Выбор оптимальных условий разливки и формирования слитков кипящей стали
При затвердевании кипящей стали в изложнице на границе между образующимися кристаллами и жидким металлом зарождаются газовые пузыри, котороые, вырастая до определенных размеров, отрываются и всплывают, вызывая кипение стали. С развитием процесса кристализации отрыв пузырей затрудняется, они остаются на месте зарождения, и так как окружающий их металл продолжает затвердевать к центру слитка, то и пузыри растут в этом же направлении, приобретая вытянутую форму, пока не будут замкнуты затвердевающим металлом. Эти вытянутые пузыри называются сотовыми.
Пузыри могут отрываться от места зарождения лишь до тех пор, пока скорость их линейного роста (увеличения радиуса) превышает скорость роста затвердевающей корки. Чем длительнее этот период, тем до большей толщины вырастает плотная корка и тем глубже располагаются сотовые пузыри.
Процесс образования и роста пузырей СО определяется масопереносом кислорода из жидкого металла (из прелегающих участков) к их поверхности.
Количество окиси углерода, образующейся в еденицу времени на еденице поверхности газовыделения , определяется скоростью поступления кислорода к еденице поверхности ( ):
, (7.1)
где а – коэффициент, учитывающий соотношение между количествами расходуемого кислорода и образующейся окиси углерода.
С другой стороны, количество обрзующейся окиси углерола на еденицу поверхности газовыделения определяется перепадом междудавлением выделения окиси углерода ( ) и ее давлением в пузыре ( )
, (7.2)
где – коэффициент, зависящий от скорости массопереноса кислорода из массы жидкого металла к поверхности пузырей:
Перепад давлений пропорционален перепаду концентраций кислорода в диффузионном слое пузырей:
(7.3)
где – содержание кислорода, равновесное с пузырем.
При установившемся процессе образования и роста газовых пузырей
(7.4)
Из уравнения (7.3) видно, что при одном и том же перепаде давлений значение возрастает с увеличением коэффициента массопереноса (подвода) кислорода к фронту кристаллизации и газовыделения.
Из уравнения (7.3) видно, что при одном и том же перепаде давлений значение возрастает с увеличением коэффициента массопереноса (подвода) кислорода к фронту кристаллизации и газовыделения.
Определив количество окиси углерода, образующейся в единицу времени на еденицу поверхности газовыделения, можно вычислить скорости увеличения объема и радиуса газового пузыря:
см/мин (7.4)
где r – размер пузыря, см;
– время от начала затвердевания металла на данном уровне изложницы, мин;
– давление выделения окиси углерода, 0,1 
– константа равновесия реакции окисления углерода;
– скорость разливки, см/мин;
– плотность жидкого металла, кг/ 
– константа скорости процесса, /кг*мин
Скорость роста затвердевающей корки:
см/мин (7.5)
где – l толщина затвердевающей корки металла в момент времени
К – константа скорости кристаллизации, см/ 
В момент прекращения интенсивного отрыва и начала образования сотовых пузырей средняя скорость утолщения затвердевающей корки на некоторую величину m (устанавливается эксперементально):
(7.6)
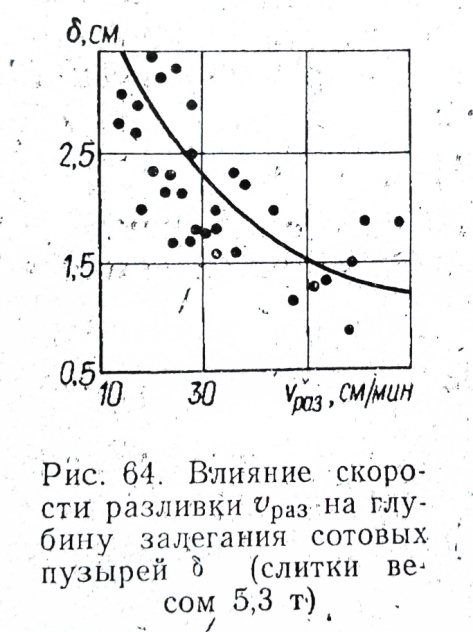
Так как скорость роста затвердевающей корки металла в момент времени имеет определенное значение (7,5) для получения более толстой беспузырной корки необходимо повысить скорость роста пузыря. Это достигается, как видно из уравнения (7.4) уменьшением скорости разливки, увеличением давления выделения окиси углерода и скорости подвода кислорода к поверхности пузырей (ростом значения ). Зависимость толщины беспузырной корки от скорости разливки показана на рис.64. При более быстрых разливке и нарастании ферростатического давления скорость линейного роста пузырей на данном уровне наполнения изложниц понижается до критического значения раньше, поэтому образование сотовых пузырей начинается ближе к поверхности слитка.
