Класи й марки ампульного скла
Залежно від якісного і кількісного складу, а також отриманих властивостей нині розрізняють два класи і декілька марок скла, що використовується у виробництві ін'єкційних лікарських форм. Склад деяких марок ампульного скла наведений в табл. 19.4.
До вітчизняних марок (сортів) ампульного скла належать НС — нейтральне й АБ — безборне скло. Ампульне скло марки НС-3 є найбільш хімічно стійким із нейтральних стекол завдяки великій кількості бору оксиду (6 %). Це скло використовується для виготовлення ампул і флаконів для розчинів речовин, що піддаються гідролізу, окиснюванню тощо (наприклад розчини солей алкалоїдів). Нейтральне скло марки НС-1 містить більшу кількість бору оксиду і меншу натрію оксиду порівняно з марками НС-2 і HC-2A і використовується для ампулування лікарських речовин, менш чутливих до лугів (розчини натрію хлориду, магнію сульфату, кальцію хлориду тощо). Нейтральне скло марок НС-2 і HC-2A в наш час використовуються в основному для виготовлення флаконів для крові та інфузійних препаратів. Безборне ампульне скло марки АБ-1 є лужним і використовується для виготовлення ампул і флаконів, в які поміщають стійкі в масляних розчинах речовини, тому при цьому вилужування практично не відбувається.
Для порівняння в таблицю включені деякі інші марки скла: СНС-1 — світлозахисне нейтральне скло для виготовлення ампул ІЗ розчинами світлочутливих речовин; XT і ХТ-1 — термічно і хімічно стійке скло, що використовується для виготовлення шприців «Рекорд».
3 1996 року в Україні введена нова марка скла медичного для виготовлення ампул — УСП-1 (ТУ У 480945—2002), що відповідає першому класу.
Визначення основних показників ампульного скла
Якість ампульного скла у фармацевтичній практиці оцінюють за такими параметрами:
— візуальний контроль;
— водостійкість;
— лугостійкість;
— залишкові напруги;
— термічна стійкість;
— хімічна стійкість;
— світлозахисні властивості (для марки СНС-1). Для ампул марки УСП-1 уведені додаткові вимоги:
— сила зламу ампул із кольоровим кільцем;
— радіальне биття стебла ампул;
— відхилення від округлості ампул.
"Основні фізико-хімічні властивості ампульного скла мають відповідати вимогам, зазначеним у ТУ У 480945-005—96.
Водостійкість. Три проби, взяті з 300 г здрібненого скла масою по 11,0 г, знежирюють етанолом та ацетоном і сушать при температурі 140 °С. Три точні наважки по 10,0 г поміщають у колби •
з 50 мл свіжоперевареної води очищеної з вихідним значенням pH = 5,5. Колби закривають і стерилізують 30 хв при температурі 121 °С і тискові 0,10— 0,11 мПа. Після охолодження їх вміст титрують розчином 0,02 моль/л кислоти хлороводневої в присутності метилового червоного до перетворення забарвлення розчину від жовтого кольору до оранжевого. Водостійкість скла X, мл/г, обчислюють за формулою:
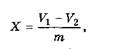
де Vj — об'єм розчину кислоти хлороводневої, витрачений на титрування досліджуваного розчину, мл; V2 — середній об'єм розчину кислоти хлороводневої, витрачений на титрування кожного з двох контрольних дослідів, мл; m — маса скла, г.
Лугостійкість. Метод ґрунтується на впливі суміші рівних об'ємів розчину 0,5 моль/л натрію карбонату і розчину 0,1 моль/л натрію гідрокарбонату на зразки скла площею 0,10—0,15 дм2 при кип'ятінні протягом 3 год. Перед випробуванням і після дії лужних розчинів зразки миють, висушують при температурі 140 °С до сталої маси і зважують.
Лугостійкість скла X, мг/дм2, розраховують за формулою:

де m — маса зразка до обробки, мг;
т1 — маса зразка після дії лугів, мг;
S — площа поверхні зразка, дм2.
