АкушерствоАнатомияАнестезиологияВакцинопрофилактикаВалеологияВетеринарияГигиенаЗаболеванияИммунологияКардиологияНеврологияНефрологияОнкологияОториноларингологияОфтальмологияПаразитологияПедиатрияПервая помощьПсихиатрияПульмонологияРеанимацияРевматологияСтоматологияТерапияТоксикологияТравматологияУрологияФармакологияФармацевтикаФизиотерапияФтизиатрияХирургияЭндокринологияЭпидемиология
|
Система автоматического управления процессом термосиловой обработки
В теоретических разработках показано, что для минимизации технологической наследственности передаваемой от операции необходимо снизить уровень остаточных напряжений и создать равнонапряженное состояние по всей длине заготовки, что, естественно, приведет к равномерной релаксации напряжений и минимальному короблению готовых изделий при их эксплуатации.
Для этой цели была введена в технологический процесс операция термосиловой обработки ТСО. Трудность управления этим процессом состоит в том, что свои физико-механические свойства материала, из которого изготавливают детали, настолько разнообразны и поведение их зависит от внешних условий при их эксплуатации, что найти единый закон управления просто невозможно. В первом приближении ставится задача получить тело равного сопротивления, т.е. тело во всех точках которого возникают одинаковые микроскопические напряжения. Анализ статических характеристик, напряжение-деформация показал, что согласно этих характеристик все материалы при упруго пластических деформациях имеют три участка - упругий, текучести, упрочнения. Если пластическая деформация небольшая, в пределах 0,2…2,0 %, то кривые деформации можно в первом приближении аппроксимировать ломаной прямой. В данной работе впервые ставится задача активного контроля состояния материала в процессе нагрева и деформации и автоматическом управлении остаточными напряжениями на протяжении всего времени обработки, независимо от физмехсвойства материала и геометрических параметров заготовок.
Система автоматического обеспечения технологических параметров осесимметричных маложестких деталей при термосиловой обработке осуществляется следующим образом, в работе участвуют два взаимосвязанных контура управления, первый - температурным режимом, второй - силовым нагруженном. Первый контур управления обеспечивает управление горизонтальной многосекционной электропечью 1, смонтированной в стапеле 2 (последний показан условно). Заготовку 3 устанавливают в печь 1 и закрепляют жестко на стапеле 2. Длина секции определяется геометрическими и физико-механическими параметрами и свойствами материала заготовки и не должна превышать величины (отношение длины заготовки к ее диаметру). В начальный момент работы автоматической системы управления включается первый контур управления температурным режимом, при этом температура рабочей среды в печи 1 контролируется термопарой контроля средней температуры 4 выходной сигнал которой является входом усилителя постоянного тока 5, где этот сигнал усиливается и поступает на первый вход первого нуль-органа 6, где на второй его вход поступает сигнал с задатчика средней температуры и время ее выдержки 7. Численное значение средней температуры и время выдержки после после пластического деформирования определяется физико-механическими свойствами материала заготовки. Температурный режим нагрева-охлаждения назначается согласно технологии обработки, отпуск, нормализация и т.д. входной сигнал с первого нуль - органа 6 (сигнал рассогласования-усилителя 5 и задатчика 7) поступает на вход блока вида работ 8, который включает в работу все секции нагрева одновременно или выборочно согласно закону управления (все секции выполнены идентично и на рис. 4.7. и представлены едиными обозначениями 9 … 12 и т.д.). Принцип работы контура управления температурой нагрева печи рассматривается на примере канала управления одной секции. Сигнал с блока 8 поступает на первый вход второго нуль-органа 9, который подключен к выходу дифференциального усилителя 10, выходной сигнал последнего через блок формирования управляющего сигнала 11 управляет нагревательным элементом 12, увеличивает или уменьшает ток питания нагревательных элементов 12. Отклонение от средней температуры по длине заготовки начиная от ее середины сопутствует любой термомеханический процесс. Нагрев или растяжение - всегда температура в середине заготовки больше, чем по краям, и убывает монотонно от середины. Для выравнивания температуры по длине заготовки на каждой секции встроена термопара контроля локальной зоны нагрева 13, выход которой включен на второй вход дифференциального усилителя 10, что создает обратную связь в канале управления нагревом нагревательного элемента 12 и обеспечивает высокую точность поддержания температуры нагрева, выдержки и охлаждения. При выходе на заданную среднюю температуру