольности круподунстового продукта на 0,1%.
Для выявления более эффективного способа ведения подготовки зерна твердой пшеницы к макаронному помолу сравним технологические коэффициенты помолов зерна и шелушенного зерна (рисунок 46).
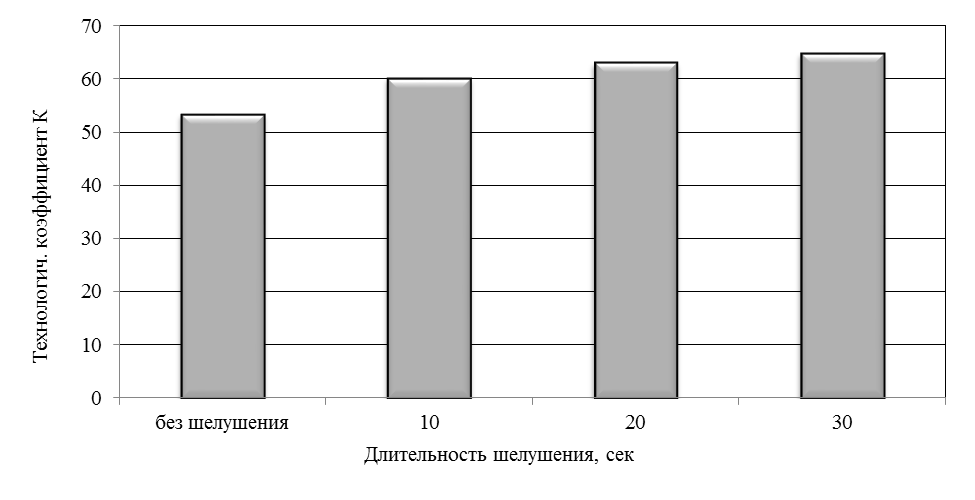
Рисунок 46 – Технологический коэффициент помола зерна в зависимости от длительности шелушения
Из рисунка видно, что с увеличением длительности сухой обработки поверхности зерна в шелушильно-шлифовальных машинах величина технологического коэффициента помола увеличивается. Зерно, шелушенное в течение 20-30 секунд, имеет наибольший технологический коэффициент помола.
4.2.5 Исследование влияния длительности шелушения на микроструктуру эндосперма, скорость поглощения влаги зерном и длительность процесса активного разрыхления эндосперма
Воздействие на зерновку рабочих органов шелушителя очевидно вызовет нарушение целостности эндосперма. Для подтверждения данного предположения была изучена микроструктура эндосперма зерна твердой пшеницы белорусской селекции при различной длительности обработки.
На рисунке 47 представлены микрофотографии эндосперма зерна твердой пшеницы белорусской селекции, шелушенного в течение от 5 до 60 секунд.
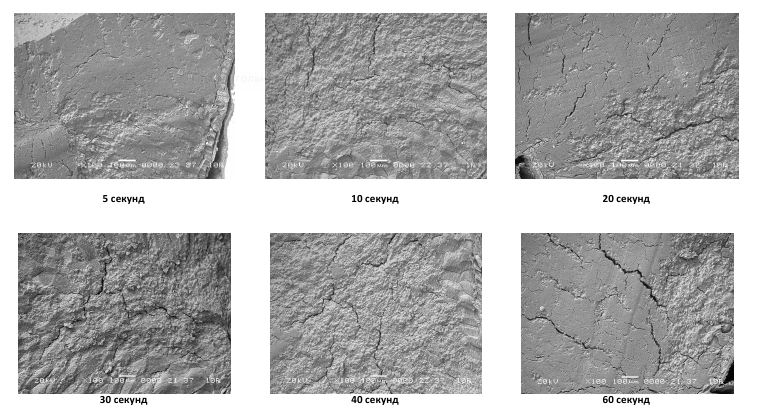
Рисунок 47 – Микрофотографии эндосперма зерна твердой пшеницы белорусской селекции, шелушенного в течение от 5 до 60 сек
Из рисунков видно, что с увеличением длительности шелушения количество микротрещин возрастает, они становятся глубже и длиннее. Кроме того, в процессе шелушения снимаются оболочки зерна. Исходя из этого, можно предположить, что при гидротермической обработке такого зерна поглощение влаги будет происходить интенсивнее, что сократит длительность отволаживания. При этом, чем длительнее сухая обработка зерна, т.е чем глубже и длиннее трещины, тем предположительно интенсивнее поглощение воды и менее длителен процесс отволаживания.