Залишкові напруги. Чим різкіше охолодження, тим більш значний температурний перепад усередині скла і тим більшими будуть сили розтягу в поверхневих і сили стиску у внутрішніх шарах стінок ампул. При швидкому нагріванні ампул, навпаки, у зовнішніх шарах стінок виникають сили стиску, а у внутрішніх — сили розтягу. Опір скла стискові в багато разів вищий від опору його розтягові. Тому ампули, як і інші скляні вироби, більш термостійкі при швидкому нагріванні, ніж при швидкому охолодженні.
Напруги, що залишилися в склі після охолодження, називаються залишковими; якщо напруги зникають, то їх називають тимчасовими. Залишкові напруги здебільшого і визначають термічну стійкість ампул або флаконів.
Напруги утворюються при виготовленні ампул завдяки нерівномірному нагріванню різних ділянок дроту. Залишкові напруги
визначають поляризаційно-оптичним методом за різницею проходження променів у досліджуваному зразку, якщо він має залишкову напругу, за допомогою полярископа-поляриметра ПКС-125, ПКС-250 і полярископа ПКС-500.
Різницю ходу променів Д, нм, обчислюють за формулою:
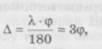
де X — при зеленому світлофільтрі (540 нм);
ф — кут повороту лімба аналізатора, град.
Різницю ходу Д1, віднесену до 1 см шляху променя в склі, млн -1, обчислюють за формулою:
A1=^
1
де 1 — довжина шляху променя в напруженому склі, см.
Не допускається залишкова напруга, яка містить питому різницю ходу Д1 більше 8 млн-1. Для зняття залишкових напруг скляні вироби піддають відпалу.
Термічна стійкість. Ампули повинні мати термічну стійкість, тобто не руйнуватися при різких коливаннях температури (при стерилізації). Перевірку термічної стійкості проводять згідно з ГОСТом 17733.
50 ампул витримують при температурі 18 °С 30 хв, потім поміщають у сушильну шафу не менше ніж на 15 хв при температурі, зазначеній в ГОСТі. Після цього ампули занурюють у воду з температурою 20±1 °С і витримують не менше 1 хв.
Термостійкими повинні бути не менше 98 % ампул від узятих на перевірку. Ампули із деяких марок скла мають витримувати перепади температур, наведені у табл. 19.5.
Хімічна стійкість. Для
Таблиця 19.5 ОЦІНКИХІМІЧНОЇСТІЙКОСТІ
Рекомендований перепад температур ампульного скла існують
для деяких марок ампульного скла різні методи визначення:
Марка скла
| Перепад температур, °С
| АБ-1
| не менше 110
| НС-1
| — <«— 130
| УСП-1
| —«— 130
| СНС-1
| —«— 150
| НС-3
| —«— 160
| за допомогою різних кислотно-основних індикаторів (зміна забарвлення), за допомогою рН-метра (зсув pH); вагові методи (кількість вилужених компонентів із зважених скляних зразків при контактуванні з водою) тощо.
Як контрольні зразки зазвичай береться вода очищена і різні спеціальні розчини лікарських речовин, що контактуватимуть зі склом ампул при виготовленні ін'єкційних розчинів і їх зберіганні.
Офіцинальним методом визначення хімічної стійкості ампульного скла є метод визначення за допомогою рН-метра, прийнятий ОСТом 64-2-485—85. Для цього ампули, двічі промиті гарячою водою, двічі обполіскують водою демінералізованою і заповнюють водою очищеною, що має pH = 6,0±2,0 і температуру 20±5 °С, до номінальної місткості. Запаяні ампули стерилізують в автоклаві при тискові 0,10—0,11 МПа і температурі 120±1 °С протягом 30 хв. Потім ампули охолоджують до температури 20±5 °С, перевіряють їхню герметичність і розкривають капіляри. За допомогою рН-метра визначають зсув pH води, вийнятої з ампул, стосовно pH вихідної води. Встановлено норми зміни значення pH для ампул: скла УСП-1 — не більше 0,8; НС-3 — 0,9; СНС-1 — 1,2; НС-1 — 1,3; АБ-1 — 4,5.
Кількість ампул з однієї партії для перевірки хімічної стійкості повинна відповідати даним таблиці 19.6.
