Экспериментальное исследование повышения точности и производительности тонкостенных длинномерных деталей
В предыдущих главах подробно описаны новые методы обработки отверстий и, в частности, обработка внутренних отверстий длинномерных деталей типа "труба". Известны методы обработки с применением ультразвука и вибрационные методы, направленные на уменьшение сил резания, точности и повышения качества обработки и стойкости инструмента, уменьшение глубины деформированного слоя и повышения производительности технологического процесса в целом.
Основным недостатком известных ультразвуковых методов обработки, заключающихся в наложении ультразвуковых колебаний (УЗК) различных векторных направлений на резец, от дополнительного мощного ультразвукового источника, является необходимость дополнительных энергозатрат. Наличие сложных следящих систем автоматического управления режимом обработки ограничивает область использования УЗ методов обработки, поскольку эффективность последних зависит от поддержания оптимальной амплитуды, частоты и направления колебаний, значение которых необходимо автоматически изменять и поддерживать оптимально в зависимости от изменения нагруженности режущего клина, физико-механических и тепло-физических свойств обрабатываемого материала и материала инструмента, а также от вариации режимов обработки (частоты вращения заготовки, величины подачи и глубины резания). Указанные недостатки снижают эффективность обработки с применением УЗК, ограничивают область их применения в станкостроении и делают их практически неприемлемыми при обработке отверстий маложестких длинномерных деталей.
В этой связи основной целью настоящей работы является разработка методологии волноводной настройки параметров зоны стружкообразования и резонирующего режущего инструмента или детали, обеспечивая условия резания подобно вибрационному резанию, используя в качестве источника динамического воздействия энергию самой зоны резания, т.е. энергию переменных составляющих сил резания.
В основу разработки и функционирования предложенного метода положены изучения особенностей динамики процесса резания на основе анализа взаимосвязи вектора функции сил и движений в широком частотном диапазоне, а также изучения динамических явлений, возникающих в зоне стружкообразования, на основе анализа изменений акустотермоэлектрических параметров процесса стружкообразования.
Методика расчета сводится к определению и назначению таких режимов обработки, а также параметров инструментальной
наладки, при которых обеспечиваются условия синхронизации и усиления волновых процессов в зоне стружкообразования, а также непрерывности колебательных смещений инструмента или детали подобно вибрационному резанию, используя в качестве источника возбуждения энергию самой зоны резания.
При обработке длинномерных деталей прежде всего следует принимать меры по повышению динамической жесткости этой детали и режущего инструмента по отношению к колебательному возбуждающему воздействию, вынужденную самим процессом ламелизации в зоне стотжообразования частота которой определяется по выражению: , где - скорость резания; - ширина ламели фрагментальной стружки.
Аналогичным образом следует поступать при возможности назначения (вылета) длины обрабатываемой заготовки, равной целому числу полуволн (если заготовка консольно не защемлена).
Можно предположить еще три дополнительных условия волноводной оптимизации настройки станкоинструменталъной наладки:
- первое условие касается обеспечения (при возможности) условий синхронности (синфазности) колебательных смешений вершины инструмента и смещений заготовки с частотой вследствие упругой волны, обегающей по периметру обрабатываемое сечение заготовки в направлении, обратном ее вращению (для обрабатываемой детали с внутренним диаметром d В=40 мм, f с =12 кГц);
- второе условие определяет возможность резонансной настройки длины заготовки по крутильным колебаниям на частоте синхронизации кГц, равной шестой гармонике частоты ламелизации; 
- третье условие - это обеспечение динамической устойчивости борштанги к изгибным колебанием. Такое условие обеспечивается размещением на входе борштанги скользящих опор, выполняющих функцию квазилюнетов и устанавливаемых в расчетных местах возможных пучностей стоячей волны изгибных колебаний борштанги или обеспечивающих соотношение . При мм должно быть меньше 180 мм, т.е. 150…160 мм. В качестве таких возможностей могут применяться шаровые дорнирующие (сепараторы) обоймы, широко используемые в инструментах для комбинированной обработки с регулируемым усилием поджатия.
Применимость изложенных принципов проиллюстрируем примером практической реализации технологического процесса комбинированной обработки заготовки длиной мм из стали 45 мм и мм. Величина снимаемого припуска мм. Материал инструмента - твердый сплав T15K6 с геометрическими параметрами мм.
Обработка проводилась на модернизированном токарном станке 1К62, снабженном регулируемым тиристорным приводом и волноводным зажимным приспособлением заготовки, устройством регистрации ТЭДС ( ), величины крутящего момента и осевой составляющей силы резания , а также необходимой аппаратурой регистрации качества сформирования поверхностного слоя.
Оптимальную величину подачи и скорость резания выбирают из условий обеспечения заданного качества формирования поверхностного слоя и непрерывности возбуждения сдвиговых колебательных смещений режущего инструмента на частоте ламелизации кГц зоны стружообразования. Как показали экспериментальные данные, при получистовой и чистовой обработке максимальное значение величины подачи может быть меньше или равно величине припуска снимаемого слоя, что соответствует моменту поступления термодинамического равновесия, а, следовательно, перелому кривой зависимости при JТ = V (S р). Рис.2.44, при .