Поэтому на следующем этапе исследовали влияние длительности шелушения зерна твердой пшеницы на скорость поглощения влаги и степень разрыхления эндосперма.
Наблюдать за процессом разрыхления эндосперма можно косвенно, на основании изучения кривых приращения удельного объема зерна, суммарно отражающих степень разрыхления эндосперма.
Результаты проведенных исследований представлены на рисунке 48.
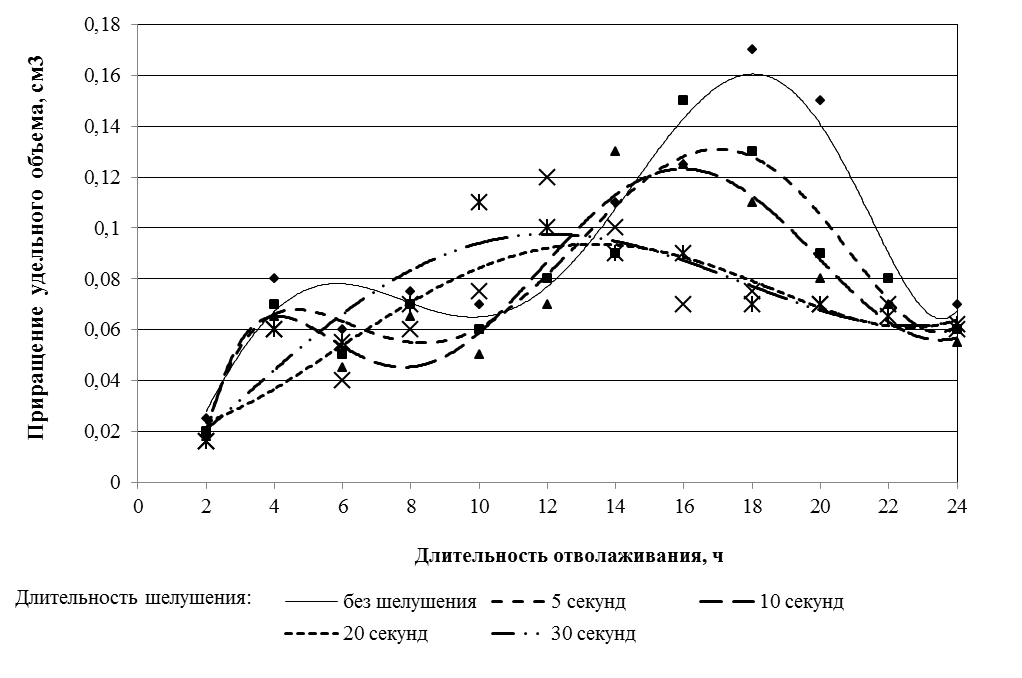
Рисунок 48 - Кривые разрыхления эндосперма зерна твердой пшеницы белоруской селекции в зависимости от длительности шелушения перед отволаживанием
Из рисунка видно, что максимальная степень разрыхления эндосперма, соответствующая максимуму на кривых приращения удельного объема зерна, наступает для нешелушенного зерна через 18-20 часов.
Применение сухой обработки поверхности зерна в течение 5 секунд сокращает период активного разрыхления на 2 часа, в течение 10 секунд – на 4 часа, увеличение длительности обработки до 20-30 секунд приводит к уменьшению необходимой длительности отволаживания до полного разрыхления эндосперма на 6-8 часов.
Таким образом, на основании полученных данных авторами рекомендуется при подготовке к макаронному помолу зерна твердой пшеницы проводить сухую обработку поверхности зерна на шелушильно-шлифовальных машинах перед ГТО при следующих режимах:
- длительность шелушения 20 секунд;
- степень снижения зольности – 0,15%;
- количество битых зерен – не более 1,5%.
4.2.6 Установление оптимальных режимов ГТО для шелушенного зерна
4.2.6.1 Оптимизация процесса гидротермической обработки при одноэтапном увлажнении
В качестве объекта проводимых исследований взят процесс гидротермической обработки, проводимый в один этап, зерна твердой пшеницы, белорусской селекции.
