АкушерствоАнатомияАнестезиологияВакцинопрофилактикаВалеологияВетеринарияГигиенаЗаболеванияИммунологияКардиологияНеврологияНефрологияОнкологияОториноларингологияОфтальмологияПаразитологияПедиатрияПервая помощьПсихиатрияПульмонологияРеанимацияРевматологияСтоматологияТерапияТоксикологияТравматологияУрологияФармакологияФармацевтикаФизиотерапияФтизиатрияХирургияЭндокринологияЭпидемиология
|
Длинномерных тонкостенных деталей
Для обработки тонкостенных деталей разработаны способы поднастройки системы СПИЗ, которые расширяют технологические возможности известных решений, т.к. позволяют осуществлять обработку внутренних поверхностей тонкостенных пустотелых деталей, обеспечить повышение точности поднастройки и виброустойчивости системы СПИЗ, а тем самым и точность обработки, так как увеличением вязкости и жесткости ферромагнитной жидкости увеличивают жесткость детали, уменьшают амплитуду колебаний деталь-резец, при этом также уменьшается износ. Кроме того, корректирующее воздействие осуществляют на упругую систему СПИЗ, что упрощает процесс поднастройки. Применение предложенных способов поднастройки системы СПИЗ при обработке тонкостенных деталей, например втулок, позволяет минимизировать уровень вибраций при резании (вынужденных и автоколебаний) за счет регулирования жесткости системы СПИЗ.
Для получения деталей с заданной точностью и качеством необходимы дополнительные методы и средства воздействия на условии протекания реальных технологических процессов. Наиболее широкое распространение получили известные ультразвуковые методы обработки, направленные на уменьшение сил резания, повышения качества обработки и стойкости инструмента, уменьшение глубины деформированного слоя и повышения производительности технологического процесса в целом. Основными недостатками известных ультразвуковых методов обработки, заключающихся в наложении ультразвуковых колебаний (УЗК) на резец, от оптимальной амплитуды, частоты и вида колебаний, значение которых необходимо изменять в зависимости от изменения физико-механических и теплофизических свойств обрабатываемого материала и материала инструмента, от вариации режимов обработки - частоты вращения заготовки, величины подачи и глубины резания. Указанные недостатки снижают эффективность обработки с УЗК, ограничивают область их применения в станкостроении.
Идея предлагаемого метода в снижении трудоемкости, расширении технологических возможностей и области его применения за счет автоматической оптимизации процесса резания, получения деталей с заданной точностью и качеством формирования поверхностного слоя и уменьшение энергоемкости процесса резания в целом.
Автоматическая оптимизация процесса резания при чистовой и получистовой механической обработке, заключается в выборе оптимальных технологических параметров, которые определяются в зависимости от варьирования технологического параметра. Для исходного физического параметра выбирают минимум энергоемкости процесса ( ) и колебательную скорость режущего клина, здесь - амплитуда колебаний режущего инструмента. Выбор оптимальных технологических параметров (скорости резания подачи глубины резания геометрических параметров углов резания ) определяют из условия равенства колебательной скорости режущего клина и скорости стружки (т.е. = ) при исключении условий возбуждения энергии ультразвуковых колебаний от внешнего источника. При этом на режущем инструменте возбуждают ультразвуковые колебания в направлении - скорости резания, а в качестве энергии возбуждения усилия и синхронизации комплексных ультразвуковых колебательных смещений ультразвуковых колебаний с преобладанием крутильной составляющей, совпадающей с направлением скорости резания. Для продольных составляющих в направлении скорости подачи, используют саму энергию зоны резания. Частоту возбуждения комплексных ультразвуковых колебаний выбирают равной, в ультразвуковом диапазоне, наибольшей по энергоемкости частотой составляющей спектра периодизированных релаксационных импульсов динамической составляющей силы стружкообразования при разрушении материала. В основу разработки и функционирования предложенного метода положено изучение особенностей динамики процесса резания на основе анализа взаимосвязи вектора функции сил и движений в широком частотном диапазоне, а также изучение динамических явлений, возникающих в зоне стружкообразования, на основе анализа изменений акусто-термоэлектрических параметров процесса стружкообразования. Кроме этого используются особенности исследований динамических явлений в зоне резания при высокочастотных вибрационных методах обработки, приводящих к вибрационной линеаризации низкочастотных вибраций в направлении действия и существенному уменьшению составляющих сил резания, а, следовательно, уменьшению общей энергоемкости процесса разрушения в целом и как следствие - улучшению качества формирования поверхностного слоя; повышения точности обработки за счет локализации зон пластического деформирования и повышения динамической жесткости обрабатываемых маложестких деталей и эффекту заострения режущего инструмента при условии значительного снижения температуры в зоне резания. При этом особое внимание акцентировалось на изыскании новых методов высокочастотного вибрационного резания, используя в качестве энергии возбуждения высокочастотных колебаний режущего клина саму энергию зоны резания, т.е. энергию спектра переменной составляющей силы резания , учитывая, что общая сила резания
. (2.43)
Наличие переменной составляющей силы резания - , обусловлено импульсными релаксационными процессами разрушения в зоне стружкообразования, а также за счет изменения жесткости резания , что приводит к перемещению одного из элементов замкнутой технологической системы непосредственно в ходе обработки, как правило, инструмента.
