АкушерствоАнатомияАнестезиологияВакцинопрофилактикаВалеологияВетеринарияГигиенаЗаболеванияИммунологияКардиологияНеврологияНефрологияОнкологияОториноларингологияОфтальмологияПаразитологияПедиатрияПервая помощьПсихиатрияПульмонологияРеанимацияРевматологияСтоматологияТерапияТоксикологияТравматологияУрологияФармакологияФармацевтикаФизиотерапияФтизиатрияХирургияЭндокринологияЭпидемиология
|
БРОНХИАЛЬНОЕ ДЕРЕВО
Анализ теоретических и экспериментальных исследований по холодной правке длинномерных заготовок, проведенный в данной работе, показал, что заготовки, имеющие начальные прогибы более 5 мм/м, не могут быть использованы при эксплуатации валов высокой точности - менее 20 мкм/м без применения дополнительных термостабилизирующих операций.
Автором разработаны новые способы термообработки длинномерных деталей, суть которых заключается в приложении управляемых осевых нагрузок при термообработке. Этот технологический прием назван - термосиловая обработка ТСО, его подробное описание было проведено ранее. В этой главе приводятся только результаты экспериментальных исследований.
Разработанная новая технология изготовления длинномерных осесимметричных деталей, включает в себя и изготовление изделий, материал которых склонен к упрочнению, (например, нержавеющие аустенитные стали, типа 12X18H10T. Стали аустенитного класса обладают некоторыми специфическими свойствами. Аустенитно-мартенсктное превращение сопровождается увеличением объема материала, что может привести к созданию внутренних напряжений, к короблению деталей, для избежания этого необходимо для решения задачи пластического деформирования аустенита ограничиться малыми степенями деформации (e < 10 %). Вопросы мартенситного превращения в процессе деформации изучались, однако результаты этих работ не доказывают возможности ТСО без распада аустенита в сталях с недостаточной его устойчивостью. Поэтому при выборе оптимальных режимов ТСО необходимо было исследовать условия образования мартенсита, а также мехсвойства нержавеющих сталей при различных температурных режимах обработки.
О том, что предшествующая пластическая деформация может значительно изменить поведение металла в условиях последующего нагружения было исследовано в работах других работах. Теория упругого последействия в твердых телах, предложенная авторами, получила значительное развитие в работах Вольтера, который очень точно назвал ее наследственной теорией. Следует заметить, что и температурный диапазон, в котором справедлива линейная теория для реальных материалов, довольно узок. Сравнительный анализ результатов, полученных различными исследованиями, затруднен, так как в различных работах применялись разные схемы, скорости и температуры деформирования. На результат испытаний оказывают сложное взаимное влияние по крайней мере семь факторов: скорость нагрева до температуры деформирования, температура деформирования, продолжительность выдержки при температуре деформации, степень деформации, скорость деформирования, скорость охлаждения до комнатной температуры, режим заключительного отпуска.
Несмотря на некоторые противоречия результатов, полученными различными исследователями, анализ их все же позволяет произвести выбор диапазона режимов ТСО, обеспечивающего влияние пластической деформации на поведение металла при последующем нагружении путем введения функции памяти, а также обеспечивающего стабильную структуру аустенита с минимальным, выровненным уровнем остаточных напряжений.
С целью подтверждения теоретических разработок и новых способов ТСО перед цеховыми испытаниями, были проведены лабораторные испытания.
Испытания проводились на разрывной машине фирмы AMSLER (Швейцария). Цилиндрические образцы для испытаний были изготовлены согласно ГОСТ 1497-84 (Ст. СЭВ 471-77). Для решения поставленной задачи была разработана специальная методика испытаний. Результаты приведенных испытаний свидетельствуют о наличии постоянства предела текучести в диапазоне температур Т° = 200°…400°С на всем интервале деформации и уменьшении предела пропорциональности порядка 25 % … 30 %.
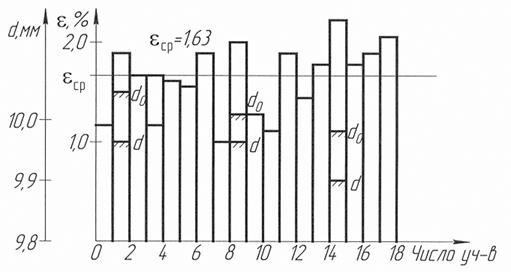
а)
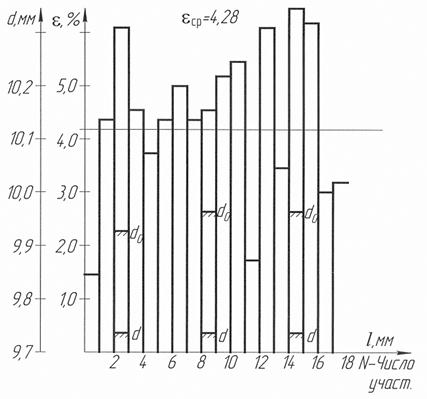
б)
Рис.3.18. Диаграммы распределения относительной деформации по длине образцов: а – для εср=1,63; б – для εср=4,28
В интервале температур Т° = 200…600°С при испытании на разрыв стали 12X18H10T преобразований аустенита в мартенсит не обнаружено, что свидетельствует о структурной стабильности материала в указанном диапазоне температур. Известно, что коррозионная стойкость нержавеющих сталей имеет "пороговое" значение величины пластической деформации, выше которой склонность к коррозионному растрескиванию резко возрастает, что имеет большое значение при осевой деформации. Рентгеноструктурный и магнитно-металлографический анализ выявили, что снижение коррозионной стойкости в данных условиях обусловлено фазовым g - a превращением, названным пластической деформацией. Таким образом, испытания подтверждают возможность холодного (при Т=20°С) деформирования аустенита без образования "мартенсита деформации" (при e ≤ 8 %).
