АкушерствоАнатомияАнестезиологияВакцинопрофилактикаВалеологияВетеринарияГигиенаЗаболеванияИммунологияКардиологияНеврологияНефрологияОнкологияОториноларингологияОфтальмологияПаразитологияПедиатрияПервая помощьПсихиатрияПульмонологияРеанимацияРевматологияСтоматологияТерапияТоксикологияТравматологияУрологияФармакологияФармацевтикаФизиотерапияФтизиатрияХирургияЭндокринологияЭпидемиология
|
Система автоматического управления главными
формообразующими подсистемами "резец-суппорт" и
"деталь-опоры".
Точность механической обработки зависит от многих факторов, важнейшим из которых является упругая деформация системы при статических и динамических воздействиях, приобретающая особо важное значение при обработке нежестких заготовок. При высоком уровне развития производства одной из основных задач науки становится изыскание резервов для дальнейшего увеличения показателей качества.
Одним из путей повышения точности обработки маложестких деталей является метод, основанный на автоматическом управлении ходом технологического процесса. Создание станков повышенной точности не решает задачу обработки маложестких деталей, т.к. в этом случае точность и качество обрабатываемой поверхности детали определяется ее динамическими параметрами. Одним из эффективных методов, позволяющих решить задачу, связанную с обработкой маложестких деталей, является встройка в технологическую систему станка системы автоматического управления. САУ стабилизации вершины резца и оси заготовки представленная функциональной схемой (рис.2.21), работает следующим образом. В процессе обработки функционируют три контура управления одновременно.
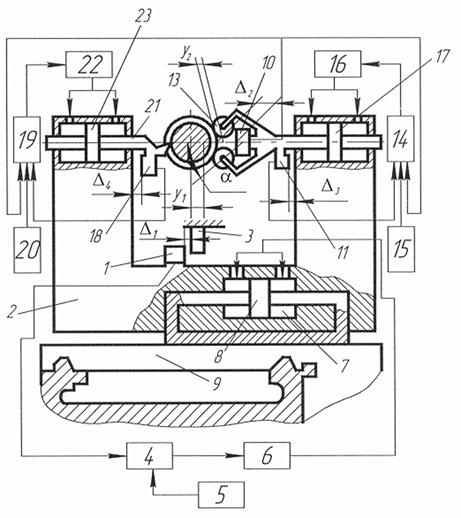
Рис.2.21. Трехконтурная САУ
Перед началом точения включается первый контур-стабилизации положения корпуса резцедержателя, при этом бесконтактный датчик 1, жестко закрепленный на корпусе 2 относительно искусственной базы 3 (последняя устанавливается на станине и может быть сменной и регулируемой в радиальном направлении обрабатываемой детали), устанавливается с зазором D1, относительно искусственной базы 3 и в случае перемещения корпуса резцедержателя 2 в плюс или минус относительно искусственной базы 3 датчика 1 выдает электрический сигнал, пропорциональный величине перемещения корпуса резцедержателя с учетом знака на дифференциальный усилитель 4, выполненный по мостовой схеме, где этот сигнал сравнивается с сигналом задатчика 5, усиливается и подается на электромагнитный преобразователь 6, последний распределяет рабочее давление в сервоприводе 7 и, тем самым, перемещает корпус резцедержателя 2 относительно шток-поршня 8, который установлен на суппорте 9 базового станка, до тех пор, пока сигнал рассогласования не станет равен нулю. В процессе резания, независимо от внешних или внутренних возмущений, порождающих перемещение корпуса резцедержателя 2, контур управления стабилизирует его положение относительно искусственной базы 3 по всей длине обрабатываемой детали. Стабилизация корпуса резцедержателя на всем пути его движения позволяет создать искусственную базу отсчета и измерения для контуров стабилизации вершины резца и оси детали, исключая при этом все погрешности, вносимые на базовом станке направляющими и ходовыми винтами.