Согласно выражению (2.43) при условии гармоничного возбуждения высокочастотных колебаний инструмента в направлении скорости резания , составляющая силы резания будет равна:
, (2.44)
где - круговая частота режущего клина инструмента, а - собственная частота комплексных колебаний инструмента, j - фазовый угол сдвига.
Закон изменения перемещения детали во времени имеет вид:
, (2.45)
где - коэффициент, характеризующий фиктивную жесткость технологической системы, под действием установившихся высокочастотных колебаний режущего клина, влияющих на время контакта ( ) инструмента со стружкой (т.е. время резания) в течение одного цикла (периода l) колебаний инструмента , где - коэффициент жесткости детали, тогда уравнение (2.45), отображающее закон изменения смещения заготовки во времени под действием составляющих сил, имеет вид:
. (2.46)
Анализ слагаемых в выражении (2.46) показывает, что первое слагаемое представляет собой статическую составляющую силы резания, а второе - динамическую силы резания, вызывающие в общем виде сложное перемещение обрабатываемой детали, причем составляющие сил резания, а, следовательно, смещения уменьшаются с уменьшением отношения . Следовательно, чем меньше время контакта ( ) и чем выше частота ( ) возбуждения комплексных колебаний с преобладанием крутильной составляющей ( ), тем меньше составляющие сил резания в процессе вибрационной обработки и выше точность и качество выпускаемых изделий.
Если глубину резания и скорость резания выбрать в процессе технологической наладки таким образом, чтобы условия самовозбуждения колебаний поддерживались устойчивыми при , а время контакта (время резания) будет сохраняться только в течение периода колебаний, то выражение (2.25) примет вид:
. (2.47)
Согласно полученного выражения (2.47) можно сделать следующие важные для реализации выводы:
1. Для уменьшения динамических составляющих сил резания и , приводящих соответственно к уменьшению изменения параметров и , возбуждение или усиление и синхронизацию высокочастотных колебаний смещений режущего клина инструмента, необходимо производить в направлении скорости резания , (в ортогональном направлении), при котором j = 900.
2. При установившемся вибрационном режиме резания (т.е. при условии возбуждения установившихся колебаний в направлении скорости резания) низкочастотные колебательные смещения линеаризируются в ортогональных направлениях, исключая изменение глубины резания и величины подачи, т.е. наблюдается механизм резания, при котором и , а следовательно параметр шероховатости также стремится к нулю. В таком режиме, шероховатость обработанной поверхности ( ) получают близкой к расчетной.
3. Обеспечиваются условия технологической наладки, путем варьирования параметрами и при постоянных значениях величины подачи и радиуса закругления ширины резца, а также углов заточки инструмента, выбранных оптимальными с точки зрения получения заданной шероховатости и условиями обеспечения установившимися высокочастотными комплексными ультразвуковыми колебаниями режущего клина, когда величина динамической составляющей силы резания в направлении и , а статическая составляющая уменьшится в 3…4 раза.
4. Уменьшение составляющих сил резания при приводит к резкому снижению сопротивления резания и коэффициента трения по передней поверхности, а, следовательно, к резкому уменьшению температуры в зоне резания.
5. Чем больше величина амплитуды крутильных колебаний инструмента и их мощность, тем больше величины припуска можно снимать за один проход при обеспечении условия контакта . При этом на величину основное влияние при финишных методах обработки оказывает скорость резания . Критическую скорость резания выбирают из условия , при = 0,025 мм, = 9,600 Гц, = 1,507 м/с, при = 0,005 мм, = 9,600 Гц, = 0,3 м/с.
6. Согласно выражения (2.47) ультразвуковые колебания фиктивно увеличивают жесткость технологической системы и величину переднего угла в раз. При принятых условиях вибрационной обработки фиктивная жесткость увеличивается в 4 раза больше фактической.