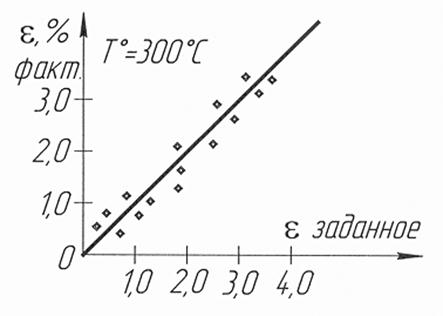
Рис.3.19. Экспериментальная зависимость величины фактической деформации от заданной
В процессе обработки результатов, полученных при испытаниях образцов на разрыв, были определены зависимости предела текучести s02, и предела прочности sВ от температуры деформирования. Ломаный характер прямой, описывающей изменение предела прочности sВ объясняется влиянием следующих факторов: 1. Образованием a-фазы при пониженных температурах, а, следовательно, более интенсивным упрочнением. 2. Более интенсивным развитием межкристаллитного разрушения в наклепанном аустените при температуре 600°С. Эти же факторы оказывают влияние и на характер кривой зависимости удлинения образца при осевом усилии от температуры.
Для проведения металлографического исследования были выполнены шлифы вдоль оси образцов - в месте разрыва и в цилиндрической части. Анализ результатов показывает, что зерна кристаллов вытянуты (особенно ярко выражено в местах разрыва). Анализ микроструктуры образцов, подвергнутых растяжению на 10% при температуре 300°С, показывает, что деформация такой величины не вызывает значительных изменений размеров и конфигурации зерен. Очевидно, удлинение образца и уменьшение его диаметра произошло за счет скольжения между зернами металла.
Проведенные эксперименты позволяют сделать следующие выводы: термосиловую обработку - ТСО деталей целесообразно проводить в интервале температур 200 … 400°С, возможна осевая деформация при Т = 20° без образования a-фазы, при степени пластической деформации e ≤ 8 %, при степени деформации e < 10 % формоизменение образца происходит за счет микродеформации в зернах, разворота зерен и скольжения зерен и не сопровождается изменением размеров зерна.
Предварительные измерения твердости показали, что твердость образцов после их растяжения при температурах 200°С, 400°С, 600°С одинакова и составляет HRС 25-26 ед. В зоне разрыва твердость несколько выше и составляет HRC 28 … 32 ед. Максимальное значение твердости в зоне разрыва достигается при температуре 400°С. При температуре 600°С увеличение твердости в зоне разрыва практически не наблюдается и составляет HRC 26 … 27 ед.
Одной из задач лабораторных исследований было оценить пластическую деформацию при ТСО по длине образца. Проанализировать влияние геометрических параметров заготовок, температурно-силовых режимов на равномерность деформации по длине.
Образцы имели ту же геометрию, что в предыдущем эксперименте, только на длине, равной десяти диаметрам, были накатаны круговые риски, расстояние между которыми (с шагом 5 … 0,01) измерялось до и после эксперимента, диаметры между рисками также измерялись и строились графики зависимости заданной деформации от фактической, равномерность удлинений и уточнений по длине, оценивалась коэффициентом локальности как величиной отношений максимальной деформации к минимальной. Контролировались усилия нагрузки, разгрузки и выстоя. Температурный режим был дискретным Т° = 20°С, 300°С, а величина относительной пластической деформации задавалась в интервалах e = 0,8%, 2 %, 4 %, 6 %. Материал - сталь 12Х18H10T и сталь 50. Технология изготовления образцов и методика проведения экспериментов вынесена в приложении диссертации. Наиболее характерные диаграммы распределения относительной деформации по длине образца приведены на рис. 5.4 и 5.5. На рис. 5.6 приведена экспериментальная зависимость величины фактической деформации от заданной. Из графика видно, что действительная величина деформации соответствует заданной при e ≤ 4 %. При относительной деформации более 4 % эта зависимость носит нелинейных характер. Анализ полученных диаграмм позволяет сделать вывод о том, что деформация образцов происходит по всей длине образцов, а не в некоторых его участках, причем при e = 4 … 6 % деформации растяжения более равномерны, конечно при тех геометрических параметрах, которые имели образцы. Нет ярко выраженной зависимости между относительным удлинением отдельных частей образца и их диаметрами. Коэффициент локальности был в пределах 1,5 … 5 и он был стабилен при e = 4 %. В методике было предусмотрено, что после деформации образец находился при постоянной температуре 30 мин., одновременно измерялось усилие деформации. Во всех экспериментах после выстоя при постоянной температуре рабочее усилие падало до 25 … 30 %. Ставилась также задача по определению биения образцов до и после ТСО. Биение контролировалось в трех точках. Корреляционной зависимости биения от величины деформации не устанавливалось, однако замечено, что после ТСО биение возрастает, что связано с технологией изготовления образцов и предварительным прогибом заготовки порядка 0,9 мм. Чтобы устранить этот технологический недостаток, необходимо изменить порядок изготовления образцов. Анализ результатов проведенных экспериментов показывает, что необходимо уточнить зависимость температуры и величины пластической деформации на ее равномерность. Для этого цел сообразно уменьшить шаг нагрева до 50°С в интервале температур 200 … 400°C, а интервалы изменения деформации до 1 %. Необходимо также проверить равномерность пластической деформации при e = 10 % и 15 %, что традиционно считается областью больших деформаций. Таким образом, экспериментальные исследования показывают, что свойства материала при различных деформированиях, величины пластической деформации имеют большие разбросы и, следовательно, применение традиционной технологии не приводит и не приведет к желаемому результату для заготовок из нержавеющих и конструкционных сталей с отношением , так как по длине заготовки выше перечисленные параметры переменны. В этом случае целесообразно считать оптимальным технологический процесс, в котором осуществляется диагностирование выше перечисленных параметров, а сам процесс управляется с учетом индивидуальных физико-химических характеристик заготовки.