нагрева печи 1, блок вида работ 8 подключает к работе нагревательных каналов бесконтактный пневмоизмеритель линейных перемещений 14, создавая при этом вторую обратную связь в каналах управления нагрева по утонению диаметров заготовки 3. Количество пневмоизмерителей 14 определяется количеством нагревательных элементов 12. Пневмоизмеритель 14 вмонтирован в опору-призму 15, в глубине угловой впадины, служит одновременно как измерительная база и как направляющая для загрузки заготовки, длина ее определяется суммарной длиной нагревательных элементов 12. Опора-призма помещается внутри печи 1 и имеет в своем корпусе общую магистраль 16 питания пневмоизмерителей 14 теплым воздухом, который нагнетается и с определенным наперед заданным давлением воздушным насосом 17. В зависимости от изменения зазора между торцом бесконтактного пневмоизмерителя 14 и нагруженной поверхностью заготовки 3, изменяется и расход в канале пневмоизмерителя 14. С изменением зазора линейно меняется и расход воздуха. Изменение расхода воздуха контролируется электропреобразовательным блоком усиления 18, который включен в обратную связь канала управления нагревательного элемента 12 на второй вход второго нуль-органа 9, что позволяет контролировать приращение диаметра заготовки в контролируемом участке с учетом знака. Опрос об изменении-утонении диаметров заготовки и канавки, их численные значения при силовом осевом нагружении производит коммутатор 19, который последовательно опрашивает каждый из пневмоизмерителей 14, и передает полученную информацию в блок экстремального поиска 20, последний находит минимальные величины утонения диаметра заготовки и в виде выходного сигнала подает эти значения на вход блока памяти 21, который формирует сигналы управления на все каналы управления нагревательными элементами, отключает нагрев в случае утонения контролируемого участка и поддерживает температуру нагрева в тех участках, где не произошло пластической деформации всего объема материала на одну и ту же величину, т.е. когда утонения на всех контролируемых участках не будет одинаковым, после этого блок памяти выдает сигнал на отключение контура силового осевого деформирования. Отключение нагревательного элемента 12 понижает температуру нагрева контролируемого участка заготовки.
Нагревая и охлаждая участки заготовки при постоянном осевом нагружении, с заданной скоростью металл получает равномерную пластическую деформацию по всему сечению и по всей длине заготовки, и, следовательно, заготовка получается с равномерными осевыми остаточными напряжениями. Второй контур автоматического управления осевым деформированием работает следующим образом: после нагрева печи до средней заданной температуры и заданной выдержки, которая определяется техпроцессом, блок вида работ 8 включает в работу канал управления осевым нагруженном, один из выходов блока 8 подключен к одному из входов многовходового дифференциального усилителя 22, выход последнего является входом силового привода осевого нагружения 23, выход которого жестко связан с механизмом захвата заготовки 24. При пуске силового привода осевого нагружения 23, пневмоизмеритель 14 вырабатывает рабочий сигнал о наступлении пластической деформации (на выборку зазоров в механизме захвата и крепления заготовки в стапеле пневмоизмеритель не реагирует). Полезный сигнал с пневмообразователя 14, пройдя через электропреобразовательный блок усиления 18, поступает на блок формирования относительной скорости пластической деформации от задатчика скорости пластической деформации 26 с учетом геометрических параметров заготовки задатчика скорости пластической деформации формирует численное значение скорости пластической деформации - скорости относительного утонения диаметра заготовки в единицу времени. Выходной сигнал с блока 25 сигнал управления скоростью осевого деформирования заготовки поступает на вход многовходового дифференциального усилителя 22, последний формирует сигнал управления для силового привода осевого нагружения 23. Величину осевого пластического деформирования заготовки относительно стапеля контролирует измеритель линейных осевых перемещений 27, который жестко крепится на стапеле 2. Величина осевого пластического деформирования преобразованная в электрический сигнал измерителем 27 сравнивается в сумматоре 28 с величиной пластического деформирования заданной задатчиком осевого пластического деформирования 29, выходной сигнал разности с сумматора 28 поступает на один из входов многоходового дифференциального усилителя 22. В случае достижения заданной величины пластического деформирования, дифференциальный усилитель отключает силовой привод 23. Конечная величина осевого пластического деформирования заготовки определяется по априорной информации и зависит от физико-механических свойств металла заготовки 3.