Давление выделения окиси углерода при данном содержании [C] определяется концентрацией [O]. Вот почему, изменяя последнюю в слое металла, прилегающем к образующимся при затвердевании слитка кристалам, можно регулировать толщину беспузырной корки. Концентрация кислорода в этом слое не равна первоначальной (при
поступлении в изложницу), так как в затвердевающем металле происходят процессы (ликваци, химические реакции между марганцем, углеродом и кислородом в жидкой стали), вызывающие изменения содержания кислорода в участках жидкого металла, прилегающегок образующимся кристаллам. Происходящяя ликвация приводит к увеличению содержания кислорода и других примесей в этих участках. Если получающаяся концентрация кислорода в рассматриваемом слое превысит значение, которое соответствует равновесию с содержащимся в металле марганцем, то начинается реакция раскисления стали марганцем. В результате раскисления содержание кислорода в этом слое поддерживается на уровне, соответствующем равновесию между марганцем и кислородом в металее при температуре, близкой к температуре начала кристализации.
Таким образом, марганец, регулируя содержание кислорода в жидкой стали у фронта кристализации, определяет велечину давления окиси углерода и, следовательно, ход образования безпузыристой корки. Кислород, расходующийся при образовании пузырей, поступает также из атмосферы (поглощение кислорода струей, каплями и через зеркало металла). Часть этого кислорода в верхних слоях металла, вступая в реакции с железом, марганцем и другими примесями, образует при разливке и после нее шлак на поверхности кипящей стали. Марганец блокирует и регулирует поступление кислорода из атмосферы и шлака в глубинные слои металла и к фронту газовыделенни. В этом также, по видимому, проявляется его роль как регулятора кипения.
Концентрация кислорода в металле к моменту ввода в него углерода. Сопоставление равновесных концентраций кислорода, которые могут быть достигнуты при содержании марганца 0,25-0,5% в киплящей стали, с концетрацией кислорода в металле к началу раскисления (рис.65), показывает что в обычных для кипящей стали температурных условиях вводимый металл марганец не вступает в реакцию с растворенным кислородом. Раскисляющая роль марганца проявляется в период кристализации.
Изменение содержания кислорода и марганца в металле в результате ликвации можно рассчитать по имеющимся коэффициентам ликвации.
На рис.66 прямоугольник abdc ограничивает область состава металла по
содержанию кислорода и марганца, соответствующуюдиапазону концентраций углерода от 0,083 до 0,270% и марганца от 0,25-0,5%. На этом рисунке показано изменение содержания кислорода и марганца в результате ликвации (линии xx’,yy’, и zz ’, где x, y, z, x’, y’, z’ – составы жидкого металла соответственно в начале кристализации и в момент, когда в результате ликвации становится возможной реакция между растворенным в стали марганцем и кислородом).
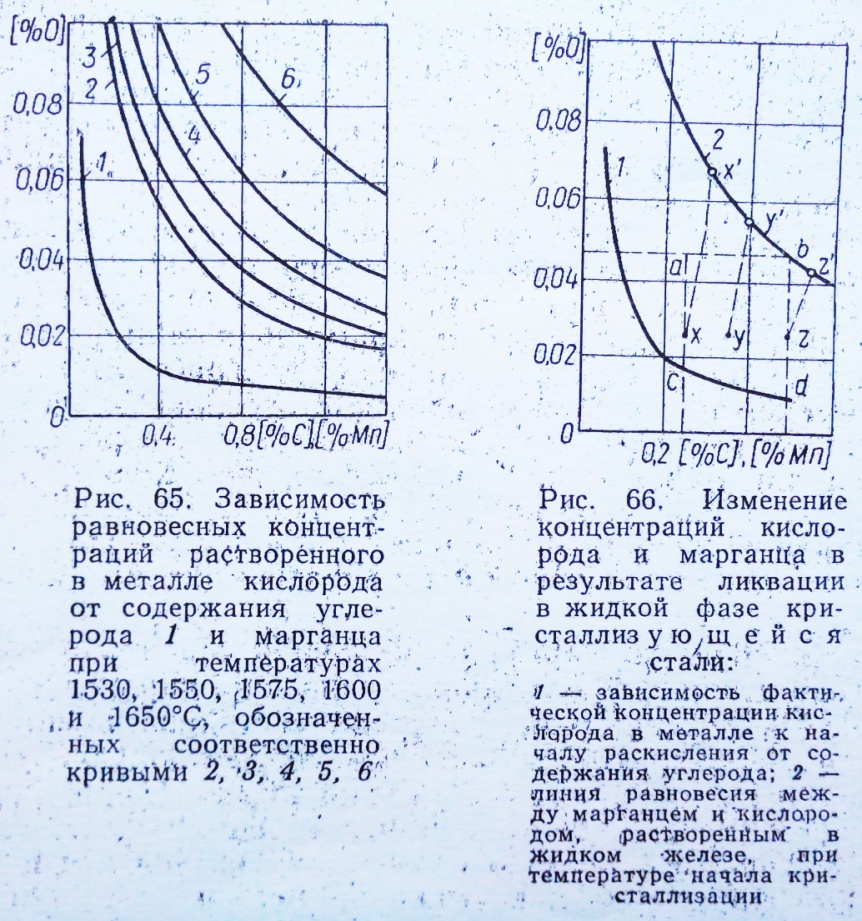
Например, если начальное содержание кислорода равно 0,025%, то в слое металла, примыкающем к образующимся кристаллам, взаимосвязь концентраций марганца и кислорода соответственно будет такой (%): 0,25; 0,50; и 0,068; 0,054; 0,043.