Результаты обработки лабораторных исследований на стандартных образцах свидетельствуют о том, что можно обеспечить равновесное и равномерное распределение остаточных напряжений и обеспечить совместность пластических деформации (для симметричных конструкций совместность деформаций означает их равенство) за счет подбора режимов обработки материала, которые находятся в пределах Т° = 250 … 400°С, e = 3 … 5 %, e = 1 × 10-3 … 1 × 10-5 С-1,критерий локальности от 1,1 до 1,15.
В связи с уменьшением эффективности ТСО с ростом начального искривления вала, в технологическом процессе изготовления маложестких валов необходима предварительная правка, начально снижающая величину биения хотя бы до 0,3 мм на погонный метр.
Теоретические и экспериментальные исследования на образцах позволили провести апробацию предложенных методов в цеховых условиях. Установка, применяемая при закалке (стапель), подробно описана в главе 4.2. Следует только напомнить суть способа, материал стапеля имеет коэффициент линейного (термического) расширения, его численное значение больше, чем коэффициент линейного расширения материала заготовки и при нагревании, за счет разности этих коэффициентов, при температуре закалки стапель, удлиняясь, пластически деформирует деталь - "горячая правка". С целью обеспечения постоянной осевой нагрузки стапель выполнен многослойным, а в качестве наполнителя использовался кварцевый песок (рис.3.20). Обрабатывались валы насоса 101 а, изготовленные из стали 30X13, а стапель из стали 12Х18H10T. Геометрические параметры заготовки, длина 3400 мм, диаметр 45 мм, готовой детали длина 3200 мм, диаметр 38 мм. Температурный режим термообработки не изменялся, температура закалки Т° = 1000 … 1050°С, с последующим охлаждением на воздухе. По концам заготовки нарезалась резьба М 42 × 2,5 для накручивания на ее концы сферических тяг (захватов). Измерялось биение заготовки и готовых деталей в десяти сечениях по всей длине, при этом изделие устанавливалось на две призмы так, чтобы вал был поделен на три равные части. По предлагаемой технологии вал обрабатывался на токарном станке с использованием САУ, правился на установке для правки и термообрабатывался в стапеле. После остывания на воздухе осуществлялся контроль равномерности пластической деформации по длине, биений в десяти сечениях и одновременно измерялась твердость по длине изделия.
Термообработка (закалка) с использованием разработанного приспособления дала положительные результаты, биение вала было не более 10 мкм/м и не превышало допуск на токарную обработку, коэффициент локальности был порядка 1,5 … 2,3. Разброс по твердости не превышал 12 % максимум. Следует заметить, что при традиционной технологии заготовка мехобработку не проходила, а закалка проводилась в свободно подвешенном состоянии, в этом случае, биение валов было в пределах 7 … 8 мм.
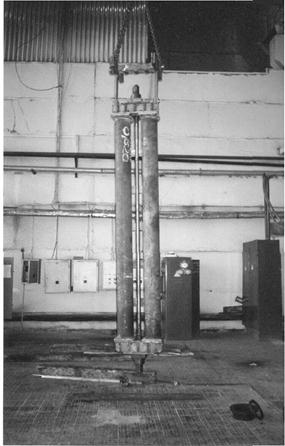
Рис.3.20. Общий вид установки стапеля для закалки длинномерных валов
Особо следует отметить, что после закажи плоскость максимального прогиба разворачивалась в пределах 40…45°, что свидетельствует о наличии больших касательных напряжений в заготовке. Последнее, к сожалению, не учитывалось в теоретических разработок.
Напряжения, полученные при закалке, максимальные, будут интенсивно релаксировать в результате местной пластической деформации. Таким образом, чтобы устранить релаксацию необходимо либо уменьшить действующие напряжения, либо повысить сопротивление металла пластическому деформированию, т.е. повысить релаксационную стойкость.
Предложенная технология закалки, если бы она была окончательной операцией, могла бы удовлетворить по геометрической точности, но не гарантировала стабильность формы в случае дальнейшей механической обработки при формировании продольного профиля. Для минимизации уровня остаточных напряжений и деформирования однородности и равновесности распределеления остаточных напряжений по всему объему детали не только при изготовлении, но и эксплуатации был предложен технологический прием и здесь остановимся только на его сути.
К заготовке при температуре отпуска, когда предел пропорциональности ее материала не изменяется или изменяется в узких пределах, что приемлемо и к материалам, склонным к упрочнению, прикладывается управляемая, в функции пластической деформации, осевая сила и путем управления температурным режимом по длине заготовки обеспечивается равенство пластических деформаций. Теоретический анализ этого технологического приема был подробно описан ранее.
