Определение температурных напряжений в дисках произвольного профиля
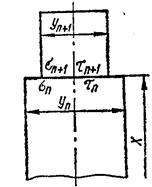
Рис.37. участки постоянной толщины диска.
Вследствие того, что рабочие лопатки диска омываются паром, имеющим высокую температуру, а ступица диска «сидит» на валу турбины, шейки которого охлаждаются смазочным маслом (температура последнего обычно не превышает 60° С), температура различных участков диска будет разной. Закон изменения температуры в диске вдоль радиуса может быть установлен экспериментально; в расчетах же ориентировочно принимают, что температура в диске меняется по закону

где Θ — разность между температурами диска на радиусе х и в центре;
Θi, — разность между температурами диска на внутренней поверхности расточки ступицы и в центре;
xt —радиус расточки внутренней поверхности ступицы диска. Поэтому действительная температура диска на радиусе х определяется выражением
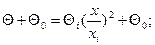
где Θ0 — действительная температура диска (вала) в его центре.
По этим соотношениям строят кривую изменения температуры в диске вдоль радиуса.
Для расчета температурных напряжений на различных участках диска его профиль заменяют ступенчатым, как это делают при расчете динамических напряжений в диске, используя также метод «двух расчетов». Расчет ведут от внутреннего радиуса ступицы к наружному радиусу обода.
Радиальные и тангенциальные температурные напряжения на наружной поверхности первого участка диска рассчитывают по формулам


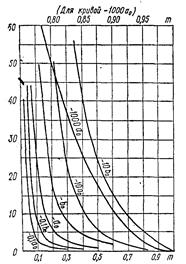
Рис.38. График для определения коэффициентов a0,b0 при расчете температурных напряжений в диске постоянной толщины
Здесь σt, τt — радиальные и тангенциальные температурные напряжения на внутренней поверхности первого участка;
ar=β τ и a τ =β r — коэффициенты, значения которых определяют точно так же, как и при расчете радиальных и тангенциальных динамических напряжений; а и b — коэффициенты, значения которых определяют так:
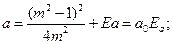
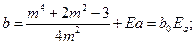
где m = xi/x1 отношение внутреннего радиуса первого участка диска к наружному радиусу этого же участка.
Для уменьшения вычислений следует воспользоваться графиком, изображенным на рис. 38. Чтобы определить по нему значения коэффициентов а0 и bо, нужно из точки на оси абсцисс, соответствующей заданному т, восстановить перпендикуляр до пересечения с соответствующими кривыми, и из полученных точек опустить перпендикуляры на ось ординат, сделать отсчеты и умножить их на коэффициент, стоящий перед а0 или bо на кривой с соответствующим знаком.
В первом расчете на внутренней поверхности первого участка принимают σi= 0, а τi, — произвольным по величине. Используя формулы, рассчитывают а и τ. Для дисков без отверстий радиальные и тангенциальные температурные напряжения в центре диска выбирают произвольными, но одинаковой величины (σ0 = τ0).
Напряжения на внутренней поверхности второго участка определяют по формулам для расчета динамических напряжений, приведенным выше.
Переходя от участка к участку, доходят до определения напряжений на наружной поверхности последнего участка диска σа и τа. Если величина σа не равна 0, то производят второй расчет для неподвижного диска, нагруженного напряжениями σi = 0 и τi — произвольным по величине.
Чтобы не делать второго расчета, можно использовать второй расчет при определении динамических напряжений в диске, после чего определить действительные температурные напряжения. Для этого из уравнения σ а = σIa+kσIIa находят значение коэффициента k, на который необходимо умножить температурное напряжение при втором расчете σIIa с тем, чтобы, сложив это произведение с напряжением при первом расчете σIa, получить действительное радиальное температурное напряжение на наружной поверхности последнего участка диска σ а= 0. При этом


Рис.39. Динамические и температурные напряжения в диске произвольного профиля.
Данные по расчету коэффициентов, входящих в формулы для определения динамических и температурных напряжений в диске, а также данные по непосредственному расчету этих напряжений заносят в табл. 6, 7. Таблиц 7 составляется две: одна — для динамических, а вторая — для температурных напряжений. Истинные значения динамических и температурных напряжений в диске отображают графически в виде зависимостей σ = f(х) и
τ = f(х), как показано на примере рис. 39. Для изготовления дисков паровых турбин небольшой мощности и работающих при невысоких температурах (до 300° С) применяют сталь марки 45. При более высоких температурах используют стали
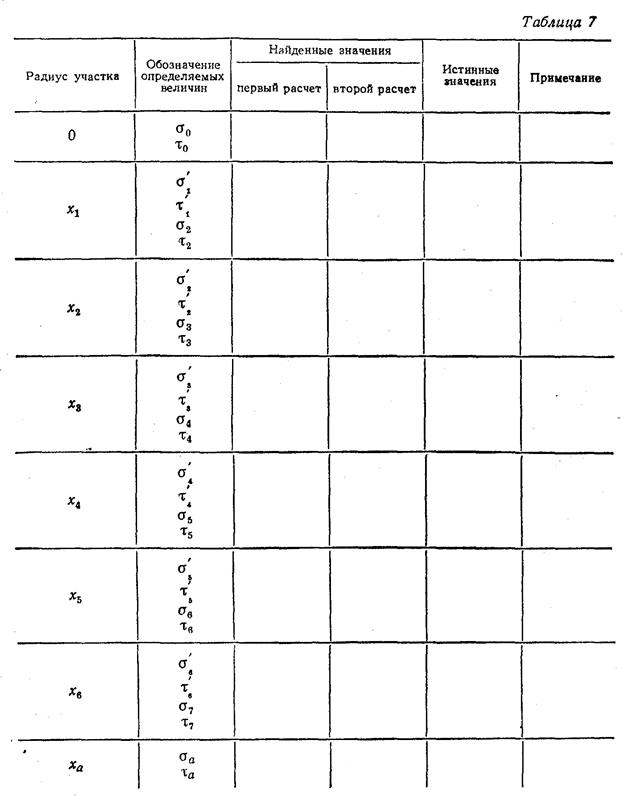

перлитного класса следующих марок: 34ХНЗМ (до 400°С), 34ХМ (до 500° С), 25Х1М1Ф (до 540° С) и 20ХЗМВФ (до 560°С). Характеристики всех вышеуказанных сталей приведены в табл. 8.
При расчете дисков с температурой металла ниже 430°С критерием прочности для перлитных сталей является предел текучести σ0,2. При более высоких температурах необходимо учитывать также предел длительной прочности σдл и предел ползучести σ пл.
Коэффициенты запаса прочности рекомендуется брать следующие:
КT = 2,2; Kдл = 1,65; Кпл— 1,25.
Допустимые напряжения соответственно будут:

Допустимым считается минимальное из трех получаемых напряжений.
Дата добавления: 2016-03-26 | Просмотры: 575 | Нарушение авторских прав
1 | 2 | 3 | 4 | 5 | 6 | 7 | 8 | 9 | 10 | 11 | 12 | 13 | 14 |
|