Итак, правильное использование марганца в качестве регулятора содержания кислорода в жидком металле при кристаллизации является важной технологической задачей.
Для получения требуемой структуры слитка кипящей стали (достаточная толщина беспузырной корки, слабое развитие рослости или усадки)
необходимо обеспечить определение скорости разливки, давление
выделения окиси углерода и содержащего расстворенного кислорода в жидком металле прилегающему к фронту кристализации. Получение же заданной концентрации кислорода обусловливается соответствующим содержанием марганца в жидкой стали. Отклонение от этого содержания в ту или иную сторону вызывает ухудшение условий формирования слитка кипящей стали. Более низкое, чем требуется, содержание марганца обусловливает повышенную концентрацию кислорода в жидком металле около кристаллов, что приводит к увеличению интенсивности кипения и в результате – к вспениванию металла и развитию усадочных дефектов в слитке (рис.43, б,в). Повышенное содержание марганца вызывает снижение концентрации кислорода в жидком металее около кристаллов, в результате чего кипение ослабляется, что сопровождается близким к поверхности слитка расположением сотовых пузырей и развитем рослости (рис.43, г).
Формирование сотовых пузырей начинается уже во время наполнения. Это было подтверждено следующим опытом: в две соседние изложницы на одном и том же поддоне (сифонная разливка) для прекращения кипения добавили алюминия по 230 г/т стали (в одну – сразу же после заполнения, а в другую – через 12 мин). Разрезы слитков показали, что толщина беспузыристой корки в них одинакова. Установлено, что продолжительность кипения в изложнице после наполнения не оказывает заметного влияния на глубину залегания сотовых пузырей.
Глубина залегания сотовых пузырей и уровень их распространения по выстое слитка, зависят друг от друга: чем меньше толщина беспузыристой корки, тем на большую высоту распространяются сотовые пузыри. Эта закономерность объясняется следующим. На данном уровне высоты изложницы возможность образование сотовых пузырей исключается, если время в течении которого они еще могут отрываться больше времени наполнения от этого уровня до полной высоты слитка.
Увеличению же времени интенсивного газовыделения и отрыва пузырей высоты части слитка,не пораженной сотовыми пузырями,способствуют те же факторы(уменьшение скорости разливки,повышение содержания кислорода в металле и др.),которые приводят к росту толщины безпузыристой корки.
Влияние температуры металла на толщину безпузыристой корки слитка не очень велико и имеет эксперементальный характер.Однако с повышением температуры металла при разливки особенно выше допустимых и оптимальных значений кипение в изложницах ослабляется,а толщина плотной корки
уменьшается.Вероятной причиной этого является снижение скорости роста корки,что ослабляет ликвационное накопление кислорода у фронта кристаллизации) и повышение скорости отвода кислорода от слоев металла к прилегающим к растущим металлам и обагащенных кислородом,к сердцевинным слоям жидкой стали в связи с изменением условий диффузии это приводит к уменьшению [O], и скорости роста пузырей.
Технология разливки кипящей стали должна предусматривать обязательное обеспечение формирование слитков без роста и усадки (рис.43 а, г). Невыполнения этого требования приводит к увеличению головной обрезки, т.е. к возростанию расхода металла на еденицу проката.
Рост и усадка кипящей стали в изложницах является результатом несоответствия объемов газовых пузырей,образующихся внутри жидкого металла и выходящих из него в атмосферу (в еденицу времени).