На основании приведенного теоретического обоснования и выводов возбуждение (синхронизацию и усилие) высокочастотных колебательных смещений согласно выражения (2.46) осуществляют в направлении скорости резания (т.е. в направлении Z - ортогональном направлении X и Y), при котором сдвиг фаз равен 90°, а в качестве исходного физического параметра выбирают минимальное значение силы резания, величины крутящего момента осевого усилия согласно выражения (2.47) и максимальное значение колебательной скорости режущего клина , сопровождающаяся значительным возрастанием уровня высокочастотных колебательных смещений с противоположной стороны инструмента - борштанги 2.
В процессе обработки детали 1 (рис.2.47, а) режущим инструментом 2, синхронизацию и усилие высокочастотных комплексных колебательных смещений режущих клиньев пластины 4, осуществляют с помощью волноводного преобразователя и резонансной настройки всей волноводной борштанги 2, закрепленной в узловых точках 5 к суппорту 6. Изменение режимов обработки, величины подачи инструмента 2 и частоту вращения (шпинделя) детали 1 автоматически плавно изменяют с помощью раздельных регулируемых приводов (подачи, состоящего из блоков 7 … 10, и главного движения, состоящего из блоков 11 … 14).
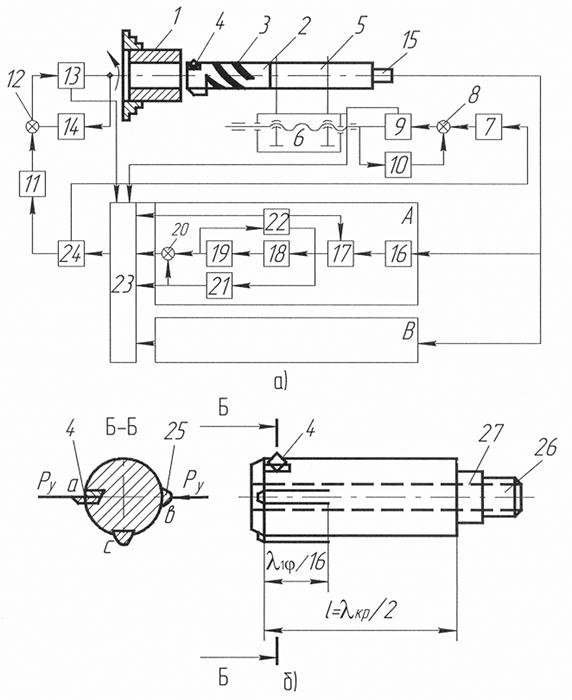
Рис.2.26. Система автоматической оптимизации процесса резания: а – функциональная схема управления; б – конструкция расточной головки волноводной борштанги
При этом регистрацию колебательной скорости инструмента 2 осуществляют с помощью преобразователя 15 регистрации комплексных ультразвуковых колебаний, установленного со стороны свободного полуволноводного конца борштанги 2. Формирование диагностических признаков и управляющих сигналов регулируемыми приводами и технологическим процессом в целом осуществляют с помощью двух идентичных избирательных каналов А и В, включающих в себя блоки 16 … 24.
Наряду с усилением и синхронизацией колебательных смещений, волноводный резонатор-преобразователь преобразовывает продольные колебания в комплексные с преобладанием крутильной компоненты с помощью двух наклонных винтовых канавок 3 волноводной длины ( , где ), с переменным шагом, уменьшающимся в сторону узла крепления режущего клина пластинки 4, и равноудаленных друг от друга идентеров 15. На рис.2.48, б приведена конструкция расточной головки волноводной борштанги, а на рис.2.48, а, б показаны зоны крепления и формы колебаний борштанги при резании. На рис.2.48, в приведен пример развертки для технологического изготовления наклонных винтовых канавок волноводного резонатора-преобразователя, где величину радиуса выбирают равной половине длины волн крутильных колебаний борштанги 2, а волноводную длину L развертки пазов 3 выбирают равной , где , , - скорость звука в материале борштанги 2 для продольных волн, - собственная частота резонатора-преобразователя.
Учитывая, что , например, для стали , для единой частоты усиления , , изготовление наклонных винтовых канавок с переменным шагом с общей длиной позволяет на полуволноводной длине сдвиговых колебаний произвести их согласование.
