АкушерствоАнатомияАнестезиологияВакцинопрофилактикаВалеологияВетеринарияГигиенаЗаболеванияИммунологияКардиологияНеврологияНефрологияОнкологияОториноларингологияОфтальмологияПаразитологияПедиатрияПервая помощьПсихиатрияПульмонологияРеанимацияРевматологияСтоматологияТерапияТоксикологияТравматологияУрологияФармакологияФармацевтикаФизиотерапияФтизиатрияХирургияЭндокринологияЭпидемиология
|
Система автоматического управления обработки длинномерных осесимметричных деталей
Рассмотренные САУ обработки стабилизировали ось обрабатываемой детали в зоне резания: длинномерные детали, когда отношения , указанными способами обрабатывать невозможно. Для обработки длинномерных валов разработан способ точения, при котором обрабатываемый вал имел равножесткость по всей длине. На рис.2.24 изображена функциональная система, иллюстрирующая новый способ мехобработки, при котором снимают информацию о точностных параметрах обрабатываемой детали в продольном и поперечном направлениях и об уровне вибрации при резании с помощью датчиков 1, 10.
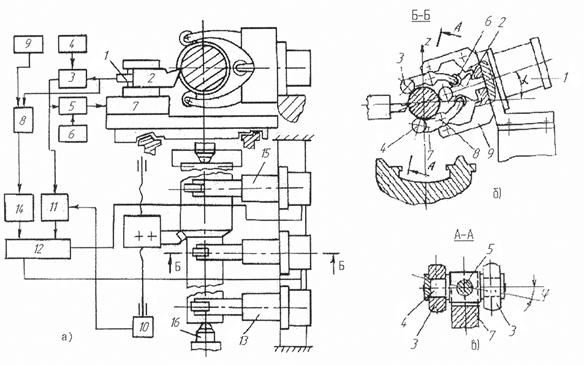
Рис.2.24. САУ обработки длинномерных заготовок
При этом, используя совокупность одновременной работы двух контуров управления, исключают отрицательное влияние динамической податливости нежесткой детали в процессе ее обработки. Для чего в процессе резания регистрируют выходной сигнал датчика 1, жестко закрепленного на резце 2 и работающего на ультразвуковом принципе и выдающего информацию о текущем значении диаметра детали в плоскости, проходящей через вершину резца по нормали к обработанной поверхности детали на блок измерения диаметра 3, где текущее значение диаметра сравнивают с задающим от задатчика 4 диаметром детали, а сигнал рассогласования подают на вход блока управления 5 положением резца для компенсации погрешности обработки, где происходит сравнение сигналов задатчика 6 положения резца и блока измерения диаметра 3, и вырабатывается сигнал управления на электрогидропривод 7. С помощью последнего и управляют положением, на котором закреплен резец 2. В случае изменения величины диаметров в плюс или минус от наперед заданного значения задатчиком положения вершины резца, также управляют по оси Y с учетом знака рассогласования сигнала управления.
Изменение диаметра обрабатываемой детали непрерывно измеряют в процессе резания и управляют положением вершины резца в функции сформированного сигнала блоком 8 с учетом знака рассогласования, что позволяет стабилизировать поперечный размер детали. С целью минимизации уровня вибраций и стабилизации оси детали, на блок 8 управления, второго контура управления демпфированием, подают выходной сигнал с датчика 1 и задатчика 9 и определяют величину уровня вибраций детали, сравнивают ее с допустимой величиной с помощью блока 8. Затем формируют сигнал управления демпфированием с помощью блока 14, который через коммутатор 12 управляет люнетами демпфирования 15. Одновременно с учетом величины сигнала датчика 10, указывающего о месте нахождения резца вдоль детали, формируют сигнал блоком 11 управления равножесткостью, который через коммутатор 12 управляет гидролюнетом жесткости 13. Количество люнетов расстанавливают по длине обработки из условия равножесткости в функции соотношений длин и диаметров детали или устанавливают люнеты в зонах пучностей распределения высших основных форм колебания детали. Самоцентрирующие гидролюнеты (СГЛ) 13 устанавливают после зоны обработки относительно обработанной поверхности, которые работают как равножесткие опоры. При этом, давление, подводимое к СЦЛ 13, обеспечивающих зажим детали, подают максимальное из условия предельного пластического деформирования поверхностного слоя обрабатываемой детали, а на управляемых СЦЛ 15, устанавливаемых относительно необработанной на данном проходе поверхности и работающих в режиме демпфера, создают давление, обеспечивающее гашение (демпфирование) вибраций. Причем, по ходу передвижения резца вдоль детали, переключение СГЛ демпфирования 15, работающих в режиме демпферов, на режим равножестких опор (люнетов 13), производят с помощью коммутатора 12 в функции пути, пройденного резцом 2, регистрируемого датчиком 10. В исходном состоянии, перед процессом резания все гидролюнеты 13 и 15 работают в режиме демпферов, кроме (работающих в режиме равножесткости), установленных у передней и задней бабок. Это условие выполняют с целью центрирования оси относительно оси центров станка, а опорные поверхности детали в местах установки крайних люнетов предварительно протачивают. При этом торцы обрабатываемой детали выполняют плоскими, без центровочных отверстий, что позволяет установленную деталь в люнетах не поджимать задним центром (у задней бабки) по оси детали, а также зажимать в патроне или устанавливать в жесткий центр у передней бабки. Традиционный способ крепления детали приводит к искривлению оси последней и возникновению остаточных напряжений в материале, которое усиливается под действием пластического деформирования во время обработки материала. К торцам детали подводят опоры 16 для предотвращения перемещения детали вдоль оси. Причем, рабочий орган последних выполняют шарообразным с целью исключения радиального микроперемещения детали и создания неопределенного направления реакции в шаровых опорах. Опоры 16 контактируют с обработанными торцами детали без предварительных осевых сил сжатия, что позволяет разомкнуть силовой контур системы СПИЗ по оси детали и в то же время создать ограничения перемещения детали в осевом направлении.