Усадку кипящей стали вызывает вспенивание при разливке (черезмерно интенсивное газообразование), и последующее оседание пены.Вспенивание металла характеризуется значительной скоростью образования пузырей, превышающей возможную скорость их удаления из-за пониженной концентрации марганца,высокого содержания кислорода и др. Это объясняется повышенной концентрацией кислорода в слое жидкой стали контактирующей с кристаллом. Рост металла наблюдается при недостаточно интенсивном газовыделении т.е. при раннем образовании и значительном распространении сотовых пузырей продолжается и после окончания наполнения изложницы, в результате чего образующиеся новые объемы окиси углерода вытесняют металл выше уровня наполнения.Общий объем сотовых пузырей получается тем больше,чем выше уровень их распространения и меньше толщина безпузыристой корки. Росту слитка способствуют те факторы, которые обуславливают малую толщину беспузыристой корки: низкое содержание кислорода в жидкой стали около кристаллов (результат повышенной концентрации марганца или перераскисленности металла), быстрая разливка (см рис. 43 г) и др.
Итак для получения качественного слитка кипящей стали (с достаточной толщиной беспузыристой корки, без роста или усадки) необходимо в каждом конкретном случае обеспечить оптимальное сочитание технологических факторов, определяющих интенсивность ликвационного накопления и
массопереноса(содержания кислорода и марганца в металле, скорость и температуры разливки).
Сифонная разливка, характеризующаяся относительно низкими скоростями подъема металла в изложницах,позволяет сравнительно легко получать слитки с достаточно толстой беспузыристой коркой и малой рослостью(см рис 64 и 67). При этом должно быть оптимальное содержания марганца в стали.
Как уже отмечалось содержание марганца в металле определяет концентрацию кислорода в слое прилегающем к кристаллам,а следовательно и значение . Связь между содержанием марганца и кислорода при температуре кристаллизации определяют из выражения
(7.7)
Чтобы получить значение выделения окиси углерода, обеспечивающие оптимальную толщину беспузыристой корки при увеличении концентрации углерода в металле, необходимо уменьшить содержание углерода около фронта кристаллизации, т.е. повысить концентрацию марганца.
Подставив в уравнение значение [%O] из выражения (7.7) получим:
(7.8)
Из уравнения (7.8) видно, что значение находится в обратной зависимости от величины отношения . Следовательно,изменяя последнюю можно регулировать значения давления выделения окиси углерода.
Получение здорового слитка кипящей стали достигается при оптимальных скорости литейного роста пузыря и увеличение отношения Конкретные величины этого отношения могут быть установлены для каждого варианта производственных условий.
На рис 68 показаны значения,получены для скорости отливки слитка весом5,3 т. При повышении содержания С в металле концентрация марганца должна увеличится:
[%C] < 0,10 0,11–0,14 0,15–0,18 0,19–0,22>0,25