Осевое пластическое деформирование осуществляется в функции поперечной скорости и пластической деформации заготовки. При достижении, если равенство поперечной деформации не наступило, заданной величины осевого пластического деформирования, то для данной заготовки назначается термообработка-отпуск, но с другими температурными, силовыми и скоростными параметрами деформации. В этом случае установку перестраивают на другой режим работы.
При отключении контура осевого деформирования, силовой привод 23 приходит в режим торможения - замыкая механизм захвата 24 на стапель 2. В этом режиме блок вида работ 8 обеспечивает равенство температуры нагрева заготовки по ее всей длине, в течение заданного времени выдержки, что обеспечивает осевую дислокацию в материале и ориентацию зерен в направлении силового поля. После окончания выдержки задатчик 7 выдает сигнал на включение блока режима охлаждения 30, последний, согласно заданной программе, формирует сигнал управления скоростью охлаждения для источника питания 31. Параллельно снижению температуры работает контур управления стабилизации температуры по длине заготовки, что позволяет сформировать температурные остаточные напряжения равномерные и направленные по всему объему заготовки. При достижении наперед заданной минимальной температуры (например 20°) система автоматического управления отключается, заготовка освобождается от силового замыкания.
В процессе термосиловой обработки с использованием автоматической системы управления по предлагаемому способу заготовка получает заданные физико-механические свойства и равнонапряженное состояние материала по сечению и длине заготовки. Одновременно процесс пластической деформации при термомеханической обработке позволяет устранить коробление, полученное заготовкой на предыдущих операциях, т.е. исключить технологическую наследственность, в то же время управляемый процесс охлаждения, когда температура стабильна по всей длине, температурные остаточные напряжения равномерны по всему объему.
Показано, что при деформации металлов в условиях развития фазового превращения происходит резкое повышение пластичности. Этот эффект наблюдается, как при диффузионных, так и при мартенситных превращениях. Эти факты указывают на то, что момент фазового превращения независимо от его механизма благоприятствует развитию процессов пластического течения. Эффект сверхпластичности при фазовом превращении зависит от прочности фаз, участвующих в фазовом переходе. Сверхпластичность вызывается внутренними напряжениями, возникающими вследствие разности удельных объемов превращающихся и вновь образующихся фаз. Отмечается, что между сверхпластическим течением и напряжениями существует линейная связь. Опираясь на работы и литературные источники, была предложена идея использовать эффект сверхпластичности для устранения технологической наследственности и снижения уровня остаточных напряжений, полученных при холодной правке заготовки. Особенностью такого подхода является то, что при ТСО прикладывается статическое напряжение, величина которого уменьшается в функции температурного удлинения, при этом начиная с некоторой наперед заданной температуры отношение приложенных напряжений, к напряжению, соответствующему пределу текучести, оставалось постоянным до момента наступления фазовых превращений. Кроме того, заготовку дополнительно возбуждают изгибные колебания на собственной частоте, регистрируя девиацию частоты и уменьшение амплитуды, контролируя отбор активной составляющей энергии самовозбуждающего генератора возбуждения изгибных колебаний в функции энергетически минимального значения, формируют сигналы управления соответствующие началу фазовых превращений и допустимому значению под действием температурно-силовых факторов. Автоматически жестко фиксируют подвижный конец заготовки в осевом направлении от температурного удлинения и одновременного статического нагружения. Одновременно фиксируют новое значение частоты и амплитуды изгибных колебаний и формируют критерий оценки - получении заданных физико-механических свойств обработанного материала, по отношению собственных частот заготовки в режиме нагрева и частоте собственных колебаний в режиме отпуска причем, чем меньше отношение частот, тем выше физико-механические свойства заготовки. Активный контроль состояния материала в процессе нагрева и деформаций позволяет управлять объемным остаточным напряжением на протяжении всего времени обработки, независимо от марки стали и геометрических параметров заготовки.