Таблиця 19.6 Рекомендована кількість ампул з однієї партії для перевірки хімічної стійкості
| Номінальна місткість, мл
| Кількість ампул, шт.
| 1,0
|
| від 1,0 до 5,0 (вкл.)
|
| від 5,0 до 20,0 (вкл.)
|
| понад 20,0
|
| 3 інших відомих методів своєю простотою вирізняється метод визначення хімічної стійкості ампульного скла за допомогою кислотно-основного індикатору фенолфталеїну (запропонований Д. I. Поповим і Б. А. Кляч-кіною). Для цього ампули заповнюють водою для ін'єкцій із додаванням 1 краплі 1 %-вого розчину фенолфталеїну на кожні 2 мл води, запаюють і стерилізують при 120 °С протягом 30 хв. Ампули, в яких вода після стерилізації не забарвилась, належать до першого класу. Вміст забарвлених ампул титрують розчином 0,01 моль/л кислоти хлороводневої, за кількістю якої визначається хімічна стійкість ампульного скла. Якщо на титрування до знебарвлення розчину її витрачено менше 0,05 мл, ампули належать до другого класу, більше 0,05 мл — ампули вважаються непридатними для зберігання ін'єкційних розчинів.
Можна також визначити хімічну стійкість ампульного скла за зміною забарвлення метилового червоного. При цьому ампули заповнюють кислим розчином метилового червоного до необхідного об'єму, запаюють і стерилізують у стерилізаторі при 120 °С протягом 30 хв. Якщо після охолодження колір всіх ампул не змінився на жовтий, то такі ампули придатні для використання.
Світлозахисні властивості. Ці властивості досліджують в ампулах, виготовлених з нейтрального світлозахисного скла вимірюванням їхнього світлопропускання в ділянці спектра від 290 до 450 нм (ГОСТ 17651—72).
3 циліндричної частини ампули вирізають зразок, ретельно промивають його, протирають, висушують і поміщають паралельно щілині спектрофотометра СФД-2. Визначають максимальний відсоток світлопропускання, що повинний складати при товщині стінки ампули від 0,4 до 0,5 мм 35 %; від 0,5 до 0,6 мм — 30 %; від 0,6 до 0,7 мм — 27 %; від 0,7 до 0,8 мм — 25 % і від 0,8 до 0,9 мм — 20 %.
Сила злому ампул із кольоровим кільцем визначається на установці, схема якої наведена на рис. 19.3, із такими характеристиками:
— швидкість випробування — 10 мм/хв;
— верхня межа виміру сили — 200H;
— температура ампули, що перевіряється, 20±5 °С.
Кількість ампул із кольоровим кільцем відлому для визначення сили зламу повинна бути не менше 0,01 % від всієї партії.
Сила злому ампул із кольоровим кільцем відлому повинна відповідати показникам, наведеним у табл. 19.7:
Таблиця 19.7
Значення сили злому ампул
Номінальна місткість, мл
| Сила злому, Н
| Довжина L — /j + 12, мм
|
| від 30 до 70 (вкл.)
| 36 = 18 + 18
|
| від ЗО до 70 (вкл.)
| 36 = 18 + 18
|
| від ЗО до 90 (вкл.)
| 60 = 22 + 38
| Радіальне биття стебла ампул відносно осі корпусу. Радіальне биття стебла ампул відносно осі корпусу і радіальне биття конічних кінців відносно осі циліндричної частини ампули типу Г перевіряється за допомогою універсального стояка типу CT за ГОСТом 10197 або ТУ 2-034-623, призми перевірної — за ТУ 2-034-439 або ТУ 2-034-812 та індикатора годинникого типу — за ГОСТом 577.
Ампулу, що перевіряється, укладають на перевірну призму, підводять наконечник індикатора до стебла ампули, а для ампул
типу Г — до конічного кінця й обертають ампулу на 360°. Різниця найбільшого і найменшого показань індикатора не повинна перевищувати значень, зазначених у табл. 19.8.
Таблиця 19.8
Допустиме радіальне биття стебла ампул відносно осі корпусу
Тип ампул
| Місткість ампул, мл
| Радіальне биття, мм
| ІП
| 1,2
| 1,0
| ш
|
| 1,2
| ІП
| 5, 10, 20
| 1,5
| ВВІ С
| 1, 2, 3
| 1,7
| ВВІ С
|
| 2,0
| впв
|
| 2,0
| 19.3.2. ВИГОТОВЛЕННЯ АМПУЛ
Виробництво ампул здійснюється зі скляних трубок (дроту медичного) і включає такі основні стадії: виготовлення скло-дроту, миття і сушіння дроту, виготовлення ампул.