[%Mn] < 0,42 0,43 0,46 0,51 0,55
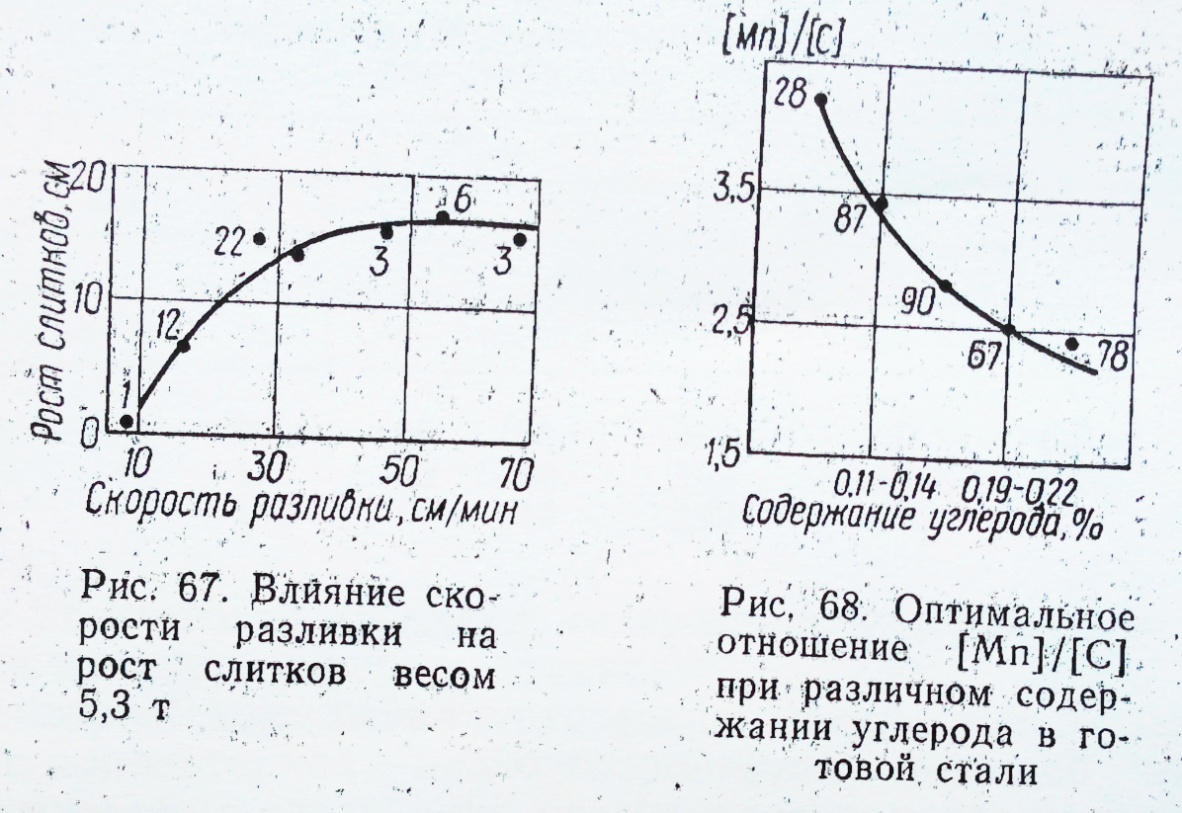
В последнее время широко распространяется скоростная разливка кипящей стали сверху. В этом случае качественный слиток может быть получен в результате увеличения скорости поступления кислорода к фронту кристаллизации и газовыделения путем присадки в изложницу(во время ее наполнения окислителей)- интенсификаторов кипения.
На заводе им. Ильича для интенсификации кипения в изложницы присаживают порошкообразную смесь состава: 70% окалины, 20-плавикового шпата и 10% соды. Добавка плавикового шпата и соды способствует услилению барбортажа, что обеспечивает ускорение транспортирование кислорода к зоне кристаллизации. Посадку смеси начинают после полного открытия стопора и заканчивают, когда уровень металла не доходит до полной высоты на 200-300 мм. Расход смеси составляет 500-600 т/гдля стали 2кп и 600-800г/т для стали 3 кп. Применение окислительной смеси этого состава позволило отливать слитки весом 16-19 т из 480 тонного ковшачерез стакан диаметром 80мм,чтобы обеспечить скорость разливки около 2м/мин и получение плотной безпузыристой корки достаточной толщины (10-12 мм).
При разливке кипящей стали с повышенным содержанием С исп. Брикеты, состоящие из 80% окалины и 20% фтористого натрия (0,5 кг/тон). Брикеты раскладывают на бортах изложницы и через 5-7 с после начала разливки сбрасывают в металл.
При переходе на скоростную разливку кипящей стали необходимо не только применять меры по обеспечению по достаточной толщины беспузыристой корки,но и создать условия,предупреждающие образование горячих трещин. Это может быть достигнуто в результате применения изложниц с внутренней волнистой поверхностью.
Интенсификация кипения стали в изложнице способствует также обдув кислородом струи металла,поступающего в изложницу. Его в частности использывали при разливке низкоуглеродистой кипящей стали,выплавляемой в 130-тонных кислородных конверторах. Кислород подавали струей металла через 15 мм трубку с диффузорным насадком из листового железа(для большего контакта со струей металла)имеющий диаметр на выходе 50 мм. Трубку устанавливали на расстоянии 100-150 мм от струи металла. Давление кислорода и метод его подвода подбирали таким образом,чтоб не нарушалось организация струи металла.Давление кислорода и метод его пдвода,подбирали таким образом,что бы не нарушалась организация струи металла.Расход кислорода составил 0,2-0,3 стали.
Колебания технологических условый иногда приводит к тому,что концентрация кислорода в металле к моменту,превышает необходимую для получения качественной структуры слитка.Это увеличевает скорость поступления кислорода к фронту кристаллизации,вспенивание металла и последуйщую усадку слитка. Для понижения концентрации кислорода в ковш добавляют алюминий: чем ниже содержание С и Mn в металле, тем тем большей должна быть присадка алюминия.
Дата добавления: 2015-01-18 | Просмотры: 965 | Нарушение авторских прав
1 | 2 | 3 | 4 |
|