Это позволяет базировать деталь по образующей поверхности детали, которая совпадает с измеряемой поверхностью, что приводит к увеличению точности обработки и исключению технологической наследственности от условий крепления.
Рациональное место расположения жесткие опор и опор-демпферов приводит к распределению добротности взаимосвязанных механических контуров, а следовательно, к улучшению диссипативных свойств контакта инструмент-деталь в зоне резания, последнее уменьшает циклическую нагруженность режущего клина, вызванную быстрыми и медленными движениями, улучшает качество формообразования обрабатываемых поверхностей. Таким образом, использование способа позволяет наряду с повышением точностных показателей обработки, повысить эксплуатационные характеристики обрабатываемой детали, снизить напряжение в готовых деталях, повысить динамическую устойчивость протекания технологического процесса в целом.
САУ (рис.2.24) оснащены самоцентрирующими люнетами, позволяющим центрировать деталь в процессе обработки. Исполнительный механизм СЦЛ (рис.2.24, б) при резании работает следующим образом: при подаче рабочей силы в привод 1, плоский копир 2, соединенный со шток-поршнем привода 1, перемещается на деталь, а рабочие ролики, последние выполнены сдвоенными со сферическими опорными поверхностями и имеют две степени свободы вращения, относительно собственной оси 4 и оси поворота 5, зажимают или разжимают деталь посредством контакта роликов слежения 6 по рабочей поверхности плоского копира 2.
Рабочая поверхность копира 2 выполнена по кривой, близкой к радиусу, и рассчитывается в зависимости от диапазона диаметров обрабатываемой детали. Одна пара рабочих роликов 3 вместе с осями 4 и 5 расположена на корпусе плоского копира 2, а две другие пары роликов 3 закреплены на рычагах 7. Поворот рычагов 7, на концах которых расположены рабочие ролики 3 и ролики скольжения 6, происходит относительно оси вращения 8, последняя закреплена на корпусе люнета 9. Зажим детали рабочими роликами 3 осуществляется по жесткой программе от копира 2. Силовое замыкание роликов про исходит с усилением, пропорциональном силе, развиваемой приводом 1. С целью разгрузки роликов 3 и рычагов 7, а также повышения динамических характеристик системы СПИЗ продольная ось корпуса люнета 9, вместе с приводом 1 повернута на угол a, который рассчитывается в функции геометрических параметров резца и обрабатываемой детали.
При снятии резцом (рис.2.24, б) в зоне контактов роликов 3 с деталью их линейный контакт изменяется, а при проходе резца через первые сдвоенные пары рабочих роликов 3, ось вращения 4 поворачивается относительно оси 5 на угол j, который изменяется в процессе съема металла. Численное значение угла оси вращения изменяется функции глубины резания и угла резания в плане. После прохода резца вторых сдвоенных пар рабочих роликов 3 ось вращения 4 возвращается в исходное положение. Плавный переход роликов с необработанной на данном проходе поверхности и обработанной на данном проходе поверхности, включал переходную поверхность, образующуюся в процессе съема металла, осуществляется за счет сферического профиля сдвоенных роликов и постоянства уравновешивающих моментов.