Общий вид установки, где на переднем плане представлен управляемый привод осевой деформации, представлен на рис.3.22.
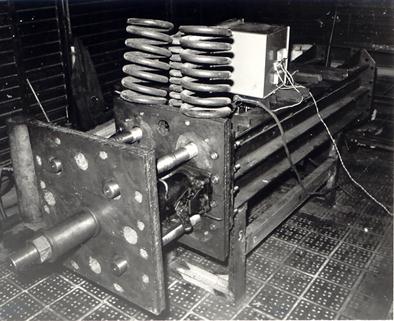
Рис.3.21. Общий вид установки для ТСО длинномерных деталей
Алгоритм работы термосиловой установки в автоматическом режиме и методику проведения эксперимента.
Результаты, полученные при испытаниях, оформлены протоколами, а наиболее типичные графики зависимости критерия локальности от величины относительной деформации представлены на рис.3.24. Испытания проводились при температуре нагрева 300°С, деформации в диапазоне 4 … 6 % и скорости деформации e = 1 × 10-3 С-1. После отпуска с применением ТСО заготовку замеряли на биение, по ранее описанной методике. Следует заметить, что точность (биение) не превышала 20 мкм/м. в течение 24 часов. Далее согласно технологии заготовка обтачивалась на токарном станке, оснащенном САУ.
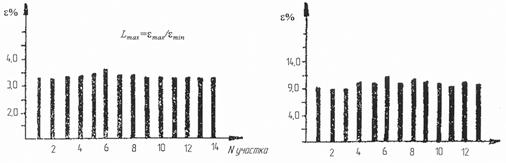
Рис.3.22. Диаграммы осевой пластической деформации
С целью расширения эксперимента была проведена ТСО заготовок изготовленных из стали 45 и 12Х18Н10Г. Температурный режим Т° = 400°С и Т° = 600°С, а величина пластической деформации составляла 4 %. Контролировалось биение в 10 сечениях, равномерность пластических деформаций по всей длине заготовки, длина которой была ограничена до 1300 мм. Перед ТСО заготовки обеспечивались с диаметра 42 мм до 30 мм (режимы: 1 проход – V = 350 об/мин, S = 0,75 мм/об, t = 2 мм; 2 … 3 проходы – V = 270 об/мин, S = 0,19 мм/об, t = 2 мм, геометрия резца стандартная, материал TI5K6). Измерялось биение после каждого прохода и было замечено, что прогиб заготовки уменьшается порядка 20 % и имеет максимум в середине вала, более подробно поведение заготовки с позиции релаксационных процессов будет рассмотрено в приложении. Результаты экспериментальных исследований представлены на рис.3.24.
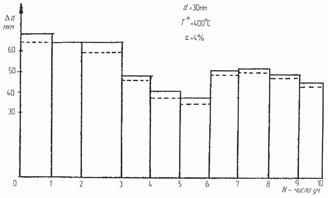
Рис.3.23. Диаграммы осевой пластической деформации при ТСО при температуре 400ºС, d = 30 мм и ε = 4%
Оценивая результаты исследований ТСО следует отметить, что предлагаемый технологический прием обеспечивает выравнивание физмехсвойств материала, однородность распределения пластической деформации по всему объему заготовки, минимизирует уровень остаточных напряжений и, как следствие, снижает коробление вала как минимум в пять раз.
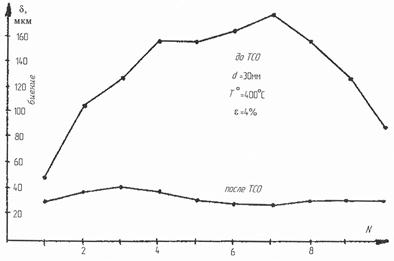
Рис.3.24. Результаты экспериментальных исследований влияния ТСО на коробление детали при температуре 400ºС, d = 30 мм и ε = 4 %: 1 – до ТСО; 2 – после ТСО
В существующей технологии термообработки металл представлен сам себе, он в свободном состоянии, в предлагаемом способе уничтожается предыдущая технологическая память и формируется новая - имеющая направленность. Влияние температурного режима: ТСО целесообразно проводить в диапазоне температур 200…400°С, мехсвойства материала в этом диапазоне практически не изменяются, увеличение твердости в этих условиях максимально. Изменение структуры металла при принятых режимах обработки не происходит, а при температуре деформации 300…400°С отсутствует фазовый наклеп (g ® a превращение), который имеет место при холодном деформировании. Особо следует отметить, что на процесс ТСО оказывают влияние касательные напряжения, плоскость максимальных деформаций изменяется на 40…45°, а в отдельных случаях доходит до 60°. Большое влияние на технологическую наследственность оказывает механическая обработка - точение. Точность мехобработки, особенно в поперечном сечении, влияет на коробление заготовок после термообработок как при закалке, так и при отпуске. Целесообразно, перед холодной правкой и ТСО, протачивать заготовки как можно точнее в пределах допуска на изготовление. Далее эксперименты с образцами разной длины показали, что интенсивное повышение предела упругости наблюдается с увеличением размеров образцов.
Управлять уровнем остаточных напряжений только с помощью пластических деформаций необходимо в начальной стадии процесса охлаждения, когда предел текучести низкий и существует слабая зависимость предела текучести от температуры. Поэтому функция управления должна учитывать, какие создавать пластические деформации в начале процесса охлаждения, чтобы получить минимальные остаточные напряжения в конце.