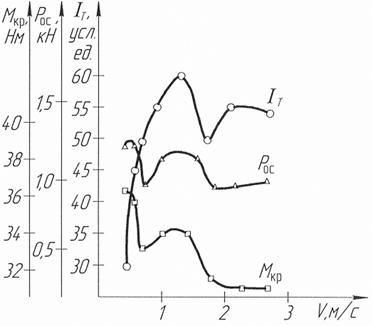
Рис.2.43. Зависимость крутящего момента Мкр, осевого усилия Рос и ТЭДС Jт от скорости резания Vр
С точки зрения получения заданного значения параметра и для финишной обработки величину подачи определяют из известного соотношения: , при мм, мкм, мм/об.
Для двухрезцозой обработки величину подачи выбирают в два раза больше, следовательно, выбирают в диапазоне 0,3…0,4 мм/об. Как показано на рис.2.44, указанному значению величины подачи мм/об при оптимальной скорости резания наблюдается перелом кривой (в виде полочки) зависимостей величины крутящего момента и осевой составляющей силы от вариации подачи.
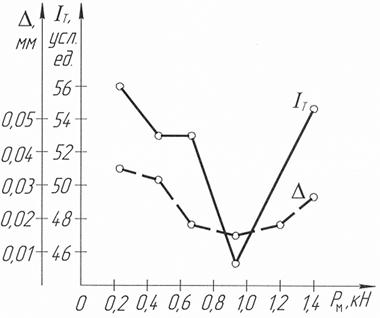
Рис.2.44. Зависимость отклонений от прямолинейности (Δ) и ТЭДС Jт от усилия Рм прижима шаров к обрабатываемой поверхности
Оптимальное значение спорости резания определяют из выражения , где - частота ламелизации в кГц, равная расчетной частоте сдвиговых колебаний борштанги, например, 2 кГц, - ширина ламели фрагментальной струнки (в мм), изменяющаяся в диапазоне от 0,6 до 0,2 мм при увеличении скорости резания от 0,3 до 3 м/с, – коэффициент усадки стружки выбирают равным 2,5. Подставляя численные значения параметров , , получим оптимальное значение скорости резания м/с, что соответствует минимальному значению параметров , , в эксперименте (рис.2.44) при вариации скорости резания и минимальному значению параметров, характеризующих качество формирования поверхностного сдоя (рис.2.45 и 2.46).
Первое же значение оптимальной скорости резания м/с соответствует наибольшей стойкости ревущего инструмента, но низкому качеству формирования поверхностного слоя (рис.2.45). При этом значение параметра (представленное в условных единицах) почти сохраняется. Точке перегиба соответствует некоторое минимальное значение параметров кН, Нм при вариации скорости резания (рис.2.43) благодаря сохранению условий.
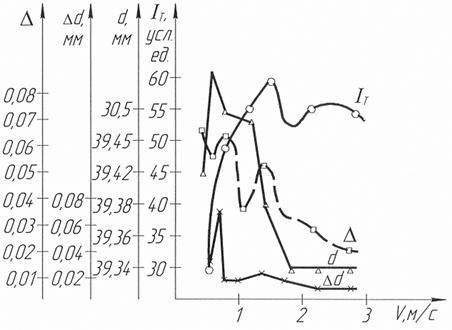
Рис.2.45. Зависимость точностных показателей (диаметра d, отклонений от круглости Δd и прямолинейности Δ, ТЭДС Jт) от скорости резания Vр
Низкое качество формирования поверхностного слоя в таком случае обусловлено тем, что на относительно низких скоростях резания преобладают динамические контактные явления в основном на задней грани режущего клина, при этом средняя температура в зоне стружкообразования далека от равновесной, а давления на поверхности сдвигов получаются настолько большими, что пластическая деформация (при относительно большой площади снимаемого слоя - 0,5 ´ 1,2 мм2) начинается ниже, у самой вершины резца, а поверхность сдвигов перемещается вниз, ближе к задней поверхности, и резец практически не касается обработанной поверхности, а, следовательно, не участвует в формировании поверхностного слоя. Такой режим используют в том случае, когда лимитирующим параметром является стойкость инструмента. Возвращаясь к анализу решила термодинамического равновесия на оптимальной скорости резания ( м/с), как наиболее рациональному режиму обработки (при тех же параметрах режущего инструмента, величины подачи мм/об и глубины резания мм), обеспечивающему заданные параметры качества формирования поверхностного слоя и заданную стойкость инструмента, определим численные значения величины крутящего момента осевой составляющей силы резания .
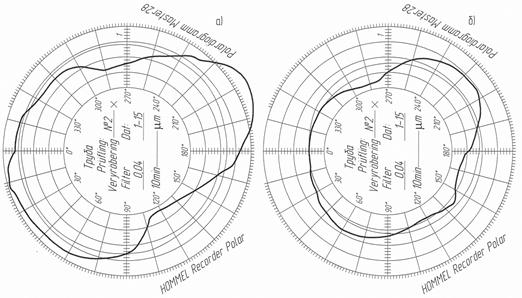
Рис.2.46. Круглограммы наружных диаметров труб до деформирования (а) и обкатанных в течение 40 мин в СЦЛ (б)
При двухрезцозой обработке (расточке) с заданными параметрами режущих клиньев ( при наличии калибрующей ленточки длиной мм) в создании величины крутящего момента участвуют силы резания и силы трения по задней грани и калибрующей ленточке за счет упругого восстановления материала от составляющей силы резания , т.е. , где - диаметр обрабатываемого отверстия в метрах.