Второй контур - стабилизации оси детали - перед процессом резания настраивается по эталонной детали с размером базовой поверхности равным номинальному (например, наибольшему предельному) диаметру обрабатываемой детали. При этом опора-призма должна быть установлена в положении, при котором ось эталонной детали с номинальным диаметром параллельна поверхности базы 3, а бесконтактные датчики 10 и 11 устанавливаются при этом с начальными зазорами D2 и D3, первый относительно базовой поверхности детали, а второй относительно корпуса резцедержателя 2, это положение датчиков будет соответствовать номинальному диаметру обрабатываемой детали и параллельности оси детали к рабочей поверхности искусственной базы 3. Постоянные составляющие сигналов датчика 10, контролирующего положение базовой поверхности детали, и датчика 11, контролирующего положение опоры-призмы 12, сбалансированы при настройке по эталонной детали и их результирующий сигнал равен нулю. Опора-призма 12 своими опорными поверхностями 13 (последние выполнены в виде тел качения из материала с большим коэффициентом демпфирования) контактирует с обработанной поверхностью детали на предыдущих операциях. Если диаметр обрабатываемой детали меньше номинального диаметра эталонной детали, то при установке в опору-призму ее ось сместится на величину от точки О, а базовая поверхность детали сместится, следовательно, на величину . Эти величины связаны уравнением , в соответствии с которым настраивается дифференциальный усилитель 14, выполненный по мостовой схеме (здесь a - половина угла опоры-призмы).
Датчик 10 выдает сигнал (его постоянная составляющая пропорциональна перемещению ), который поступает на дифференциальный усилитель 14, последний оснащен задатчиком начального положения опоры-призмы 15. Дифференциальный усилитель 14 усиливает сигнал с датчика 10 и подает на вход электромагнитного преобразователя 16, который распределяет давление в рабочих полостях сервопривода 17, поршень-шток которого представляет одно целое с опорой-призмой. Опора-призма 12 по команде усилителя 14 с помощью электромагнитного преобразователя 16 и сервопривода 17 перемещается в направлении биссектрисы. При этом датчик 11 начинает выдавать сигнал, меняющийся по мере перемещения опоры-призмы 12. При совмещении центра обрабатываемой детали с центром эталонной детали, сигналы с датчиков 10 и 11 балансируются в усилителе 14 и результирующий сигнал становится равным нулю, обработка постоянных составляющих сигналов с датчиков 10 и 11 прекращается. В случае биения обрабатываемой детали, с датчика 10, регистрирующее это биение, выделяется переменная составляющая и преобразуется в электрический сигнал, который подается на усилитель 14, где усиливается и в фазе поступает на последовательно включенные преобразователь 16, сервопривод 17. Последний отрабатывает переменную составляющую этого сигнала, что приводит к колебаниям опоры-призмы 12 с частотой, амплитудой и фазой, равными колебаниям обрабатываемой детали. При этом первоначальный зазор датчика 10 сохраняется в течении каждого оборота детали, что приводит к стабилизации амплитуды относительных колебаний детали и опоры-призмы.
Третий контур-стабилизации положения вершины резца - работает следующим образом. Сигналы с датчика 10 контроля текущего размера (переменные составляющие) поступают на вход дифференциального усилителя 19. Датчик 18, закрепленный на резце 21, устанавливается с помощью задатчика 20 относительно корпуса резцедержателя с начальным зазором D4, что соответствует заданной глубине резания. В процессе резания, в случае отжима резца или биения детали, появляются сигналы рассогласования на дифференциальном усилителе 19 по постоянной и переменной составляющей от датчиков 10 и 18. Усиленные сигналы с усилителя 20 поступают на вход электромагнитного преобразователя 22 с учетом знака, последний распределяет давление в рабочих полостях сервопривода 23 и перемещает резец 21 на величину, пропорциональную отжиму резца (постоянная составляющая сигнала датчика 18), и на величину, пропорциональную амплитуде биения детали, но с обратным знаком.
Все три контура идентичны и выполнены на стандартных элементах. Первичные преобразователи (вихретоковые) датчики контроля имели линейную статическую характеристику в диапазоне 0…1,2 мм при начальном зазоре 2 мм, а ширина рабочего диапазона частот была в пределах от 0 до 5 × 103 Гц. Контуры управления имели постоянную времени , ошибку (точность слежения) по возмущению равную , величину относительного перерегулирования . Динамические характеристики снимались при рабочем давлении в сервоприводах в диапазоне 3…5 н/м2. Использование САУ полностью исключает влияние неточности направляющих и ходовых винтов станка на точность обработки и увеличивает межремонтный цикл станка.