Целью исследований является установление оптимальных режимов гидротермической обработки зерна твердой пшеницы при переработке ее в макаронную крупку.
В качестве параметра оптимизации был выбран технологический коэффициент К, представляющий собой отношение выхода макаронной крупки к ее зольности, так как он в полной мере отражает количественные (выход) и качественные (зольность) характеристики процесса.
На процесс гидротермической обработки оказывают влияние ряд факторов: влажность зерна, продолжительность отволаживания, температура воды, физические свойства зерна и т.д.
При планировании эксперимента в качестве факторов были выбраны влажность (W) и длительность первого периода отволаживания (t). Длительность второго периода составляет 15-20 минут до I др.с с доувлажнением на 0,5%. Данные характеристики полностью удовлетворяют требованиям, предъявляемым к факторам – являются управляемыми, операциональными и однозначны. Так как одновременно изменяются оба фактора, была проверена совместимость факторов. Установлено, что выбранные факторы совместимы и между ними отсутствует корреляционная зависимость.
Из априорной информации были выбраны исходные точки для построения плана эксперимента и интервалы варьирования для первого и второго фактора (таблица 22).
Таблица 22 – Исходные данные для построения плана эксперимента
Условия планирования
| Обозначение
| W, %
| t, ч
| Основной уровень
|
| 15,5
|
| Интервал варьирования
|
| 1,5
|
| Верхний уровень
| +1
| 17,0
|
| Нижний уровень
| -1
| 14,0
|
|
На основании исходных данных были проведены опыты. Полученные результаты представлены в таблице 23.
Таблица 23 – План эксперимента по определению влияния факторов (влажности и длительности отволаживания) на технологический коэффициент
№ опыта
| Факторы
| Параметр оптимизации
| W (влажность, %)
| t (длительность отволаживания, ч)
| К (технологический коэффициент)
|
| -1
| -1
| 59,7
|
|
| -1
| 59,1
|
| +1
| -1
| 55,9
|
| -1
|
| 59,04
|
|
|
| 60,77
|
| +1
|
| 62,5
|
| -1
| +1
| 50,2
|
|
| +1
| 61,7
|
| +1
| +1
| 55,3
|
Полученные экспериментальные значения технологического коэффициента для каждого варианта (таблица 23) подвергались математической обработке.
При статистической обработке экспериментальных данных получено уравнение регрессии, адекватно описывающее в стандартизированных переменных зависимость исследуемого показателя качества от выбранных факторов
K = -285,589+45,7488·W+1,84688·t-1,51852· W2 + 0,185417·W·t -0,0591667· t2
Влияние каждого из оцениваемых факторов на параметры оптимизации графически отражали в виде карты Парето (рисунок 49 и графика главных эффектов отклика (рисунок 50).

Рисунок 49 – Стандартизированная карта Парето для технологического коэффициента К
Карта Парето позволяет установить незначимые коэффициенты и упростить первоначальный вид уравнения модели. Пересечение стандартизированных эффектов вертикальной линией, которая представляет 95% доверительную вероятность, означает, что влияние факторов на функцию отклика статистически значимо. Было установлено, что коэффициент А при переменной W незначим. Следовательно, его можно исключить из уравнения модели.
Значимость факторов (р<0,05) также подтверждается дисперсионным анализом, представленным в таблице 24.
Таблица 24 – Результаты дисперсионного анализа
Коэффициенты
| Сумма квадратов
| F-статистика
| р-значения
| A:W
| 3,77627
| 4,66
| 0,0308
| B:t
| 9,375
| 11,57
| 0,0007
| AA
| 23,3472
| 28,82
| 0,0000
| AB
| 19,8025
| 24,45
| 0,0000
| BB
| 28,6777
| 35,40
| 0,0000
|
После упрощения первоначального вида уравнения модели с учетом исключения незначимых коэффициентов было получено уравнение регрессии
K = -285,589 - 1,84688·t- 1,51852·W2 + 0,185417·W·t - 0,0591667· t2
Анализируя график главных эффектов отклика для технологического коэффициента К, установили, что влияния факторов по степени значимости распределилось в следующем порядке: с увеличением влажности до 15,6% технологический коэффициент увеличивается, а затем начинает снижаться, с увеличением длительности отволаживания до 8,8 часов также наблюдается увеличение технологического коэффициента, после этого значения происходит снижение значений технологического коэффициента (рисунок 50).