Сущность метода поясняется схемой рис.3.14, где показаны конструктивные особенности установки для термосиловой обработки ТСО маложестких деталей типа "вал", на рис.3.15 представлена функциональная блок схема автоматической диагностики и управления процессом ТСО.
Управление процессом ТСО маложестких деталей осуществляется следующим образом: в электрическую печь 1 устанавливают заготовку 2 относительно стапеля 3. Причем верхний конец крепят к плите 4 механизма квазистатической нагрузки, причем плита 4 перемещается вверх под действием нагрузочных пружин 5 по направляющим скалкам 6. Осевая растягивающая сила определяется из условия , где - коэффициент жесткости пружин, Х - ход пружин. Пружины могут включаться в работу параллельно и последовательно.

Рис.3.14. Функциональные схемы САУ термосиловой обработкой упрочняющих материалов (а) и одного ее блока (б)
Жесткая фиксация заготовки 2 относительно плиты 4 осуществляется стопором 7, при остывании заготовка перемещается вниз (сжимается), а ее перемещение регулируется электромеханическим ограничителем хода заготовки 8, управляемого первым реле регулятором 9. На стапеле 3 крепится электромагнитный вибратор 10, обеспечивающий колебания заготовки на первой резонансной частоте в режиме отпуска. Удлинение заготовки 2 в процессе нагрева контролируется датчиком линейных перемещений 11, а его выход преобразований в электрический сигнал поступает в систему управления и диагностики.
В исходном состоянии, после закрепления заготовки 2 и в нижней части стапеля производят сжатие пружин 5 электромеханическим приводом 12 от второго реле регулятора 13, обеспечивая при этом свободный проход заготовки 2 через центральное отверстие плиты 4. Затем заготовку 2 фиксируют относительно плиты 4 стопором 7, т.е. замыкают верхний свободный конец заготовки 2 на торец плиты 4. Далее освобождают предварительно сжатые пружины 5 путем управления механизмом натяжения 12 от электропривода 13, обеспечивая при этом нагружение заготовки 2 осевой силой , где - коэффициент жесткости пружин под действием рабочей нагрузки, в данном случае максимальной, которая выбирается исходя из геометрических параметров и физико-механических свойств заготовки. В этом исходном положении заготовка 2 нагружена осевой растягивающей силой за счет пружин 5 (количество пружин выбирается исходя из потребной осевой силы) через плиту 4.

Рис.3.15. САУ процессом ТСО маложестких деталей типа «вал»
Далее включают электрическую печь 1 и контролируют приращение температуры нагрева печи с помощью первичного преобразователя регистрации температуры 14, подключенного ко входу потенциометрического усилителя 15. Выходной сигнал усилителя 15 пропорциональный температуре печи регистрируется с помощью многовходового регистратора 16, одновременно регистрируют величину температурного удлинения заготовки 2 с помощью датчика линейных перемещений 11 первичного преобразователя регистрации температурных удлинений и усилительного блока температурных удлинений 17, выход которого также подключен к многовходовому регистратору 16. Для автоматической регистрации приращения температуры и температурных удлинений заготовки - параметры, необходимые для предварительной настройки и оценки динамики изменения температуры печи и удлинения заготовки, в многовходовой регистратор встроен самописец.