Склодріт виготовляється на скляних заводах із медичного скла. Якість дроту регламентується такими показниками: конусність, рівностінність, прямолінійність, відмивність від забруднень. Дріт має бути однорідним (без бульбашок повітря і механічних включень), правильної форми в поперечному розрізі (коло, а не еліпс) і однакового діаметра по всій довжині.
Виготовлення склодроту і вимоги до його якості. Дріт виготовляється витягуванням із рідкої скляної маси на спеціальних лініях AT 2-8-50, установлених на скловарних печах. Довжина трубок повинна складати 1500±50 мм, зовнішній діаметр від 8,0 до 27,00 мм, що регулюється зміною кількості подачі скломаси на формувальні пристрої, зміною величини тиску повітря і швидкості витягування.
Основними вимогами, що висуваються до склодроту відповідно до ТУ 64-2-5—76, є: відсутність різних включень (дефектів), чистота зовнішньої і внутрішньої поверхонь, стандартність за розміром; трубки мають бути циліндричними та прямолінійними.
Дефекти скляних трубок здебільшого визначаються якістю скломаси. Скло, отримане в промислових печах, завжди має ті або інші включення (вкраплення), які класифікують за трьома видами: газові, склоподібні та кристалічні.
| Газові включення характеризуються наявністю в склі різних газів, що можуть бути у вигляді бульбашок (видимі включення) і розчиненими в скломасі (невидимі включення). Розміри видимих неозброєним оком бульбашок коливаються від десятих долей до декількох міліметрів. Дрібні бульбашки називаються «мошкою>>. У бульбашках можуть міститися різні гази або їх суміші: 02, CO, С02 тощо. У склі іноді утворюються сильно витягнуті бульбашки, що називаються порожнистими капілярами. Причинами газових включень можуть бути: неповне видалення газоподібних продуктів розкладання елементів шихти при її варінні, попадання повітря в скломасу тощо. Такі компоненти скломаси, як карбонати, сульфати, нітрати, викликають обмінні й інші реакції з виділенням газів, що залишаються всередині скломаси.
До заходів запобігання виникненню бульбашок газу належать: правильний добір матеріалів, використання оптимальної кількості склобою, дотримання технологічного режиму варіння скломаси.
Склодріт не повинен містити капілярів і бульбашок, що продавлюються сталевою голкою, розмір їх допускається не більше 0,25 мм.
Кристалічні включення (камені) є головним дефектом скломаси. Вони знижують механічну міцність і термічну стійкість виробу зі скла, погіршують його зовнішній вигляд. Розмір їх коливається в межах декількох міліметрів. Під дією високої температури вони можуть розплавлятися, утворюючи склоподібні краплі.
За зовнішнім виглядом ці включення являють собою одиночні камені або пучкоподібні нитки в товщі скломаси. Нитки надають склу нашарованості, утворюючи звилини. Основною причиною утворення звилин вважають потрапляння в скломасу сторонніх речовин і недостатню гомогенізацію скломаси.
На скляних трубках неприпустима наявність шихтних каменів розміром понад 2 мм (груба, відчутна на дотик звилина).
Калібрування дроту. Для одержання ампул однієї партії (серії) необхідно використовувати трубки одного діаметра і з однаковою товщиною стінОк, щоб ампули однієї серії мали задану місткість. Точність калібрування визначає стандартність ампули і має велике значення для механізації й автоматизації ампульного виробництва. 3 цією метою дріт калібрують за зовнішнім діаметром на машині H. А. Філіпіна (рис. 19.4).
Скляні трубки 7, попадаючи в машину по напрямним 1, скочуються до упору 6, звідки за допомогою захватів 5 подаються на калібри 4. На вертикальній рамі машини 3 закріплено п'ять калібрів. Якщо діаметр трубки більший за отвір калібру, трубка піднімається вище захватами нагору на наступні калібри з великим зазором. Трубки, діаметр яких відповідає розміру калібру, по похилим напрямним скочуються в накопичувач 2, звідки надходять до мийки.