Для расширения технологических возможностей контура стабилизации оси детали в него был встроен дополнительный контур минимизации уровня вибраций ПДО, который работает следующим образом (рис.2.22). Первичный преобразователь (бесконтактный датчик линейных перемещений) 1 настраивается с начальным зазором D1 относительно обрабатываемой детали и крепится на опоре-призме 2, последняя выполнена из упругих элементов 3 и прижимных роликов 4. Силовое замыкание осуществляется путем управления зазором D1 по программе или от задатчика. Выходной сигнал, пропорциональный колебаниям обрабатываемой детали, поступает на вход дифференциального усилителя 5, где сравнивается с сигналом задатчика 6, а их разностный сигнал усиливается и поступает на вход электромагнитного преобразователя 7, где преобразуется в линейные перемещения золотника 8, последний распределяет рабочее давление и управляет шток-поршнем 9 сервопривода 10. Шток-поршень 9 жестко соединен с опорой призмой 2. Второй первичный преобразователь 11 (датчик вибраций) установлен с начальным зазором D2 и регистрирует уровень вибраций обрабатываемой детали относительно станины станка. Его выходной сигнал поступает на блок 12 уровня вибраций, где сравнивается с сигналом задатчика 13 уровня вибраций, и в случае превышения заданного уровня вибраций сигнал с блока 12 поступает по цепи управления на сервопривод 10, что позволяет осуществлять управление за счет фиктивной жесткости, полученной при помощи обратной связи. Для управления по фиктивному демпфированию или фиктивной массе, сигнал с блока 12 поступает на блок 14 дифференцирования и далее на блок 15 вторичного дифференцирования, выходные сигналы трех блоков 12, 14 и 15, отдельно каждый или последовательно включенные, поступают на сервопривод 16 и далее на управляемый редуктор 17, давление в которой создается насосной станцией 18. Если изменить параметры второго контура: коэффициент усиления датчика 11, коэффициенты усиления , и блоков 12, 14 и 15, коэффициент усиления сервопривода 16, коэффициент управляемого редуктора 17 и коэффициент сервопривода 10, то изменяются и фиктивные параметры механической системы СПИЗ станка. Так как жесткости подсистемы "деталь-опоры" прибавится фиктивная жесткость , полученная при помощи контура управления обратной связи. В случае необходимости можно применять три разновидности контуров управления, включая три соответствующих виброгасителя - по перемещению, скорости и ускорению.
САУ позволяет изменять резонансные свойства системы СПИЗ в широких пределах как вручную от задатчика, так и автоматически по любому, наперед заданному закону, так как изменение фиктивных параметров системы СПИЗ достигается в результате управления электронными элементами и одновременного изменения реальной жесткости исполнительного механизма опоры-призмы.
В тоже время САУ позволяет изменять фиктивные параметры и по нелинейным законам, для этого достаточно ввести в цепь контура нелинейные звенья.
Особенностью предложенного метода минимизации вибраций при резании заключается в том, что быстродействие и величины таких параметров как масса заготовки, демпфирующие способности ПДО можно повысить и увеличить только за счет введения контуров обратной связи. Представим механическую модель обрабатываемой заготовки, как сосредоточенную массу закрепленную на пружине с коэффициентом демпфирования b и закрепленным параллельно пружине. Тогда дифференциальное уравнение описывающее движение ПДО имеет вид , где - сила действующая со стороны электрогидропривода на массу заготовки. Так как в САУ имеется отрицательная обратная связь по скорости, т.е. включен блок дифференцирования 14, то сила определится из уравнения , где , - коэффициенты усиления контура управления и блока дифференцирования соответственно. Подставляя полученное значение для в уравнение движения получим , где - коэффициент фиктивной жесткости подсистемы «деталь-опора». Для получения регулируемой фиктивной массы достаточно ввести в контур обратной связи двойное дифференцирование (рис.2.22) и в этом случае сила . Тогда уравнение движения ПДО будет , где - фиктивная масса.
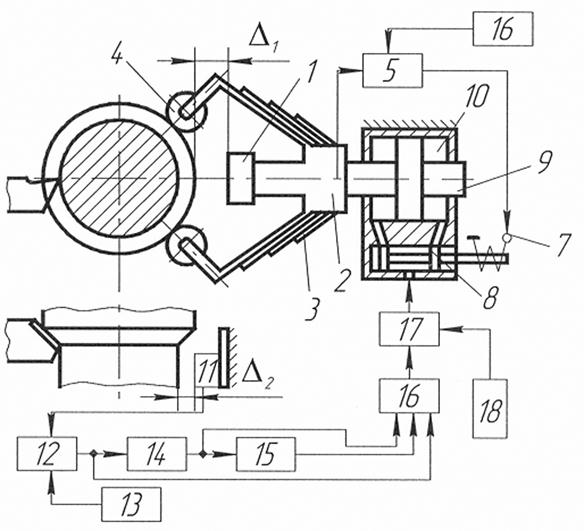
Рис.2.22. САУ подсистемы "деталь-опоры"
В случае необходимости можно применять сразу две разновидности управления.