ТРАХЕЯ
Трахея является продолжением гортани, представляет собой полую эластическую трубку, которая начинается от перстневидного хряща и заканчивается бифуркацией на уровне IV грудного позвонка, разделяясь на два главных бронха под углом 65 - 950;. Длина трахеи у взрослого человека колеблется от 90 до 150 мм, диаметр от 15 до 16 мм. Остов трахеи состоит из 16 - 20 хрящевых неполных колец, обращенных к пищеводу и соединенных между собой кольцевидными связками [2]. Задняя стенка ее представлена мембранозной частью, состоящей из коллагеновых, эластических и гладкомышечных волокон. Такое строение трахеи позволяет ей при разных условиях менять свою конфигурацию, а следовательно, и воздушный поток. Минимальный размер трахеи соответствует фазе выдоха, максимальный - фазе вдоха. При кашлевом толчке просвет трахеи уменьшается в 3 - 10 раз в зависимости от возраста человека (чем моложе, тем больше сужается просвет). Во время вдоха бифуркация трахеи смещается вниз и на 2 - 3 см кпереди.
БРОНХИАЛЬНОЕ ДЕРЕВО
Бронхиальное дерево состоит из двух главных бронхов (правого и левого) и 23 - 26 генераций ветвлений, включая бронхиолы и альвеолярные ходы (рис. 1-1). Общее число ветвлений равно 223, т.е. около 8x10<sup>6</sup> [3]. Правый главный бронх отходит под углом 15 - 400, длина его 28 - 32 мм, диаметр 12 - 22 мм. Левый отходит под углом 50 - 700, длина составляет 40 - 50 мм, а диаметр - 8 - 16 мм [4]. Таким образом, правый главный бронх короче, шире и имеет более вертикальное направление, чем левый. Главные бронхи делятся, как правило, дихотомически на долевые, сегментарные, субсегментарные и на бронхи более мелких генераций, вплоть до терминальных и респираторных бронхиол. В стенках респираторных бронхиол I, II и III порядка уже появляются альвеолы. Респираторные бронхиолы и их альвеолы одновременно выполняют воздухопроводящую и газообменную функцию. На протяжении субсегментарных бронхов может насчитываться до 5 делений, в малых (мышечных) бронхах - до 15 делений. По мере ветвления бронхов закономерно уменьшается и их диаметр. Размерные взаимоотношения предыдущей и последующей генераций бронхов оптимальны для того, чтобы обеспечить должный поток воздуха с минимальными затратами энергии на этот процесс [5].
path: pictures/01-01.png
Рис. 1-1. Строение дыхательных путей (по Э.Р. Вейбелю, 1970 [3]).
Бронхи с 4й по 13ю генерацию имеют диаметр до 2 мм; общее число таких бронхов около 400. Наибольшее число бронхов диаметром 2 мм наблюдается с 7й по 9ю генерацию [3]. В терминальных бронхиолах диаметр колеблется от 0,5 до 0,6 мм, диаметр респираторных бронхиол (17 - 19я генерации) и альвеолярных ходов от 0,2 до 0,6 мм. Длина воздухоносных путей от гортани до ацинусов составляет 23 - 38 см, протяженность от 9й генерации бронхов до респираторных бронхиол около 5 см. В воздухоносных путях выделяют около 50 типов клеток, 12 из которых относятся к эпителиальным [6].
По мере уменьшения калибра бронхов и бронхиол хрящевая пластинка в них сначала уменьшается в размерах, а в терминальных бронхиолах исчезает. Для того чтобы бронхиолы не спадались при вдохе, они располагаются внутри легочной паренхимы, которая за счет эластической тяги расправляется при вдохе и расширяет бронхи. Кроме того, в хрящевых бронхах мышечная оболочка не столь мощная, как в бронхиолах, в стенке мало сосудов, и каждый бронх имеет адвентицию. В стенках мелких бронхов много сосудов и отсутствует адвентиция [7].
Эпителиальная выстилка трахеи и бронхов образована многорядным реснитчатым эпителием с бокаловидными, промежуточными и базальными клетками. Указывается также на наличие нейроэндокринных клеток. На уровне сегментарных бронхов толщина эпителия составляет от 37 до 47 мкм. Собственная пластинка слизистой оболочки трахеи и бронхов уплотнена и образует отчетливую базальную мембрану, толщина которой колеблется от 3,7 до 10,6 мкм. Ткань, расположенная глубже, называется подслизистой основой. В нее погружены секреторные отделы многочисленных белково-слизистых желез, расположенные в треугольнике между двумя хрящами [8].
Белковослизистые железы являются дериватом секреторных клеток слизистой оболочки воздухоносных путей и функционально взаимосвязаны с ней. Железы имеют альвеолярно-трубчатую структуру и состоят из ацинусов, содержат серозные и слизистые клетки, расположенные на базальной мембране. Серозные клетки имеют призматическую форму, эллипсоидное ядро и пиронинофильную цитоплазму. Белковослизистые железы выделяют смешанный белково-мукополисахаридный секрет, в котором преобладают муцины. Секреция осуществляется по мерокриновому и апокриновому типам. Выводные протоки желез выстланы мерцательным кубическим однослойным эпителием, расположенным на базальной мембране; в стенке протоков содержится сеть эластических волокон. По периферии подслизистых желез расположены соединительная ткань, подразделяющая их на дольки, а также скопления лимфоидных клеток (особенно в области протоков), единичные макрофаги, тучные клетки, плазмоциты. Между эпителиальными клетками и базальной мембраной располагаются миоэпителиальные клетки, сокращение которых способствует выведению секрета из концевых отделов желез, протоки которых открываются на внутренней поверхности трахеи и бронхов [9].