Миття і висушування дроту. Відомо декілька способів миття дроту. Найпоширенішим є камерний спосіб. Установка для промивання має дві камери, які герметично закриваються і завантажуються вертикально стоячими пучками дроту. Камери заповнюють гарячою водою або розчином мийного засобу, після чого подають пару або стиснуте повітря через барботер. Потім рідину з камери Рис 194 Схема установки для калібру-
ЗЛИВаЮТЬ І ДрІТ промивають вання дроту за зовнішнім діаметром
душуванням знесоленою водою під тиском. Для сушіння всередину камери подається гаряче фільтроване повітря. Найефективнішим є спосіб миття за допомогою ультразвуку, який застосовується на ФФ «Здоров'я». Установка такого миття трубок працює за такою схемою. Трубки в горизонтальному положенні подаються на транспортні диски, підходять до газових пальників для оплавлення з одного боку і занурюються в барабан ванни, заповненої гарячою водою очищеною знесоленою. На дні ванни розташований ряд магнітострикційних генераторів ультразвуку. Додатково в отвори трубок із сопел подається струмінь води. У такий спосіб дія ультразвуку поєднується зі струминним миттям. Вимиті трубки висушують в повітряних сушарках при температурі 270 °С.
Значно підвищує ефективність миття контактно-ультразвуковий спосіб, тому що в цьому разі до специфічної дії ультразвуку (кавітація, тиск) додається механічна вібрація трубок із високою частотою.
Виготовлення ампул. В європейських країнах і в нашій країні ампули виготовляють на склоформуючих автоматах роторного типу при вертикальному положенні трубок і безперервному обертанні ротора. Продуктивність таких автоматів коливається в межах 2000—5000 ампул за годину. Найбільше використовують шістнадцяти- і тридцятишпиндельні автомати. Шістнадцятишпиндель-ні автомати мають автоматичну систему подачі трубок у робочу зону, завдяки чому один оператор може одночасно обслуговувати дві або три машини.
На вітчизняних заводах фармацевтичної промисловості широко застосовуються автомати IO-8 «Тунгсрам» (Угорщина), «Амбег», «Матвер» (Німеччина). Усередині станини — основи автомата — розташований привід каруселі, яка безперервно обертається і несе
на собі 16 пар вертикальних верхніх та нижніх шпинделів (патронів). На верхній плиті каруселі встановлені накопичувальні барабани для автоматичного завантаження трубками верхніх шпинделів, усередині каруселі закріплені нерухомі пальники. Карусель охоплює кільце, яке здійснює коливальний рух навколо її осі і на якому розміщені спрямовані всередину рухомі пальники. Кільце несе на собі також пристрій для формування перебивки капіляра ампул та інший необхідний інструмент. У центральній зоні каруселі змонтована труба для відсмоктування і відведення гарячих газів, що утворюються під час роботи автомата. У нижній його частині в місці виходу готових ампул можуть бути розташовані
пристрої для різання, сортування та набору в касети готових ампул. На рис. 19.5 подана схема виготовлення ампул на автоматах цього типу. Трубки завантажуються в накопичувальні барабани і послідовно проходять шість стадій:
1) трубки подаються з накопичувального барабана всередину патрона і за допомогою обмежувального упора встановлюється їхня довжина. Верхній патрон стискує трубку, залишаючи її на постійній висоті;
2) до трубки підходить відтяжний пальник із широким полум'ям і розігріває її ділянку, що підлягає розтягуванню. У цей час нижній патрон, рухаючись по копіру, піднімається нагору і затискає нижню частину трубки;
3) після розігрівання скла нижній патрон опускається вниз, і розм'якшена ділянка трубки розтягується, утворюючи капіляр ампули;
4) і 5) далі відрізний пальник із гострим полум'ям відрізає вже готову ампулу, одночасно формуючи (запаюючи) денце наступної ампули;
6) при подальшому обертанні ротора (каруселі) розкриваються затискачі нижнього патрона, і готові ампули скидаються в накопичувальний лоток. Трубка із запаяним денцем підходить до обмежувального упора 1-ї стадії, і цикл роботи автомата повторюється.