Одной из ключевой задач разработки САУ является создание диагностических каналов, выявление диагностических признаков в объекте, для данной работы - это изменение основных параметров, характеризующих состояние и условия протекания процесса резания непосредственно в ходе обработки. Разработан новый метод автоматической диагностики условий протекания процесса резания. Высокочастотные ультразвуковые зондирующие волны: возбуждают пьезоэлектрическим преобразователем на рабочей части инструмента в направлении подачи в пределах критического угла a1 = 30…450 (например a1 = 360) по отношению к нормали, проведенной в плоскости резания для режущих инструментов с пластинками твердого сплава или по отношению к перпендикуляру, проведенному к образующей обрабатываемой детали через вершину резца для режущих инструментов со сменными (трехгранными, четырехгранными и др.) пластинами.
Как показали первые эксперименты по мехобработке с применением САУ, точность детали, полученная на станке не сохраняется в связи с проявлением релаксационных процессов в течении первых 2…3 часов после обработки. С целью снижения уровня короблений - сохранения эксплуатационной точности был предложен новый метод обработки, суть которого - исключение влияния технологической наследственности, полученной на предыдущих операциях и проходах.
Согласно предложенному способу механической обработки нежестких деталей базирование последних осуществляют в соосно расположенных по длине детали самоцентрирующихся гидравлических люнетах - СЦЛ 1, причем перед началом обработки измеряют упругие реакции детали в СЦЛ 1 и устанавливают в них усилие зажима детали на 10 % превышающим максимальную величину измеренных реакций.
Затем в процессе обработки изменяют величину подачи из условия сохранения постоянной разницы между радиальной составляющей силы резания и величиной измеренных упругих реакций заготовки.
Особую трудность при мехобработке вызывают заготовки особо длинные, когда соотношение длин к их диаметру равно или больше ста. Тогда САУ процессом обработки реализуется следующим образом. Предварительно, в зависимости от длины обрабатываемой детали, заднюю бабку станка устанавливают в требуемое положение на станине станка. Затем по обе стороны с противоположных сторон суппортов по длине заготовки устанавливают самоцентрирующиеся гидравлические люнеты СЦЛ для стабилизации оси по длине заготовки. Причем, расстояние между опорами выбирают из соотношения , обеспечивая условие равножесткости по всей длине заготовки. Деталь закрепляют в зажимных патронах 2 и 4 соответственно передней и задней бабок. Резцы соответственно устанавливают в резцедержателях суппортов подводят в начале и в конце заготовки и настраивают на необходимый размер. Включают привод главного движения и приводят деталь во вращение.
Двухрезцовый способ обработки с применением САУ позволяет уменьшить время обработки заготовки как минимум в два раза, увеличить производительность, получить при этом деталь с заданными технологическими параметрами и точностными характеристиками, за счет оптимизации сил резания и поддерживания предельного упругого состояния поверхностного слоя по всей длине заготовки.
Теоретические исследования показали, что для длинномерных заготовок необходимо управлять осевой силой. В противном случае возникает дополнительный изгибающий момент и точность резко падает. Для устранения влияния осевой силы на процесс формирования геометрии детали была разработана САУ (рис.2.25) управления осевой силой сжатия.
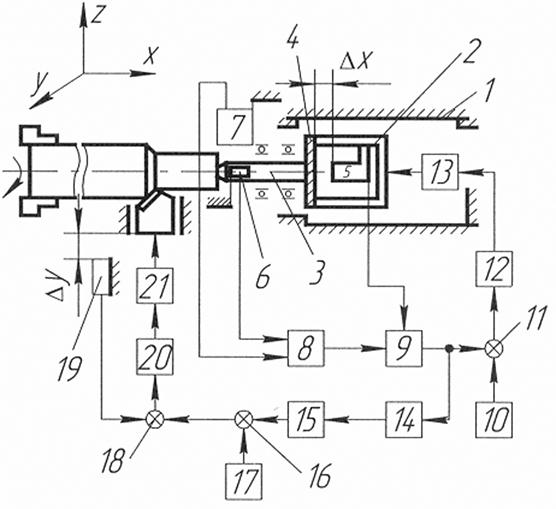
Рис.2.25. САУ осевыми усилиями
САУ точностью механической обработки длинномерных деталей осуществляется следующим образом: заготовку зажимают в патроне и поднимают задним динамометрическим узлом 2 с вмонтированном в него динамометрическим центром 3, один конец которого упирается в заготовку, а другой в упругий элемент 4, его перемещение по оси X контролируется первым первичным преобразователем малых перемещений 5, последний жестко закреплен на корпусе динамометрического заднего центра относительно упругого элемента 4 с начальным зазором D X. При удлинении заготовки за счет температурного расширения от процесса резания динамометрический центр перемещается по оси X и деформирует упругий элемент 4, его деформация протарированная, через свои физико-механические характеристики диагностирует осевое напряжение в заготовке в процессе резания. Деформация упругого элемента регистрирует первым первичным преобразователем 5.