Рисунок 50 – Главные эффекты отклика для технологического коэффициента К
Графически модель влияния факторов на параметр оптимизации представлена в виде поверхности отклика (рисунок 51). Анализ графических зависимостей показал, что оптимальной влажностью и длительностью отволаживания, при которых технологический коэффициент имеет максимальное значение, являются W=15,6% и t=8,8ч. Дальнейшее увеличение влажности и длительности отволаживания приводит к снижению технологического коэффициента.


Рисунок 51 - График и контурный график поверхности отклика
Таким образом, в результате планирования эксперимента процесса гидротермической обработки зерна твердой пшеницы белорусской селекции были определены оптимальные режимы процесса холодного одноэтапного кондиционирования. Установили, что оптимальная влажность зерна – 15,6%, оптимальная длительность отволаживания – 8,8 ч.
4.2.6.2 Оптимизация процесса гидротермической обработки при двухэтапном увлажнении
В качестве объекта проводимых исследований взят процесс гидротермической обработки, проводимый в два этапа, зерна твердой пшеницы белорусской селекции.
Целью исследований является установление оптимальных режимов отволаживания при ГТО, т.е. длительность первого и второго этапов отволаживания, третий этап увлажнения за 15-20 минут перед первой драной системой на 0,5 % остается неизменным.
В качестве параметра оптимизации был выбран технологический коэффициент К, представляющий собой отношение выхода макаронной крупки к ее зольности, так как он в полной мере отражает количественные (выход) и качественные (зольность) характеристики процесса.
При планировании эксперимента в качестве факторов были выбраны длительность первого этапа отволаживания (t1) и длительность второго этапа отволаживания (t2).
Из априорной информации были выбраны исходные точки для построения плана эксперимента и интервалы варьирования для первого и второго фактора (таблица 25).
Таблица 25 – Исходные данные для построения плана эксперимента
Условия планирования
| Обозначение
| t1, ч
| t2, ч
| Основной уровень
|
|
| 2,5
| Интервал варьирования
|
|
| 2,5
| Верхний уровень
| +1
|
|
| Нижний уровень
| -1
|
|
|
Затем были проведены опыты. Полученные результаты представлены в таблице 26.
Таблица 26 – План эксперимента по определению влияния факторов (влажности и длительности отволаживания) на технологический коэффициент
№ опыта
| Факторы
| Параметр оптимизации
| Длительность 1-ого этапа отволаживания (t1)
| Длительность 2-ого этапа отволаживания (t2)
| К (технологический коэффициент)
|
| -1
| -1
| 56,94
|
|
| -1
| 59,02
|
| +1
| -1
| 53,39
|
| -1
|
| 57,74
|
|
|
| 58,52
|
| +1
|
| 53,12
|
| -1
| +1
| 53,61
|
|
| +1
| 56,31
|
| +1
| +1
| 52,12
|
Полученные экспериментальные значения технологического коэффициента для каждого варианта подвергались математической обработке.
При статистической обработке экспериментальных данных получено уравнение регрессии, адекватно описывающее в стандартизированных переменных зависимость исследуемого показателя качества от выбранных факторов
K=54,9458+1,51447∙ t1+0,206933∙t2-0,138533∙ t12 +0,0412∙ t1∙t2 -0,196533∙ t22 (15)
Влияние каждого из оцениваемых факторов на параметры оптимизации графически отражали в виде карты Парето (рисунок 52) и графика главных эффектов отклика (рисунок 53.

Рисунок 52 – Стандартизированная карта Парето для технологического коэффициента К
Карта Парето позволяет установить незначимые коэффициенты и упростить первоначальный вид уравнения модели. Пересечение стандартизированных эффектов вертикальной линией, которая представляет 95%-ную доверительную вероятность, означает, что влияние факторов на функцию отклика статистически значимо. Было установлено, что коэффициент А при переменной t1 незначим. Следовательно, его можно исключить из уравнения модели.
Значимость факторов (р<0,05) также подтверждается дисперсионным анализом, представленным в таблице 27.