Одновременно с нагревом заготовки 2 ее возбуждают изгибными колебаниями в режиме отпуска на ее собственный резонансной частоте с учетом приведенной массы механизма статического нагружения, с помощью электромагнитного вибратора 10, установленного на верхней части стапеля 3. Возбуждение заготовки осуществляют на участке вне зоны нагрева. Электромагнитный вибратор подключен к выходу самовозбуждающего генератора 18, включающего в себя, соединенные в кольцо задающий генератор 19, усилитель мощности 20, эмпидансный мост 21 и блок 22 стабилизации резонансной частоты, амплитуды и фазы. Причем для оценки отбора активной составляющей энергии от генератора электромагнитный вибратор 10 включен в одно из плеч эмпидансного моста 21. Под действием температурно-силовых факторов увеличивается линейное удлинение заготовки 2, приводящее к изменению (увеличению) величины хода пружин 5, сопровождающееся уменьшением осевых растягивающих усилий, действующих на заготовку, величину статического напряжения заготовки 2 выбирают таким образом, чтобы, начиная с некоторой наперед заданной температуры, отношение приложенных напряжений растяжения к пределу текучести оставалось постоянным до момента наступления фазовых превращений (появление сверхпластичности).
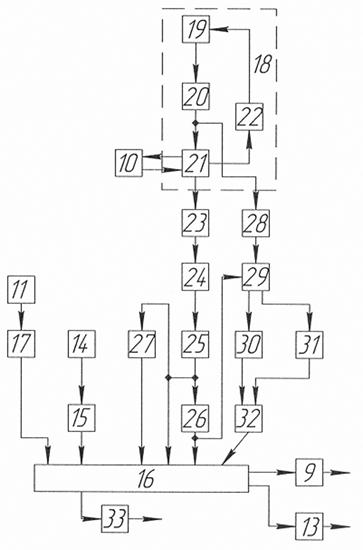
Рис.3.16. Диагностические каналы САУ термосиловым процессом
Такой режим стабилизации указанного отношения обеспечивается автоматически за счет уменьшения усилий осевой статической нагрузки под действием изменяющейся величины хода пружин и изменения напряжения от температуры. При обеспечении постоянства отношений , где - рабочее нормальное напряжение, создаваемое пружинами, - предел текучести при условии, что необратимая остаточная деформация равна 0,2 %, несмотря на увеличение длин заготовки, собственная частота подсистемы "вал-опоры" остается постоянной за счет стабилизации жесткости указанной подсистемы. В случае несохранения указанного соотношения, изменяется жесткость подсистемы "вал-опоры", а, следовательно, меняется (уменьшается) ее собственная резонансная частота, изменения частоты в таком случае несет информацию о нарушении указанного отношения , а, следовательно, о необеспечении заданных температурно-силовых факторах воздействия. Регистрация изменения частоты, амплитуды и активной составляющей мощности динамического воздействия осуществляется с помощью двух взаимно-связанных диагностических каналов.
Первый диагностический канал, состоящий из последовательно включенных: полосового усилителя 23, детектора 24, интегратора 25, компаратора 26 (пороговый элемент), первого аналогового блока памяти 27, подключенного к сигнальному входу компаратора 26 и многовходовому регистратору 16, и второго реле-регулятора 13 управления электромеханическим приводом 12 натяжения пружин 5.