Структурная организация всех слоев стенки воздухоносных путей обеспечивает три основные функции: барьернозащитную с обеспечением мукоцилиарного клиренса, контроль за калибром бронхов и бронхиол, механическую стабильность воздухоносных путей.
Эпителиальная выстилка воздухоносных путей здорового человека включает следующие разновидности клеток: реснитчатые (РК), секреторные (бокаловидные) (СК), переходные, или промежуточные (ПК), базальные (БК), нейроэндо-кринные (НЭК) (рис. 1-2) [10].
При изучении поверхности эпителиального пласта воздухоносных путей человека и экспериментальных животных был выявлен ряд закономерностей [11, 12]:
---вопервых, все клетки эпителиальной выстилки воздухоносных путей имеют на своей апикальной поверхности микроворсинки - небольшие выросты цитоплазмы. Наличие этих структур способствует увеличению поверхности эпителиального пласта, соприкасающегося с жидким надэпителиальным секреторным покрытием, и указывает на возможность всасывания путем эндоцитоза жидкой части секрета из просвета бронхов;
---вовторых, межклеточные контакты плотные и представлены в виде валикообразных структур или черепицеобразных наложений, что обеспечивает непрерывность эпителиальной выстилки и позволяет ей выполнять барьернозащитную функцию;
---в-третьих, распределение, а следовательно, и соотношение реснитчатых и секреторных клеток в разных областях эпителиальной выстилки структур одного и того же калибра неодинаковое в продольном направлении и по периметру бронхов или бронхиол. Так, в бесхрящевой части трахеи и по всему периметру слизистой оболочки бесхрящевых бронхов отчетливо выражена ее складчатость в результате сокращения гладкой мускулатуры в этой зоне. В эпителиальном пласте таких зон преобладают реснитчатые клетки, на долю которых приходится до 70 - 80%, а иногда и все 100%. В тех местах, где по периметру трахеи и бронхов содержатся хрящевые полукольца или пластинки, поверхность эпителиальной выстилки ровная, без складок. В эпителии бронхов были выявлены зоны с разным соотношением реснитчатых и секреторных клеток: 1) с преобладанием реснитчатых клеток (до 80%), чаще соотношение СК:РК составляет 1:4 или 1:7; 2) с почти равным соотношением реснитчатых и секреторных клеток; 3) с преобладанием секреторных и микроворсинчатых клеток; 4) с полным или почти полным отсутствием реснитчатых клеток, которые можно назвать «безреснитчатыми».
В эпителиальной выстилке трахеи и бронхов располагаются антигенпредставляющие дендритные клетки и межэпителиальные лимфоциты.
На поверхности эпителиальной выстилки воздухоносных путей в норме встречаются единичные макрофаги, лимфоциты, полиморфноядерные лейкоциты, капельки, комочки, дисковидные и войлокообразные структуры секрета.
path: pictures/01-02.png
Рис. 1-2. Клеточный состав эпителиальной выстилки слизистой оболочки бронха.
I - надклеточное жидкое покрытие, II - многорядный мерцательный эпителий, III - базальная мебрана, IV - собственная пластинка слизистой оболочки, V - мышечная пластинка слизистой оболочки, РК - реснитчатая клетка, СК - секреторная (бокаловидная) клетка, БК - базальная клетка, ПК - переходная клетка, НЭК - нейроэндокринная клетка, ДК - дендритная клетка, НО - нервное окончание, КК - кровеносный капилляр, ТК - тучная клетка, ГМ - гладкомышечная клетка, м - макрофаг, л - лимфоцит, п - перицит, ф - фибробласт (по Л.К. Романовой, 2000 [5]).