Этим методом можно регулировать все параметры линейной и нелинейной колебательной системы любого порядка, и, следовательно, изменять резонансные свойства ПДО в широких пределах, Предлагаемый метод может найти применение для гашения вибраций различных систем работающих в переходных режимах, т.е. там, где необходимо быстродействие системы управления параметрами. Следует заметить, что пределы изменения параметров колебательной системы по описанному методу ограничены только мощностью электрогидроприводов. Амплитуду резонансных гармонических колебаний в стационарном режиме при согласовании параметров можно определить из следующего выражения , где . Задаваясь амплитудой колебаний А, можно определить величины , , .
В рассмотренных ранее САУ (рис.2.21 и 2.22) стабилизировались параметры СПИЗ, но не минимизировались параметры процесса резания, а следовательно, не управлялось качество обрабатываемой поверхности детали, остаточные напряжения, шероховатость, наклеп. С целью расширения технологических возможностей процесса мехобработки САУ стабилизации вершины резца, дополнилась контурами минимизации и стабилизации сил резания. Суть функционирования такой системы в следующем (рис.2.23). Включается первый контур управления стабилизации инструмента в радиальном положении, в этом случае механизм 1 малых перемещений инструмента устанавливают в крайнее положение от обрабатываемой детали путем подвода первичного преобразователя 2 положения инструмента, с помощью задатчика 3 глубины резания (микровинт) последний устанавливается на поперечном суппорте базового станка с начальным зазором относительно первичного преобразователя 2. При перемещении под действием внешней силы механизм 1 и закрепленный на нем первичный преобразователь 2 перемещаются, а следовательно зазор изменяется. Это механическое перемещение, преобразованное в электрический сигнал, поступает на вход дифференциального усилителя 4, который усиливает этот сигнал и с учетом знака подает его на электромеханический преобразователь 5, последний управляет сервоприводом 6, который в свою очередь перемещает механизм 1 малых радиальных перемещений.
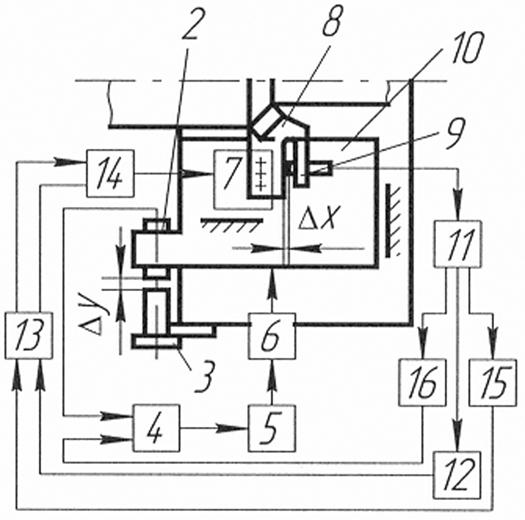
Рис.2.23. САУ стабилизации сил резания
Таким образом, первый контур управления обеспечивает заданное положение инструмента в радиальном направлении. Механизм 7 малых осевых перемещений инструмента не имеет степени свободы по оси Y, а имеет управляемое перемещение по оси X. Второй контур управления обеспечивает стабилизацию минимальной составляющей силы изменяемых в течение одного оборота. На механизме 7 малых осевых перемещений жестко крепится державка 8, на последней крепится режущая пластина, причем державка имеет динамометрический рычаг 9 консольного типа, на свободном конце которого закреплен первичный преобразователь 10 регистрации деформаций инструмента в осевом направлении по оси X. Расстояние, на котором крепится первичный преобразователь 10, определяется режимами резания и конструкцией резце державки. С целью повышения коэффициента усиления контура управления желательно закреплять первичный дает их на вход усилителя сигналов 11, последний усиливает величину входного сигнала до нужного уровня.