Первый диагностический канал служит для формирования диагностического признака, несущего информацию о моменте наступления фазовых превращений и сверхпластичности. Принцип формирования полезного управляющего сигнала заключается в следующем. Напряжение снимаемого с выхода эмпидансного моста 21, пропорциональное амплитуде колебаний и отбору активной энергии от самовозбуждающего генератора 18, усиливается полосовым усилителем 23, детектируется блоком 24, интегрируется блоком 25 и подается непосредственно и через компаратор 26, а также через аналоговый блок памяти 27 на последующие входы многовходового регистратора 16. Поскольку жесткость подсистемы "вал-опоры" остается постоянной даже при изменении температурно-силовых факторов, то величина амплитуды также остается неизменной до момента наступления температуры, соответствующей сверхпластичности материала заготовки, значение которой фиксируется аналоговым блоком памяти 7, выходное напряжение блока 27 является входным сигналом компаратора 26, равным опорному сигналу на втором его входе от интегратора 25. При наступлении момента фазовых превращений и сверхпластичности добротность механической подсистемы "вал - опоры" резко падает, и уменьшается при этом амплитуда выходного сигнала на выходе блока 25, а, следовательно, амплитуда опорного сигнала на входе компаратора 26, приводящего к срабатыванию последнего. Выходной сигнал компаратора 26 воздействует на первое реле регулятора управления 9, выход которого через электромеханический привод, управляет механизмом жесткой фиксации заготовки в ее верхней части, а также отключает дальнейший нагрев электропечи 1 и с этого момента включают режим отпуска, необходимый для формирования заданной структуры физико-механических свойств и равномерного напряженно-деформационного состояния по всей длине заготовки. Такое условие обеспечивается за счет создания постоянного осевого усилия механизмом жесткой фиксации заготовки.
Начальное значение собственной резонансной частоты подсистемы "вал-опоры" соответствует режиму нагрева, а изменение частоты соответствует режиму отпуска, фиксируется вторым диагностическим каналом, образованным блоками 28 - 32. сформирование управляющего сигнала и реализация критерия оценки заданных свойств обрабатываемого материала по отношению собственных частот заготовки осуществляется вторым диагностическим каналом следующим образом. Выходное напряжение самовозбуждающего генератора 18 с частотой в режиме нагрева преобразуется блоком 28 (блок преобразователя частоты колебаний в аналоговый сигнал) в аналоговое напряжение, которое через электронный управляемый переключатель 23 подается на второй аналоговый блок памяти 30, аналоговое напряжение запоминается блоком 30 и додается на один из входов блока отношений 32, реализующего критерий к. В момент наступления фазовых превращений после срабатывания компаратора 26, управляющего электронным переключателем, последний под действием управляющего сигнала компаратора 26 подключает выход блока 29 преобразователя "частота-напряжение" к входу третьего аналогового блока памяти 32, который регистрирует это напряжение, соответствующее частоте в режиме отпуска. Причем, за частоту принимают частоту, соответствующую жесткости подсистемы "вал-опоры" в упруго-напряженном состоянии и температуры окончания отпуска. Выходное напряжение третьего аналогового блока памяти 31 подают на второй вход блока отношений 32, реализующего критерий , причем, чем меньше величина указанного отношения, тем выше полученные физико-механические свойства заготовки.
Наличие двух контуров формирования диагностических признаков и управления режимами термомеханической обработки, а также механической системы стабилизации отношения с автоматическим приводом механизма фиксации заготовки позволяет полностью автоматизировать техпроцесс и получить деталь заданного качества. ТСО позволяет, наряду с получением физико-механических свойств, получить равнонапряженное состояние по длине заготовки и одновременно проводить процесс правки в пределах припуска на обработку, а также исключить технологическую наследственность заготовки.
При термомеханической обработке новых конструкционных материалов с отсутствием явно выраженной зоны сверхтекучести режим автоматического управления температурой нагрева до максимальной величины отпуска осуществляется аналогично прототипу на основе анализа регистрации пропорциональности температурного удлинения заготовки датчиком линейных перемещений 11, а также каналом, образованным блоком 17. Усилительный блок температурных удлинений, воздействующий также через многовходовой регистратор 16 на третье реле-регулятор 33, и отключает дальнейший процесс термомеханической обработки.