Таблица 27 – Результаты дисперсионного анализа
Коэффициенты
| Сумма квадратов
| F-статистика
| р-значения
| A: t1
| 15,5526
| 27,65
| 0,0000
| B: t2
| 8,90602
| 15,83
| 0,0001
| AA
| 23,9894
| 42,65
| 0,0000
| AB
| 1,0609
| 1,89
| 0,1696
| BB
| 3,01761
| 5,36
| 0,0205
|
После упрощения первоначального вида уравнения модели с учетом исключения незначимых коэффициентов было получено уравнение регрессии
K=54,9458+1,51447∙t1+0,206933∙t2-0,138533∙t12-0,196533∙t22 (16)
Анализируя график главных эффектов отклика для технологического коэффициента К, установили, что влияния факторов по степени значимости распределилось в следующем порядке: с увеличением длительности отволаживания первого этапа до 6 часов технологический коэффициент увеличивается, а затем начинает снижаться, с увеличением длительности второго этапа отволаживания до 2 часов также наблюдается увеличение технологического коэффициента, после этого значения происходит снижение значений технологического коэффициента (рисунок 53).

Рисунок 53 – Главные эффекты отклика для технологического коэффициента К
Графически модель влияния факторов на параметр оптимизации представлена в виде поверхности отклика (рисунок 54). Анализ графических зависимостей показал, что оптимальной длительностью отволаживания первого этапа и длительностью второго этапа отволаживания, при которых технологический коэффициент имеет максимальное значение, являются t1=5,6 ч и t1=1,1 ч. Дальнейшее увеличение влажности и длительности отволаживания приводит к снижению технологического коэффициента.


Рисунок 54 – График и контурный график поверхности отклика
На основании полученных данных были определены оптимальные режимы процесса холодного двухэтапного кондиционирования. Установили, что оптимальная – длительность первого этапа отволаживания t1 = 5,6 ч, длительность второго этапа отволаживания составляет t2 = 1,1 ч при влажности 15,5-16%.
Анализ литературных источников показал, что авторами Косцовой И.С. и Гончаренко Т.М. ранее были установлены режимы гидротермической обработки зерна твердой пшеницы белорусской селекции при подготовке ее к макаронному помолу: при однократном увлажнении - влажность 15,5-16%, длительность отволаживания 12,0-12,5 часов; при двукратном увлажнении – длительность первого периода отволаживания – 8 часов, второго – 1,5 часа, влажность – 15,5-16%. Таким образом, сравнение полученных оптимальных режимов ГТО шелушенного зерна твердой пшеницы белорусской селекции с ранее полученными оптимальными режимами для зерна, не прошедшего первичную обработку поверхности зерна, показало, что при увлажнении и отволаживании шелушенного зерна сокращается длительность отволаживания на 3,5-4 часа при одноэтапном увлажнении и на 3 часа при двухэтапном увлажнении. Сокращение длительности отволаживания приведет к уменьшению длительности технологического процесса и количества технологического оборудования.
4.2.6.3 Сравнительный анализ режимов подготовки к помолу зерна твердой пшеницы белорусской селекции
Для сравнения полученных режимов подготовки к помолу зерна твердой пшеницы белорусской селекции с ранее установленным были проведены пробные лабораторные помолы. Режимы процесса подготовки к помолу, полученные в результате исследований (вариант 1):
- удаление мелкой фракции зерна 2,2х20/1,7х20;
- предварительная сухая обработка поверхности зерна в шелушильно шлифовальной машине (степень снижения зольности – 0,15%; количество битых зерен – не более 2%);
- ГТО в два этапа (влажность зерна 15,5-16%, длительность первого и второго этапа отволаживания 5,5часа и 1час соответственно).
Сравнительные режимы процесса подготовки к помолу по традиционной схеме согласно Правил ведения технологических поцессов на мукомольных заводах (вариант 2):
- ГТО в два этапа (влажность зерна 15,5-16%, длительность первого и второго этапа отволаживания 8,5-9 часов и 1,5 часа соответственно).
После подготовки к помолу по двум вариантом зерна твердой пшеницы исследуемых сортов были проведены пробные лабораторные помолы, определен выход и зольность полученных продуктов и рассчитан технологический коэффициент К.
Результаты исследования представлены в таблицах 28, 29 и на рисунке 55.