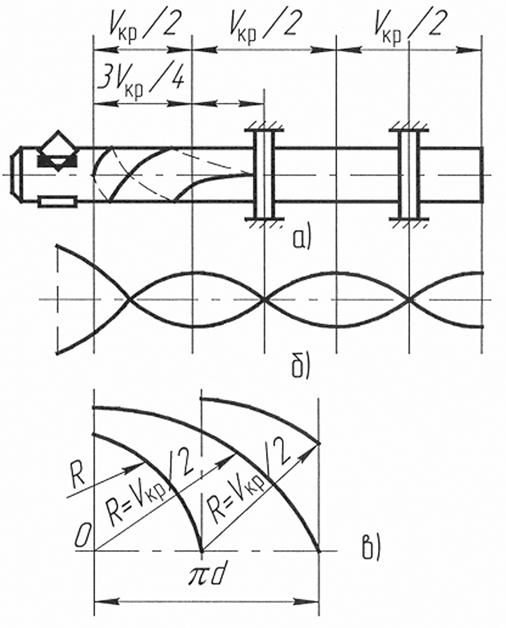
Рис.2.27. Схема расположения узлов и пучностей на инструменте:
а – схема закрепления; б – формы колебаний борштанги;
в – развертка пазов волновода
Одновременно, наличие винтовых канавок с переменным шагом, уменьшающимся к зоне резания, позволяет не только усиливать и преобразовывать продольные колебательные смещения в колебательные смещения разных векторных направлений, но и производить с большим быстродействием автоматическую адаптацию режущих клиньев инструмента 4, изменяющимся условиям их силовой нагруженности в зоне резания. Указанная высокоскоростная цилиндрическая адаптация возможна благодаря упругой податливости рабочей части инструмента на закручивание и сжатие волноводного преобразователя 2. Автоматическую адаптацию на изменение среднеинтегральной нагруженности режущего инструмента, осуществляют с помощью регулируемых приводов подачи и главного движения, управляемых избирательными диагностическими каналами А и В реле-регулятором многовходового регистратора 24. Стабилизацию минимального значения величины крутящего момента или осевой составляющей силы резания ( ), например, при увеличении износа осуществляют путем переключения блока 24 рода работ, соединяющего управляющие входы задатчиков 7 и 11 с выходом многовходового регистора 23, изменяющего скорость резания или скорость подачи функции приращения управляющих сигналов, сформированных со стороны реакции электрической части приводов 9 и 13, а также в функции приращения величины износа, регистрируемого вторым диагностическим каналом В или в функции уменьшения выходного сигнала канала А, функционально связанного с уменьшением эффективности самовозбуждения волноводного преобразователя 2, т. е. с его значительным демпфированием.
Настройку на наиболее информативные частоты спектра колебательных смещений инструмента, связанные с износом режущего инструмента, качеством формообразования поверхности обрабатываемой детали, а также амплитудного значения циклической нагруженности и колебательной скорости режущих клиньев инструмента, осуществляют в каждом канале в процессе самообучения при контрольной обработке с помощью системы 22 автоматической настройки фильтра 17 и задатчика 21 по максимальному значению выходного сигнала, снимаемого с выхода блока усреднения (интегратора) 19.
Регистрацию текущего значения контролируемых параметров на выходе блоков 9, 13 и блоков 19 в каждом канале, их допустимого значения на выходе блоков 21, а также разностного сигнала на выходе схемы сравнения 20 в канале А и В, осуществляют с помощью многовходового регистратора 23, подключенного к выходам указанных блоков.
Многопараметрическая диагностика и своевременное автоматическое управление процессом механической обработки, позволяют значительно повысить точность и качество выпускаемых изделий, а также производительность в целом. В свою очередь, использование волноводной силовой головки позволяет совместно с волноводным резонатором-преобразователем борштангой 2 наряду с обработкой резанием осуществлять поверхностно-пластическое деформирование (ППД), производить исправление оси заготовки за счет дополнительного введения пластин 25 твердого сплава длиной , образующие совместно с режущими клином пластины 4 и равнобедренный уравновешенный силовой треугольник. Крепление силовой головки к волноводному преобразователю 2 осуществляют с помощью резьбового соединения 26 и цилиндрической посадочной шейкой 27, которая обеспечивает надежный акустический контакт для передачи комплексных колебаний с преобладанием крутильной составляющей. В этой связи общую длину силовой головки выбирают равной полуволноводной длине крутильной компоненты . Поскольку для продольной составляющей компоненты колебаний при длине , силовая головка вносит значительное эквивалентное (жесткостное) сопротивление, то конструктивно твердосплавные пластинки 25 устанавливают непосредственно у начала канавок волноводного преобразователя борштанги 2, вблизи источника возбуждения и преобразования, что значительно уменьшает вносимое рассогласование.
Возбуждение с помощью механического волноводного резонатора-преобразователя комплексных ультразвуковых колебаний с преобладанием крутильной составляющей, позволяет производить высококачественную адаптацию режущего клина в направлении вращения (скорости резания) и в направлении продольной подачи. Преобладание крутильной составляющей над продольной составляющей высокочастотных колебаний, диктуется несоизмеримым соотношением скорости резания и скорости подачи в процессе механической обработки.
Дата добавления: 2015-01-18 | Просмотры: 1313 | Нарушение авторских прав
1 | 2 | 3 | 4 | 5 | 6 | 7 | 8 | 9 | 10 | 11 | 12 |
|