Как отмечалось в предыдущих главах в технологический процесс обработки МЖД входит как обязательная операция закалка, которая и формирует в дальнейшем технологическую наследственность изделий по их продольной форме.
Проведенные эксперименты и теоретические выкладки привели к реализации следующей идеи, суть второй в том, что в период нагрева происходит осевая пластическая деформация, за счет разности коэффициентов линейного расширения стапеля и заготовки. Принцип работы установки следующий (рис.3.16).
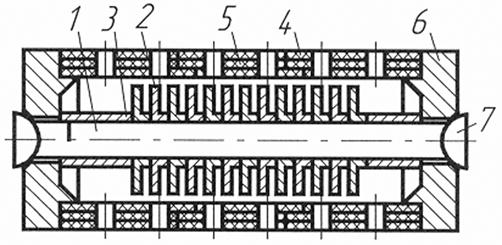
Рис.3.17. Установка для ТСО осевой деформации
На заготовку 1 надевают радиаторы 2 с радиальными пазами. Количество радиаторов 2 и их площадь оценивают потребной поверхностью теплосъема. Величину площади радиаторов регулируют количеством пазов, причем набор радиаторов с разными поверхностями теплосъема обеспечивают равномерное остывание заготовки по всей длине, последняя может иметь сложную форму в продольном и поперечном сечениях. На оставшееся место на заготовку с учетом теплосъема одевают с обеих сторон дистанционные втулки, одну до упора в торец радиаторов 2. Собранную заготовку с радиаторами 2 и дистационными втулками вставляют в многослойный сборно-секционный стапель 3 с наполнителем 4, последний в зависимости от необходимой скорости охлаждения стапеля может иметь и разный коэффициент теплопроводности (например, речной песок с мелкой чугунной стружкой) и фиксируют относительно торцов стапеля 3 крышками-пятами 5. Далее в отверстия крышек-пят вставляют сферические подпятники 6 и накручивают их концы на заготовки 1 до тех пор, пока сферические подпятники 6 не войдут в контакт с крышками-пятами 5, тем самым создают замкнутый силовой контур заготовки со сферическими подпятниками - крышки - пяты - стапель. Отверстие в крышке-пяте 5 выполняется с зазором так, чтобы перекос заготовки мог быть в пределах трех градусов, это позволяет компенсировать технологическую неточность изготовления установки. Собранную конструкцию опускают в шахтную печь и нагревают согласно технологии термообработки до температуры закалки. При нагреве стапель удлиняется больше, чем заготовка, его коэффициент линейного расширения больше, чем коэффициент линейного расширения заготовки. Подбирая численные значения положительной разности коэффициентов линейного расширения стапеля и заготовки, получают величину пластической деформации заготовки, превышающую предел пропорциональности, т.е. предел закона Гука. При необходимости увеличения величины осевой пластической деформации заготовки, например, при правке, необходимо увеличить длину стапеля, а, следовательно, и длину цилиндрической части сферического подпятника, оставляя неизменной длину заготовки.
Осевая пластическая деформация за пределами пропорциональности (закон Гука) при нагреве устраняет технологическую наследственность от предыдущих операций, одновременно правит заготовки. Однако неравномерный режим остывания в свободном состоянии наводит свои неравномерные остаточные напряжения, для исключения этого отрицательного технологического явления необходимо, чтобы стапель 4 остывал медленнее заготовки 1 (т.е. заготовка должна остывать с большей скоростью, чем стапель, минимум в пять раз).
3.6. Экспериментальные исследования влияния термосиловой обработки при отпуске и закалке на геометрическую точность и стабильность форм длинномерных маложестких деталей в условиях функционирования автоматической
Дата добавления: 2015-01-18 | Просмотры: 741 | Нарушение авторских прав
1 | 2 | 3 | 4 | 5 | 6 |
|