Дата добавления: 2015-01-18 | Просмотры: 2532 | Нарушение авторских прав
1 | 2 | 3 | 4 | 5 | 6 | 7 | 8 | 9 | 10 | 11 | 12 | 13 | 14 | 15 | 16 | 17 | 18 | 19 | 20 | 21 | 22 | 23 | 24 | 25 | 26 | 27 | 28 | 29 | 30 | 31 | 32 | 33 | 34 | 35 | 36 | 37 | 38 | 39 | 40 | 41 | 42 | 43 | 44 | 45 | 46 | 47 | 48 | 49 | 50 | 51 | 52 | 53 | 54 | 55 | 56 | 57 | 58 | 59 | 60 | 61 | 62 | 63 | 64 | 65 | 66 | 67 | 68 | 69 | 70 | 71 | 72 | 73 | 74 | 75 | 76 | 77 | 78 | 79 | 80 | 81 | 82 | 83 | 84 | 85 | 86 | 87 | 88 | 89 | 90 | 91 | 92 | 93 | 94 | 95 | 96 | 97 | 98 | 99 | 100 | 101 | 102 | 103 | 104 | 105 | 106 | 107 | 108 | 109 | 110 | 111 | 112 | 113 | 114 | 115 | 116 | 117 | 118 | 119 | 120 | 121 | 122 | 123 | 124 | 125 | 126 | 127 | 128 | 129 | 130 | 131 | 132 | 133 | 134 | 135 | 136 | 137 | 138 | 139 | 140 | 141 | 142 | 143 | 144 | 145 | 146 | 147 | 148 | 149 | 150 | 151 | 152 | 153 | 154 | 155 | 156 | 157 | 158 | 159 | 160 | 161 | 162 | 163 | 164 | 165 | 166 | 167 | 168 | 169 | 170 | 171 | 172 | 173 | 174 | 175 | 176 | 177 | 178 | 179 | 180 | 181 | 182 | 183 | 184 | 185 | 186 | 187 | 188 | 189 | 190 | 191 | 192 | 193 | 194 | 195 | 196 | 197 | 198 | 199 | 200 | 201 | 202 | 203 | 204 | 205 | 206 | 207 | 208 | 209 | 210 | 211 | 212 | 213 | 214 | 215 | 216 | 217 | 218 | 219 | 220 | 221 | 222 | 223 | 224 | 225 | 226 | 227 | 228 | 229 | 230 | 231 | 232 | 233 | 234 | 235 | 236 | 237 | 238 | 239 | 240 | 241 | 242 | 243 | 244 | 245 | 246 | 247 | 248 | 249 | 250 | 251 | 252 | 253 | 254 | 255 | 256 | 257 | 258 | 259 | 260 | 261 | 262 | 263 | 264 | 265 | 266 | 267 | 268 | 269 | 270 | 271 | 272 | 273 | 274 | 275 | 276 | 277 | 278 | 279 | 280 | 281 | 282 | 283 | 284 | 285 | 286 | 287 | 288 | 289 | 290 | 291 | 292 | 293 | 294 | 295 | 296 | 297 | 298 | 299 | 300 | 301 | 302 | 303 | 304 | 305 | 306 | 307 | 308 | 309 | 310 | 311 | 312 | 313 | 314 | 315 | 316 | 317 | 318 | 319 | 320 | 321 | 322 | 323 | 324 | 325 | 326 | 327 | 328 | 329 | 330 | 331 | 332 | 333 | 334 | 335 | 336 | 337 | 338 | 339 | 340 | 341 | 342 | 343 | 344 | 345 | 346 | 347 | 348 | 349 | 350 | 351 | 352 | 353 | 354 | 355 | 356 | 357 | 358 | 359 | 360 | 361 | 362 | 363 | 364 | 365 | 366 | 367 | 368 | 369 | 370 | 371 | 372 | 373 | 374 | 375 | 376 | 377 | 378 | 379 | 380 | 381 | 382 | 383 | 384 | 385 | 386 | 387 | 388 | 389 | 390 | 391 | 392 | 393 | 394 | 395 | 396 | 397 | 398 | 399 | 400 | 401 | 402 | 403 | 404 | 405 | 406 | 407 | 408 | 409 | 410 | 411 | 412 | 413 | 414 | 415 | 416 | 417 | 418 | 419 | 420 | 421 | 422 | 423 | 424 | 425 | 426 | 427 | 428 | 429 | 430 | 431 | 432 | 433 | 434 | 435 | 436 | 437 | 438 | 439 | 440 | 441 | 442 | 443 | 444 | 445 | 446 | 447 | 448 | 449 | 450 | 451 | 452 | 453 | 454 | 455 | 456 | 457 | 458 | 459 | 460 | 461 | 462 | 463 | 464 | 465 | 466 | 467 | 468 | 469 | 470 | 471 | 472 | 473 | 474 | 475 | 476 | 477 | 478 | 479 | 480 | 481 | 482 | 483 | 484 | 485 | 486 | 487 | 488 | 489 | 490 | 491 | 492 | 493 | 494 | 495 | 496 | 497 | 498 | 499 | 500 | 501 | 502 | 503 | 504 | 505 | 506 | 507 | 508 | 509 | 510 | 511 | 512 | 513 | 514 | 515 | 516 | 517 | 518 | 519 | 520 | 521 | 522 | 523 | 524 | 525 | 526 | 527 | 528 | 529 | 530 | 531 | 532 | 533 | 534 | 535 | 536 | 537 | 538 | 539 | 540 | 541 | 542 | 543 | 544 | 545 | 546 | 547 | 548 | 549 | 550 | 551 | 552 | 553 | 554 | 555 | 556 | 557 | 558 | 559 | 560 | 561 | 562 | 563 | 564 | 565 | 566 | 567 | 568 | 569 | 570 | 571 | 572 | 573 | 574 | 575 | 576 | 577 | 578 | 579 | 580 | 581 | 582 | 583 | 584 | 585 | 586 | 587 | 588 | 589 | 590 | 591 | 592 | 593 | 594 | 595 | 596 | 597 | 598 | 599 | 600 | 601 | 602 | 603 | 604 | 605 | 606 | 607 | 608 | 609 | 610 | 611 | 612 | 613 | 614 | 615 | 616 | 617 | 618 | 619 | 620 | 621 | 622 | 623 | 624 | 625 | 626 | 627 | 628 | 629 | 630 | 631 | 632 | 633 | 634 | 635 | 636 | 637 | 638 | 639 | 640 | 641 | 642 | 643 | 644 | 645 | 646 | 647 | 648 | 649 | 650 | 651 | 652 | 653 | 654 | 655 | 656 | 657 | 658 | 659 | 660 | 661 | 662 | 663 | 664 | 665 | 666 | 667 | 668 | 669 | 670 | 671 | 672 | 673 | 674 | 675 | 676 | 677 | 678 | 679 | 680 | 681 | 682 | 683 | 684 | 685 | 686 | 687 | 688 | 689 | 690 | 691 | 692 | 693 | 694 | 695 | 696 | 697 | 698 | 699 | 700 | 701 | 702 | 703 | 704 | 705 | 706 | 707 | 708 | 709 | 710 | 711 | 712 | 713 | 714 | 715 | 716 | 717 | 718 | 719 | 720 | 721 | 722 | 723 | 724 | 725 | 726 | 727 | 728 | 729 | 730 | 731 | 732 | 733 | 734 | 735 | 736 | 737 | 738 | 739 | 740 | 741 | 742 | 743 | 744 | 745 | 746 | 747 | 748 | 749 | 750 | 751 | 752 | 753 | 754 | 755 | 756 | 757 | 758 | 759 | 760 | 761 | 762 | 763 | 764 | 765 | 766 | 767 | 768 | 769 | 770 | 771 | 772 | 773 | 774 | 775 | 776 | 777 | 778 | 779 | 780 | 781 | 782 | 783 | 784 | 785 | 786 | 787 | 788 | 789 | 790 | 791 | 792 | 793 | 794 | 795 | 796 | 797 | 798 | 799 | 800 | 801 | 802 | 803 | 804 | 805 | 806 | 807 | 808 | 809 | 810 | 811 | 812 | 813 | 814 | 815 | 816 | 817 | 818 | 819 | 820 | 821 | 822 | 823 | 824 | 825 | 826 | 827 | 828 | 829 | 830 | 831 | 832 | 833 | 834 | 835 | 836 | 837 | 838 | 839 | 840 | 841 | 842 | 843 | 844 | 845 | 846 | 847 | 848 | 849 | 850 | 851 | 852 | 853 | 854 | 855 | 856 | 857 | 858 | 859 | 860 | 861 | 862 | 863 | 864 | 865 | 866 | 867 | 868 | 869 | 870 | 871 | 872 | 873 | 874 | 875 | 876 | 877 | 878 | 879 | 880 | 881 | 882 | 883 | 884 | 885 | 886 | 887 | 888 | 889 | 890 | 891 | 892 | 893 | 894 | 895 | 896 | 897 | 898 | 899 | 900 | 901 | 902 | 903 | 904 | 905 | 906 | 907 | 908 | 909 | 910 | 911 | 912 | 913 | 914 | 915 | 916 | 917 | 918 | 919 | 920 | 921 | 922 | 923 | 924 | 925 | 926 | 927 | 928 | 929 | 930 | 931 | 932 | 933 | 934 | 935 | 936 | 937 | 938 | 939 | 940 | 941 | 942 | 943 | 944 | 945 | 946 | 947 | 948 | 949 | 950 | 951 | 952 | 953 | 954 | 955 | 956 | 957 | 958 | 959 | 960 | 961 | 962 | 963 | 964 | 965 | 966 | 967 | 968 | 969 | 970 | 971 | 972 | 973 | 974 | 975 | 976 | 977 | 978 | 979 | 980 | 981 | 982 | 983 | 984 | 985 | 986 | 987 | 988 | 989 | 990 | 991 | 992 | 993 | 994 | 995 | 996 | 997 | 998 | 999 | 1000 | 1001 | 1002 | 1003 | 1004 | 1005 | 1006 | 1007 | 1008 | 1009 | 1010 | 1011 | 1012 | 1013 | 1014 | 1015 | 1016 | 1017 | 1018 | 1019 | 1020 | 1021 | 1022 | 1023 | 1024 | 1025 | 1026 | 1027 | 1028 | 1029 | 1030 | 1031 | 1032 | 1033 | 1034 | 1035 | 1036 | 1037 | 1038 | 1039 | 1040 | 1041 | 1042 | 1043 | 1044 | 1045 | 1046 | 1047 | 1048 | 1049 | 1050 | 1051 | 1052 | 1053 | 1054 | 1055 | 1056 | 1057 | 1058 | 1059 | 1060 | 1061 | 1062 | 1063 | 1064 | 1065 | 1066 | 1067 | 1068 | 1069 | 1070 | 1071 | 1072 | 1073 | 1074 | 1075 | 1076 | 1077 | 1078 | 1079 | 1080 | 1081 | 1082 | 1083 | 1084 | 1085 | 1086 | 1087 | 1088 | 1089 | 1090 | 1091 | 1092 | 1093 | 1094 | 1095 | 1096 | 1097 | 1098 | 1099 | 1100 | 1101 | 1102 | 1103 | 1104 | 1105 | 1106 | 1107 | 1108 | 1109 | 1110 | 1111 | 1112 | 1113 | 1114 | 1115 | 1116 | 1117 | 1118 | 1119 | 1120 | 1121 | 1122 | 1123 | 1124 | 1125 | 1126 | 1127 | 1128 | 1129 | 1130 | 1131 | 1132 | 1133 | 1134 | 1135 | 1136 | 1137 | 1138 | 1139 | 1140 | 1141 | 1142 | 1143 | 1144 | 1145 | 1146 | 1147 | 1148 | 1149 | 1150 | 1151 | 1152 | 1153 | 1154 | 1155 | 1156 | 1157 | 1158 | 1159 | 1160 | 1161 | 1162 | 1163 | 1164 | 1165 | 1166 | 1167 | 1168 | 1169 | 1170 | 1171 |
|