Таблица 28 - Выход круподунстового продукта и муки при помоле зерна твердой пшеницы белорусской селекции
Сорт
| Славица
| Вероника
| Розалия
| Фракция крупок
| вариант 1
| вариант 2
| вариант 1
| вариант 2
| вариант 1
| вариант 2
| Крупная
| 15,1
| 8,9
| 14,5
| 9,2
| 14,9
| 8,7
| Средняя
| 17,9
| 15,1
| 17,7
| 14,5
| 18,2
| 14,7
| Мелкая
| 13,8
| 13,3
| 14,1
| 13,8
| 13,5
| 12,9
| Дунсты
| 26,5
| 28,0
| 26,3
| 28,0
| 25,8
| 28,2
| Мука 2 сорта
| 3,8
| 11,1
| 4,0
| 10,8
| 3,1
| 11,2
| Макарон-ная крупка
| 73,3
| 65,3
| 72,6
| 65,5
| 72,4
| 64,5
| Общий выход
| 77,1
| 76,4
| 76,6
| 76,3
| 75,5
| 75,7
|
Таблица 29 - Зольность круподунстового продукта, полученного при помоле зерна твердой пшеницы белорусской селекции
Сорт
| Славица
| Вероника
| Розалия
| Фракция крупок
| 1 вариант
| 2 вариант
| 1 вариант
| 2 вариант
| 1 вариант
| 2 вариант
| Крупная
| 1,5
| 1,87
| 1,5
| 1,80
| 1,53
| 1,83
| Средняя
| 1,3
| 1,49
| 1,25
| 1,47
| 1,21
| 1,38
| Мелкая
| 1,11
| 1,38
| 1,1
| 1,31
| 1,08
| 1,25
| Дунсты
| 0,85
| 1,12
| 0,85
| 1,16
| 0,87
| 1,15
| Мука 2 сорта
| 0,75
| 0,87
| 0,77
| 0,89
| 0,75
| 0,85
| Макаронная крупка
| 1,14
| 1,36
| 1,13
| 1,35
| 1,13
| 1,31
| Средневзве-шенная зольность
| 1,12
| 1,29
| 1,11
| 1,28
| 1,11
| 1,25
|
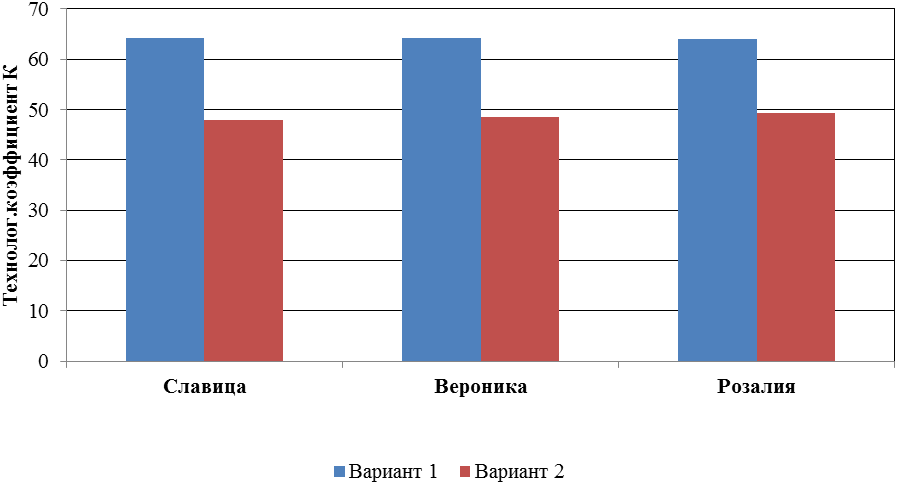
Рисунок 55 - Изменение технологического коэффициента К в зависимости от способа подготовки зерна к помолу
Из рисунка видно, что для всех исследуемых сортов технологический коэффициент К помола зерна, прошедшего подготовку с применением режимов, полученных в результате исследований, выше, чем для помола, подготовка к которому проведена согласно традиционной схеме. Результаты проведенных исследований позволяют сделать вывод о целесообразности проведения подготовки к макаронному помолу зерна твердой пшеницы с предварительным отбором мелкой фракции зерна и с применением сухой обработки поверхности зерна с использованием шелушильно-шлифовальных машин.
Дата добавления: 2016-06-05 | Просмотры: 850 | Нарушение авторских прав
1 | 2 | 3 |
|