Головною вадою цього способу є утворення всередині ампул вакууму при охолодженні їх до кімнатної температури. При розкритті капіляра осколки, що утворюються, і скляний пил засмоктуються всередину ампули. Для вирішення цієї проблеми було запропоновано наносити на капіляр ампули кільцеву риску (надріз) з подальшим покриттям її спеціальною сумішшю для затримання осколків.
Інший варіант вирішення завдання щодо забезпечення розкриття ампули без утворення скляного пилу передбачає виробництво ампул, у вільному об'ємі яких знаходиться інертний газ під невеликим тиском; при цьому передбачається, що при розкритті ампули вихідний газ відкине осколки скла і пил, і вони не потраплять в ін'єкційний розчин.
Останнім часом для одержання безвакуумних ампул у момент відрізу ампули додатково нагрівають спеціально встановленим пальником. Повітря, що знаходиться в ампулі, розширюється при нагріванні, проколює скло в місці відпайки; і вакуум у такій ампулі при її охолодженні не утвориться. Існує ще один метод: у момент відпайки ампули нижній патрон відкривається; і під дією сили ваги ампули в місці відпайки витягається дуже тонка капілярна трубочка, що обламується при падінні ампули в збірник, і завдяки цьому вакуум не утворюється.
Для формування на ампулах перебивки застосовують пристрій з профільованими роликами.
Продуктивність автомата IO-80 при виробництві ампул місткістю 1—10 мл при виготовленні спарених ампул складає 3500— 4000 ампул за годину. Конструкція автомата дозволяє виготовляти одинарні, подвійні ампули й ампули складної конфігурації.
Серед способів виготовлення ампул із трубок можна виділити технологію, яку застосовують на підприємствах Японії. Цей спосіб полягає ось в чому: на спеціальних машинах горизонтально розташована трубка в декількох ділянках по довжині одночасно розігрівається пальниками і потім розтягується, утворюючи ділянки з перебивками (майбутніми капілярами ампул). Потім скляну трубку розрізають на окремі заготовки по середній частині пере-бивок. Кожна заготовка, у свою чергу, розрізається термічним способом на дві частини з одночасним формуванням дна в обох ампулах, що утворюються при цьому.
За описаним технологічним способом із використанням спеціального устаткування досягається висока продуктивність від 2500 шт./год великомістких до 3500 шт./год маломістких ампул.
На зазначених вище автоматах, як правило, одержують герметично запаяні ампули, в яких відразу обрізається капіляр за допомогою спеціальних приставок. Потім ампули встановлюють-
ся «капіляром догори» у металеву тару і направляються на стадію відпалу.
Американською фірмою «Корнінг Гласс» розроблений новий метод виготовлення ампул без проміжного виготовлення трубок. Фірмою створена серія високопродуктивних стрічкових машин, на яких відбувається струминно-видувний процес формування скла, що забезпечує високий ступінь рівномірності його розподілу по стінках готових виробів. Виготовлення виробів на стрічкових машинах вимагає підтримання стабільності температурного режиму і регулювання тиску з високою точністю, для чого використовується високоточна вимірювальна апаратура. Стрічкові машини при діаметрі виробів 12,7—43,18 мм можуть працювати з високою продуктивністю — до 9000 шт./год.
Дата добавления: 2016-03-26 | Просмотры: 862 | Нарушение авторских прав
1 | 2 | 3 | 4 | 5 | 6 | 7 | 8 | 9 | 10 | 11 | 12 | 13 | 14 | 15 | 16 | 17 | 18 | 19 | 20 | 21 | 22 | 23 | 24 | 25 | 26 | 27 | 28 | 29 | 30 | 31 | 32 | 33 | 34 | 35 | 36 | 37 | 38 | 39 | 40 | 41 | 42 | 43 | 44 | 45 | 46 | 47 | 48 | 49 | 50 | 51 | 52 | 53 | 54 | 55 | 56 | 57 | 58 | 59 | 60 | 61 | 62 | 63 | 64 | 65 | 66 | 67 | 68 | 69 | 70 | 71 | 72 | 73 | 74 | 75 | 76 | 77 | 78 | 79 | 80 | 81 | 82 | 83 | 84 | 85 | 86 | 87 | 88 | 89 | 90 | 91 | 92 | 93 | 94 | 95 | 96 | 97 | 98 | 99 | 100 | 101 | 102 | 103 | 104 |
|