Принцип формирования полезного сигнала для подавления мешающих факторов, обусловленных температурно-силовыми деформациями вращающегося центра в плоскости YOZ, осуществляют путем регистрации статических и динамических составляющих деформаций соответственно первичным преобразователями вторым 6 и третьим 7, и дифференциальным усилителем 8, с помощью выходного сигнала которого измеряют коэффициент передачи первого масштабного усилителя 9 в функции изменения статической и динамической податливости заднего динамометрического центра 3 в указанной системе координат. Регистрируемые и преобразованные в электрические сигналы температурные деформации в направлении оси X первым первичным преобразователем 5, подают на первый масштабный усилитель 9, в котором и происходит нормирование выходного сигнала первичного преобразователя 5, путем изменения его коэффициента передачи, таким образом, сигнал на выходе первого масштабного усилителя 9, функционально связанного с осевыми температурными деформациями заготовки, управляет величиной осевой силы поджатия заготовки в заданном диапазоне от задатчика осевых деформаций 10, т.е. заданное осевое усилие поджатия задним центром сохраняется в течение всего процесса обработки независимо от геометрических параметров заготовки и температурных режимов обработки. Заготовка, удлиняясь дополнительно, не нагружается осевой внешней силой температурного расширения. Сигнал с задатчика 10 и блока 9, сравниваясь в первой схеме сравнения 11, и разностный сигнал, пропорциональный сигналу управления, поступает на усилитель мощности 12 и далее на электрогидравлический привод 13, последний перемещает динамометрический задний центр 2 относительно задней бабки 1 на величину, пропорциональную деформации заготовки от температурного удлинения, поддерживая тем самым заданное задатчиком 10 усилие осевого прижатия заготовки. Одновременно в функции сформированного сигнала управления, снимаемого с выхода первого масштабного усилителя 9, корректируют величину глубины резания с учетом температурных деформаций заготовки путем воздействия-изменения заданного напряжения на выходе задатчика 17, привода коррекции глубины резания, через последовательно соединенные второй масштабный усилитель 14, блок типа "зона нечувствительности" 15, старой схемы сравнения 16. Причем величину корректирующего сигнала управления в процессе настройки устройства, реализующего способ, осуществляют путем изменения коэффициента передачи второго масштабного усилителя 14, а величину зоны нечувствительности блока 8 выбирают такой, чтобы сигнал управления на его выходе появился только после того, как температура заготовки непосредственно в ходе обработки повысится на 15…20°С относительно температуры окружающей среды. Далее сигнал управления - коррекции вершины резца с учетом температурного расширения заготовки с выхода второй схемы сравнения 16, поступает на вход третьего схемы сравнения 18, где сравнивается с сигналом обратной связи по положению резца от четвертого первичного преобразователя 19, установленного на суппорте станка и разностный сигнал с выхода схемы сравнения 18 поступает на вход второго усилителя мощности 20, а выход последнего подключен к выходу электрогидропривода 21.
Обеспечение указанных условий с учетом стабилизации осевых деформаций силового контура задней бабки и коррекции глубины резания позволяет стабилизировать глубину напряжения - деформированного состояния поверхностного слоя, получить детали с заданной точностью обработки с учетом влияния температурных деформаций за счет компенсации последних при точении, шлифовании, фрезеровании и т.д.
Для маложестких деталей, диаметры которых не превышают 10 мм, а отношение длины к диаметру больше 10, целесообразно, как показали эксперименты, в процессе резания прикладывать осевую растягивающую силу. Последнее позволяет сократить упругие прогибы детали и не подвергать последнюю перегрузкам.
При растяжении собственная частота детали растет на 10…20%, т.е. происходит смещение спектра частот в сторону их возрастания и одновременно уменьшаются амплитуды колебаний по соответствующим формам.
Импульсное приложение растягивающей силы приводит к уменьшению величины силы растяжения в 6…8 раз. Кратность частот импульсов растягивающей силы частоте вращения детали позволяет получить резонансный режим работы. Использование переменной составляющей термо-ЭДС в качестве датчика амплитуды относительных колебаний позволяет измерять их в труднодоступных зонах обработки (расточка, нарезание резьбы и т.д.) и осуществлять соответствующую поднастройку процесса.
Дата добавления: 2015-01-18 | Просмотры: 952 | Нарушение авторских прав
1 | 2 | 3 | 4 | 5 | 6 | 7 | 8 | 9 | 10 | 11 | 12 |
|