Усилитель сигналов 11 имеет три выхода, которые подключены к входам трех каналов. Первым канал управляет (минимизирует) составляющей силы в течение одного оборота следующим образом. Сигнал с выхода усилителя сигналов 11, пропорциональный изменению составляющей силы резания и усиленный поступает на вход блока 12, где формируется сигнал управления, оценивается минимальная амплитуда силы резания, которая пропорциональна минимальной величине припуска срезаемого слоя. Разностный сигнал (сигнал управления) поступает на вход электромеханического преобразователя 13 с алгебраическим знаком, последний управляет гидравлическим сервоприводом 14 так, что механизм 7, а следовательно, и инструмент, закрепленный на нем, перемещается в течение одного оборота по оси Х так, что переменная составляющая остается минимальной и стабильной на всем протяжении съема металла, т.е. при большем припуске инструмент отходит по оси X к заданной бабке, что соответствует уменьшению амплитуды перемещений составляющей силы , до тех пор, пока площадь съема не станет равной минимальной, что соответствует минимальной силе резания, следовательно, амплитуда переменной составляющей силы стремится к минимуму.
Величина амплитуды определяется величиной ошибки работы канала управления и может быть сведена к минимуму. Таким образом, инструмент, имея рабочую продольную подачу, получает дополнительно управляемые малые перемещения, которые накладываются на большие рабочие перемещения, создавая равномерный съем (площадь съема в течение одного оборота постоянна) металла, следовательно, стабилизируя постоянную составляющую силы резания , что приводит к стабилизации переменных составляющих и , т.е. к равно напряженному по величине и направлению поверхностному слою.
Это особенно важно при формировании стабильного уровня остаточных напряжений. Сформированный равно напряженный слой металла на поверхности детали приводит и к стабилизации оси последней в пространстве, т.е. исключает коробление, особенно интенсивно это проявляется при обработке маложестких деталей.
Для повышения качества обработки поверхности и снижения уровня постоянных составляющих сил , и , а также для повышения точности обработки управляемого сигнала и устойчивости первого канала параллельно ему работает второй канал. Сигнал с усилителя сигналов 11 подается на вход блока 15, в котором вырабатывается осциллирующий сигнал управления с определенным уровнем по амплитуде и частоте колебаний, далее поступает на вход электромагнитного преобразователя 13, выход последнего включен на вход сервопривода 14, который управляет малыми перемещениями механизма 7 по оси X. Частота и величина амплитуды колебаний определяется блоком 15 в функции режимов резания, физико-механическими свойствами обрабатываемого материала, качеством обрабатываемой поверхности детали. Верхний предел по частоте обработки определяется быстродействием сервопривода 14 и массы механизма 7. Для упрощения системы управления оптимальные параметры (амплитуды и частоты) определяются опытным путем и вводятся в блок 15 с помощью задатчиков (не показаны).
Работа первого контура управления обеспечивает стабилизацию инструмента относительно базового суппорта станка, но по мере передвижения инструмента вдоль детали по оси X последний изнашивается, что приводит к потере точности обрабатываемой детали, а при обработке длинномерных деталей с частой перестройке и потери производительности. Для компенсации размерного износа режущей кромки инструмента во второй контур управления вводится третий канал, работающий совместно с первым контуром управления. Третий выход усилителя сигналов 11 соединен с входом блока 16, последний формирует сигнал управления для дифференциального усилителя 4 и далее всего первого контура управления. В блоке 16 сигнал с усилителя сигналов отфильтровывается и постоянная составляющая, пропорциональная силе , осредняется в течение 5…10 оборотов детали, запоминается и далее в ходе точения первые значения сравниваются с первоначальным для каждого прохода своим значением. С увеличением размерного износа увеличивается постоянная составляющая , а, следовательно, пропорционально растет и величина выходного сигнала блока 16. Поступая на вход дифференциального усилителя 14, она вносит коррекцию в управляющий сигнал с первичного преобразователя 2 положения инструмента в радиальном направлении по оси Y. Коррекция управляющего сигнала осуществляется всегда с одним знаком (например, плюс) и в сторону увеличения первоначального зазора D Y между первичным преобразователем 2 и задатчиком 3 глубины резания. В этом случае инструмент перемещается на деталь, компенсируя величину износа. Величина перемещения инструмента не должна превосходить линейный зазор, на котором работает первичный преобразователь 2. Ограничительным критерием износа являются автоколебания, возникающие при резании. Уровень автоколебаний устанавливается задатчиком, встроенным в блок 16. Работа двух контуров взаимосвязана через процесс резания и через каналы управления.
Дата добавления: 2015-01-18 | Просмотры: 937 | Нарушение авторских прав
1 | 2 | 3 | 4 | 5 | 6 | 7 | 8 | 9 | 10 | 11 | 12 |
|