Согласно классическому представлению теории резания действия сил по передней и задней поверхности инструмента, составляющая силы трения , с учетом среднего значения динамического коэффициента трения и значения, переднего угла определяется из выражения . Численное значение составляющей силы резания определяется соотношением . Полученное расчетное значение , с достаточно высокой степенью точности совпадает с экспериментальными данными, полученными на оптимальных режимах обработки при обеспечении условий полноводной настройки параметров упругой системы и зоны стружкообразования. При обеспечении условий волноводной оптимизации технологической наладки сила резания не зависит от скорости резания и определяется только площадью срезаемого слоя (а ´ в) и влиянием температурных эффектов, сопровождающих процесс механической обработки подобно вибрационному резанию. Учитывая, что при двухрезцовой обработке составляющие силы резания , то результирующий вектор силы резания расположен в плоскости ZOY перпендикулярно к лезвию режущего инструмента. В таком случае изменение главного угла в плане вследствие изменения положения главного лезвия относительно направления подачи значительно влияет на величину соотношений осевой и тангенциальной силы.
При значительном уменьшении скорости резания, например, до 0,5 м/с (рис.2.44) значение величины крутящего момента и осевой составляющей силы резания увеличивается в 1,2 раза. Указанное увеличение обусловлено уменьшением влияния температуры на силовую нагруженность режущих клиньев. Такое же увеличение и наблюдается и на оптимальной скорости резания м/с. При вариации любых параметров, приводящих к нарушению условий волноводной настройки, а, следовательно, к уменьшению термодинамических эффектов, связанных с импульсным локальным тепловым воздействием в зоне сдвига и стружкообразования в целом.
Если на оптимальных режимах обработки и уменьшаются в 1,2 раза, то параметры, определяющие точностные характеристики, и параметры шероховатости улучшаются в 7 … 8 раз (рис.2.33 … 2.36).
Приведенный экстремальный характер изменения контролируемых параметров при нарушении условий волноводной настройки объясняется изменением не только за счет импульсных тепловых воздействий, но и изменением величины локальные зон пластической деформации, скорость, пластического течения, т.е. нарушаются условия квазихрупкого разрушения материала в условной скорости сдвига.
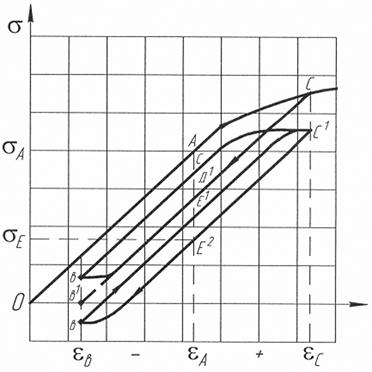
Рис.2.47. Диаграмма напряжений при циклических нагрузках
Разработанная технология изготовления длинномерных деталей включает в себя и мехобработку длинных труб, диаметром 30…110 мм, длиной (1…3) × 103 мм. На первой операции - черновая проточка, труба устанавливается на токарном станке в гидравлических самоцентрирующих люнетах - СЦЛ (как и в случае точения валов) и вращается в зажимных роликах на протяжении всего прохода по наружной или внутренней поверхности. С целью установления влияния усилия зажима трубы СЦЛ на геометрическую точность в поперечном сечении был проведен эксперимент, суть которого заключалась в том, что дискретно менялось усилие зажима в СЦЛ (200 и 300 н/мм2) и время деформации (20 и 40 мин). Наружный диаметр труб 34 ± 0,4 мм, толщина 2 мм. Материал сталь 45 и 12Х18Н10Г, в поставке. Мехобработка не проводилась. Наиболее характерные круглограммы представлены на рис.2.48, а, б.
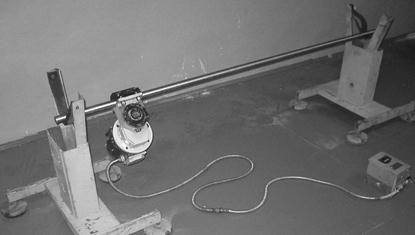
Рис.2.48. Установка для обработки изгибными колебаниями
На рис.2.48, а профиль наружного диаметра до деформирования, а на рис.2.48, б после 40 минутной обкатки. Анализ экстремальных данных показывает правильность теоретических предпосылок проведенных в главах 2 и 3, использование СЦЛ повышает геометрическую точность в 1,8…2,5 раза в зависимости от физмехсвойств материала и его первоначального профиля.
Дата добавления: 2015-01-18 | Просмотры: 953 | Нарушение авторских прав
1 | 2 | 3 | 4 | 5 | 6 | 7 | 8 | 9 | 10 | 11 | 12 |
|